Garment Costing:
Cost accounting is a structure of determination of costs of products or services. Costing is the technique and process of estimating the cost for a product or service or process. Costing of the garment and textile product is a complex problem, it involves numerous number of activities associated with each product. The technique and methods to be used for ascertainment of cost vary from unit to unit depending upon the nature of the industry, type of the product, method of production and the meaning or the sense in which the term cost is used.
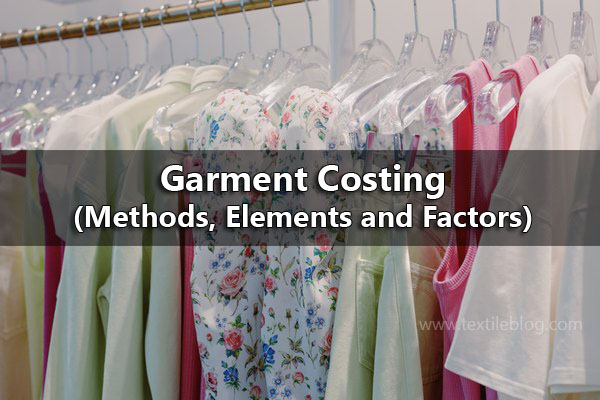
In garment industry, the process of costing a product is very dynamic. Since, the fashion changes every season and sometimes very often, the product which the manufacturing company receives for manufacturing from the buyer also differs every season. Most of the time, the products are manufactured only once. This leads the manufacturing company to work on accurate costing on every product in order to run the business profitable.
Globalization, which has shortened the world’s distance, impacted the garment industry a lot because it is a massive labor-dependent and tech-savvy industry. Although the world has come closer spatially, the garment industry’s supply chain has gone multidimensional, which practically means that it is almost impossible to incorporate all the processes under one roof, so various companies opt to outsource some of the activities / processes. The process outsourcing may be in the same or different country, depending on the lead time requirement. As globalization has opened newmarkets to stimulate trade, especially in garment industry, companies are moving their operations to low-cost countries to compete with their counterparts on cost. The impact of international outsourcing on the practice of costing and labor cost is significant. Due to deficient resources (resource scarcity) and technological know-how, each country is not competent in producing the garments up to the same standards and matching the cost by their counterparts. In this article I will discuss methods of garment costing, elements of garments costing and factors of garment costing.
Methods of Garment Costing:
Costing is the operation for ascertaining the total resource investment essential to manufacture and market a product. Costing includes:
- Determination of variable and non-variable material cost and labor cost necessary to manufacture a product
- Overhead required to operate the industry
- General operating cost
For efficient costing, information related to cost must be specific and accurate. Inaccurate costing could lead to cancellation of an order having good profit potential. Management in an organization utilities costing to estimate
- The producibility of a style within an established price range
- The profit potential in a style
- To decide whether a style could be added to the line
Costing could also be used to defend the procurement of new machinery or the extension of production facilities. The method of costing indicates the systems and processes involved in the estimation of costs and it depends on the type and nature of manufacturing activity. The two basic methods of costing are
- Job costing: This is the cost estimation for a particular work order where the estimation of cost was carried out separately.
- Process costing: This method is practiced in bulk manufacturing units where cost is accumulated for each department.
Product costing needs in-depth knowledge in materials, product development, production processes and plant operations. The costs involved in manufacturing a product are only taken into account in product costs. Two kinds of product costing are generally used in the garment industry, such as absorption costing and direct costing. Manufacturing costs are separated between variable manufacturing costs and nonvariable manufacturing costs. Direct costing and absorption costing are included in variable manufacturing costs, but only absorption costing is included in nonvariable manufacturing costs.
Absorption costing:
Absorption costing comprises every single manufacturing cost, both variable and nonvariable, to be product costs that should be allocated to products. Overhead is generally calculated as a percentage of direct labor. The estimation of a sensible overhead application rate is a major drawback in absorption costing. Further, it is also difficult to concentrate on the actual variable costs and profit prospective related to a particular product. Factory overhead costs that do not differ with deviations in volume are included as part of cost of products produced with absorption costing. Industries repeatedly project the anticipated total overhead for the particular period based on the past year’s costs and expected changes.
The risks connected with using absorption costing are the dependency of the costing system on the accuracy of the estimation of direct labor and the determination of the overhead application, which is arbitrary. For these two reasons, direct costing is mostly recommended for cost ascertainment in place of absorption costing.
Direct costing:
Marginal cost is the increase in the total production cost that results from manufacturing one more unit of output and variable costs. Direct costing is a theory that takes into account only the variable costs like labor, material costs and sales commission to be product costs. Nonvariable costs, namely, manufacturing and nonmanufacturing, are treated as time period costs.
A direct costing system gives information about costing in a way that can be easily understood and used by management. Since the individual product costs are obviously identified, direct costing makes it easier to evaluate the cost of production and the contribution of product to nonvariable sewing and administrative costs and profit. Direct costing makes it easier to categorize the product styles with the highest contribution rate and the most profit potential.
Elements of Garments Costing:
Elements of costing are direct material, direct labor and direct expenses (Figure 2).
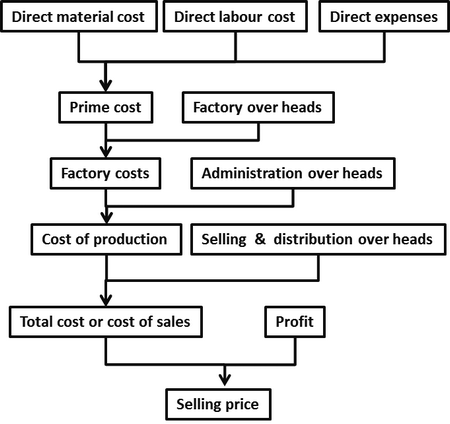
Direct materials:
Direct materials are all the materials and trimmings which go into the construction and finish of the garment. Typically, these materials would include cloth, lining, sewing threads, fusible, buttons, zips, pads, tapes, labels, hangers and packaging materials and so forth.
