Costing procedure of apparel is very critical task. Because costing a single piece of clothing there are lot things to do. In order to gain perfect apparel costing, responsible person must know about all the activities including purchasing of raw materials, sewing, knitting, dyeing, printing, packing, transport, overheads, cost of trimmings & accessories used all are included in it. And also should know about their costs, procedures, advantages & risk factors. Generally, apparel merchandiser and the top management of an apparel company are actively involved in deciding the cost of apparel. Apparel industry follows different techniques to determine the cost. In this article I will discuss different apparel costing techniques. And also point out requirements of a good costing system at the last of this article.
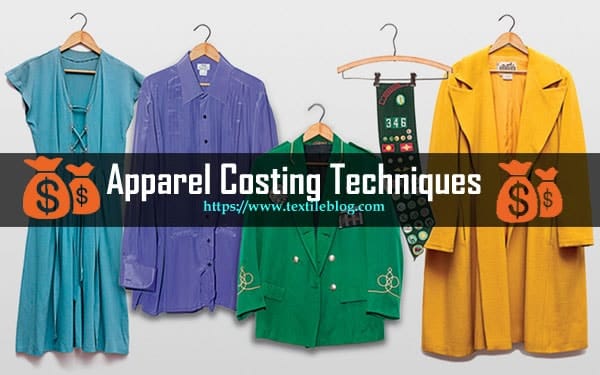
Costing Techniques in Apparel Industry
At first we have to know that costing techniques should not be confused with methods of costing. Techniques of costing to be used depend on the nature and purpose of the information required by the management. Management may require different type of cost information for the purpose of control, decision making, price determination and forward planning for profit. Thus the desired technique of costing is used in conjunction with an appropriate method of costing.
The following costing techniques are adapted in the apparel manufacturing companies:
1. Total or absorption costing:
In this method, the entire cost is absorbed into individual units where both the fixed and variable costs are charged to production. Such type of technique is also called full costing.
2. Marginal costing:
In this method, only variable costs are taken into account and fixed costs are written against profits in the period in which they arise. This is also called as partial costing.
Marginal costing represents the change in the aggregate cost resulting from variation in volume of output by one unit. This type of costing is an important managerial tool for decision making. This is called direct costing. As it takes into account only variable costs which can be charged direct to production.
3. Standard costing:
This is a technique of cost control where costs are predetermined on the basis of management’s standard of efficient operation. These pre-determined costs are called standard costs. Actual costs are compared with standard costs and remedial action is taken in case the former exceed latter. Standard costing not only serve as a yardstick to measure efficiency but also provide a basis for price fixation.
4. Budgetary control:
This is an important managerial tool for planning and control. A budget is an overall financial plan for future activities. It seeks to co-ordinate and control the use of resources for a specific period. Budgetary control involves establishment to the requirements of budgets relating to responsibilities of executives to the requirements of a policy, comparison of actual performance with budgeted performance and prompt remedial action when former falls short of the latter. Budgetary control may be described as forward costing as it seeks to control the future activities of the concern through the establishment of budgets.
5. Activity based costing:
Nowadays companies try to adapt their offers and terms to different buyers. Thus an apparel manufacturer will negotiate different terms with different retail chains, meaning the cost and profits will differ with each chain. To estimate the real profitability of dealing with different retailers, the apparel manufacturer needs to use Activity Based Cost (ABC) accounting instead of standard cost accounting. ABC accounting tries to define the real costs associated with serving different customers. Both the variable costs and the overheads costs must be tagged back to each customer. Companies that fail to measure their costs correctly are not measuring their profit correctly & they are likely to misallocate their marketing effort. Identifying the true costs arising in a customer relationship also enables a company to explain the charges better to the customer.
6. Target costing:
Costs change with production scale and experience. They can also change as a result of a concentrated effort by the company’s designers, engineers and purchasing department to reduce them. Many Japanese companies use a method called Target costing. Firstly they use market research to establish a new product’s desired functions. Then they determine the price at which the product will sell given its appeal & competitor’s price. They eliminate the desired profit margin from this price and this leaves the target cost they must achieve. Next, the firm examines each cost element – design, textile engineering, garment manufacturing, sales and break them down into further components, looking for ways to reengineer components, eliminate functions and bring down the supplier costs. The objective is to bring the final cost projections into the target cost range. If they cannot succeed, they may decide against developing the product because it could not sell for the target price & make the target profit. When they can succeed, profits are likely to follow.
Requirements of a Good Costing System:
The costing system adopted by an organization should have the following requirements:
- It must fit with the requirements of the business.
- It must be simple, effective and sufficiently elastic.
- It must enable an easy collection and classification of expenditure relating to productive and non-productive services as well as of general on cost.
- It must give prompt, accurate, reliable and comprehensive cost relating to operation, process and output units in all their constituting elements.
- It must admit easy comparison with predetermined estimates and with cost of similar jobs previously performed in the company.
- It must present reliable data in sufficient details to enable future estimates to be prepared and the sales price to be fixed with due regard to the fluctuations in expenses.
- It must provide for the maintenance of cost records and statistical data in a well arranged, classified and analytical form of all manufacturing and other expenses so as to serve for further references & guidance.
- The costing system should not be unduly expensive and cumbersome.