Yarn Conditioning Process:
In which process yarn is conditioned for better performance (such as strength, serviceability, luster, handle etc) is called yarn conditioning. Yarn conditioning is a great technique to improve physical properties of yarn and mechanical performance of yarn especially cotton yarn. In spinning process yarn conditioning machine is used to adjust the moisture of yarn and to improve efficiency in the next process. It also affects performance of subsequent processes such as weaving and knitting.
The presence of moisture in the mill atmosphere has a significant impact on the physical properties of fibers and yarns. High-speed spinning machines generate more friction, thus giving additional heat to the yarn and as a result of such heat transfer the yarn moisture content is vaporized. For quality reasons, it is absolutely important to have even distribution of this recuperated moisture throughout the entire yarn package. The two parameters such as relative humidity and temperature will decide the amount of moisture in the atmosphere.
The increase in the relative atmospheric humidity causes a rise in the moisture content of the cotton fiber. The maintenance of high degree of moisture improves the physical properties of yarn. The correct follow-up of R.H% in different departments of spinning mill is very crucial, which influences the trouble-free running and dust-free environment in subsequent process. Higher R.H% tends to increase roller lapping tendency in many departments. Lower R.H% tends to drop in strength value and increase in dust liberation. The fiber strength and elasticity increase proportionately with the increase in humidity. If the water content of the cotton fiber is increased, the fiber is able to swell, resulting in increased fiber-to-fiber friction in the twisted yarn structure.
Humidification needs are not only for getting a good working during production, but also to ensure that the material is made suitable for further working. During spinning and winding, the yarn package runs at a high speed, because of which the moisture in the yarn is thrown out. The normal moisture in ring spun cops and cone winding shall be around 4.5–5.0%. To have a good working in warping or knitting, the yarn should have moisture of above 7%. The commercial moisture regain considered for overseas market is 8.5%, whereas in the mills, it is very difficult to get that moisture content. To get the advantage of moisture content, people started keeping high humidity in winding section by installing mist humidifiers. This resulted in the rusting of machine parts, but the moisture in the cone did not increase. The cones were remaining dry as the cones were put in polythene bags immediately after doffing to avoid handling stains. Then the system of keeping cones in a humidified room for 24 hr was started, which only added the space problem, but the cones did not absorb moisture as they were tightly built to have higher yarn content on cones and to have higher container capacity to reduce transportation costs.
The yarns made for hosiery is normally waxed, which also is a hindrance for the yarn to absorb moisture. By keeping cones in a humidified room for a long time gave higher moisture content in the outer surface of cones, but not uniformly inside the cone. Some even tried subjecting cones to direct steam at different pressures. The imbedded air in between the fibers and yarns had no place to come out, which was also a hindrance to moisture absorption.
There used to be condensation of water droplets at the surface of cones and in the polythene bags, but the moisture was not entering the core of the yarn. It increased the problems rather than reducing. The yarn conditioning plants and auto claves were designed to give moisture to the yarn by force.
Yarn conditioning machine as shown in Figure 1 is basically closed vessel capable of producing saturated steam at very low pressure. The machine produces vacuum that facilitates even penetration of steam into the layers of yarn package.
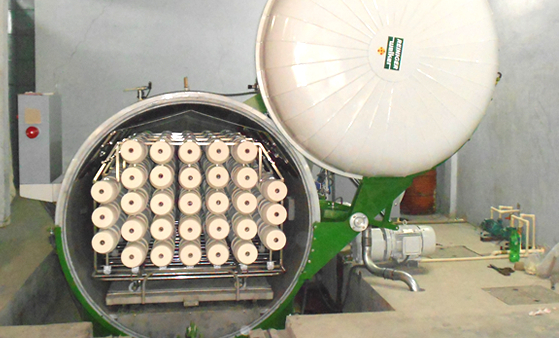
The cones are kept in an enclosed chamber, which shall first be made vacuum by a vacuum pump. By this, the trapped air between fibers and yarns are taken out. Afterwards live steam would be allowed to enter the chamber. As the air has been removed, the water molecules can enter the cavity in the fibers, and the absorption of moisture becomes more effective.
Effects of Conditioning of Yarn:
The following effects would be envisaged by steam-conditioning of yarn:
- Twist Setting – Preventing Snarling (yarn loops)
- Better Dye affinity – Eliminating static electricity
- Influencing the Cloth handle – Preventing crease-proneness
- High bulking – Humidifying
- Dye – fixing – De-crinkling
- Determining residual boiling shrinkage.
You may also like:
- What is Yarn | Types of Yarn
- Yarn Specifications and Quality Parameters
- Fancy Yarn: Types, Properties, Manufacturing Process and Application
- What is Yarn Twist | Twist Direction | Twist Level
- Yarn Count System and Determination by Different Methods