Direct labor:
This covers the cost of all the labor directly involved in producing the garment and could include cutting, fusing, regular sewing, special machine operations, pressing, finishing, inspection and packing. Labor of all types and grades has a direct overhead, which includes holiday pay, sick pay, fringe benefits and so forth, and the statutory payments made by the employer for each employee. This is usually expressed as a percentage of salary and when this percentage is added to the employee’s wage, it becomes the basis for calculating direct labor costs.
Factory overhead:
There are different methods of calculating the factory overhead, but most of them use a combination of the following three elements:
- Indirect labor: This covers every person in the factory who does not directly perform a production operation, such as managers, supervisors, engineers, store personnel, clerks, maintenance staff, porters, canteen staff security and cleaners and so forth.
- Expenses: Included in this element is every fixed and variable expense incurred in operating the factory, such as rent, rates, utilities, insurance, depreciation, maintenance, air conditioning and the various types of energy generation required by a clothing factory.
- Indirect materials: Also known as consumables, this element contains all the materials not directly connected to the make-up of a garment. Some of the typical items involved are office materials, spare parts, marker paper, maintenance materials, chalk and pins.
The total of these three elements is the factory overhead and because it cannot be conveniently applied to specific cost units, it is generally expressed as a percentage of the direct labor costs. For example, if the costs for a given period are:
- Direct labor Tk. 28 000 (including direct overhead)
- Factory overhead Tk. 33 600
The factory overhead is 120% of the cost of direct labor. From this, it is simple to calculate the cost of 1-min work for every production operator:
- Labor rate/h Tk. 6.00
- Factory overhead at 120% Tk. 7.20
- Total cost Tk. 13.20
- Cost/min Tk. 0.22
Therefore, the price of an operation is the rate/min multiplied by the time allowed for the operation.
General overhead:
The general overhead comprises of all the labor costs and expenses which are incurred in running the company, such as management, marketing, finance, insurance, warehousing, rent and utilities. The design department costs are usually allocated to this component.
Again, because of the practical difficulties of apportioning this component to specific cost units, it is expressed as a percentage of the total for direct labor factory overhead and direct materials, as in this example, where all the costs are for the same period:
- Direct materials Tk. 84 000
- Direct labour Tk. 28 000
- Factory overheads at 120% Tk. 33 600
- Total Tk. 1 45 600
- General overhead Tk. 65 520
Therefore, conveniently, the general overhead is 45% of all the other costs. Therefore, the framework of garment costing would be the sum total of these four components.
Factors Influencing the Garment Costing Process:
In continuation to the cost elements, it is essential to know and understand the fundamental factors which affect the cost of the apparel products. An apparel product cost or price includes cost of various activities like fabric purchase, dyeing, cutting, sewing and packing, transportations and other overhead expenses. Hence, the cost of the product will always fluctuate time to time based on other factors.
The cost of the apparel product also will vary style to style. Since the style complexity decides the number of operations in each process, the cost always changes with styles. The various components of an apparel cost are as follows:
- Type of fabric
- Trims type and numbers
- Cutting, making checking and packing charges
- Value added services–printing, embroidery, washing, appliqué
- Testing of the garment
- Quality parameters expected
- Transportation and logistics cost
- Profit of the manufacturing organization.
Other than these factors, there are few other things which will affect the cost of an apparel product directly. They are described below.
a. Fabric cost:
Fabric is generally the most significant factor in costing of garment. Fabric accounts for 60%–70% of the total cost of basic-styled garments.The cost of fabric depends upon the type of fabric that is going to be utilised in the garment. Types of fabrics are:
- Woven/knitted fabric
- Power loom/automatic loom fabric
- Fiber/yarn/fabric dyed fabric
- Fiber content of fabric i.e. cotton, wool, polyester, silk, blended fabric, etc.
- Type of dyeing and finish used
- GSM/Weight of fabric
- Type of yarn used i.e. ring spun, open ended, or carded/combed, etc.
b. Unit of Measurement (UoM):
The another important information which a merchandiser should be aware for different raw materials. Sometimes, the cost associated with the raw material depends upon the unit of availability.
c. Fabric Minimum Order Quantity (MOQ):
This is the information about the minimum or smallest quantity of any raw material which can be bought from vendors. The MOQ plays the important role while ordering the fabric as it directly affects the cost of garment. If the order of fabric is below the estimated MOQ then vendor charges more cost as compared to regular charges. Merchandisers need to keep the MOQ in mind while doing the costing of small quantity orders.
d. Order quantity:
The cost of the material majorly depends upon the quantity ordered. Higher the order quantity, lesser will be the cost of any material (comparatively).
e. INCOterms (International commercial terms):
The type of agreement between the buyer and seller with respect to commercial aspects also a major criteria which decides the cost of the product.For example, FOB pricing, FAS pricing, etc.
References:
- Apparel Manufacturing Technology By T. Karthik, P. Ganesan and D. Gopalakrishnan
- Apparel Merchandising by R. Rathinamoorthy and R. Surjit
- Fashion Marketing Management by A. Arunraj and V. Ramesh Babu
- Garment Manufacturing Technology Edited by Rajkishore Nayak and Rajiv Padhye
You may also like: Costing Techniques in Apparel Industry