Main purpose of garments manufacturer is to make a profit. So, it is very essential to estimate product cost for a successful business. Estimation of factory cost includes all the activities like purchase of fabrics and accessories, processing and finishing of fabrics, cutting, sewing, packing of garments, transport, shipping, overheads, banking charges, commissions, insurance and among others. Costing of garment is generally estimated by the merchandiser who is responsible for that’s specific garment item. So, merchandiser must have to know about all these process thoroughly about their costs, procedures, advantages & risk factors.
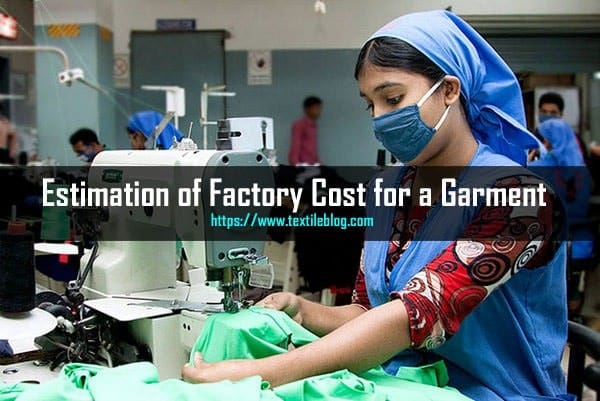
Estimation of Factory Cost for a Garment:
The estimation of factory cost for a garment involves the following steps:
- Calculation of garment weight (for any one size)
- Calculation of fabric cost per kg.
- Calculation of fabric cost per garment.
- Garment costing process
1. Calculation of garment weight (for any one size):
The garment weight for any one size-normally the middle size of the all sizes in an order inquiry is calculated. For example, if there are 3 sizes S, M, L then the M size weight is taken for calculation. The garment weight can be calculated with formula.
2. Calculation of fabric cost per kg:
If the fabric for the garment order is purchased directly from the market which may be readily available, then the price per kg of the fabric is taken as fabric cost per kg. If the fabric for the garment order is made specifically, then the fabric cost per kg is calculated as follows:
Fabric cost per kg:
Particulars | Amount (Tk) |
Yarn price / kg | xxx |
Knitting rate / kg | xxx |
Dyeing rate / kg | xxx |
Printing rate / kg | xxx |
Compacting rate / kg | xxx |
Heat setting rate / kg (for synthetic fabric) | xxx |
Total | xxx |
Process loss (8-10%) | xxx (+) |
Fabric cost per kg | xxx |
3. Calculation of fabric cost per garment:
Fabric cost per garment is obtained by multiplying garment weight and fabric cost per kg.
Fabric cost per garment = Garment weight x Fabric cost per kg
4. Garment costing process:
The cost of the garment is calculated as follows:
Particulars | Amount | |
Fabric cost per garment | xxxBDT | |
Cost of Making (CMT) cost | xxxBDT | |
Special operations (embroidery, garment printing etc) | xxxBDT | |
Accessories | Amount (BDT) | xxxBDT |
Buttons, zippers, twill tape | xxx | xxxBDT |
Main label | xxx | |
Wash care label | xxx | |
Poly bag/Pouch | xxx | |
Hang tag | xxx | |
Insert card | xxx | |
Barcode sticker | xxx | |
Hologram sticker | xxx | |
FOB + Packing (Re. 1 per 30 gms of garment) | xxxBDT | |
Sub total | xxxBDT | |
Overhead (10%) (+) | xxxBDT | |
Sub total | xxxBDT | |
Rejection 3% (+) | xxxBDT | |
Sub total | xxxBDT | |
Profit% (+) | xxxBDT | |
Sub total | xxxBDT | |
Agent’s commission | xxxBDT | |
Insurance | xxxBDT | |
Garment price (FOB) in BDT | xxxBDT | |
Garment price (FOB) in US$ | Price in BDT/1 US$ rate | |
Garment price (FOB) in Euro | Price in BDT/1 Euro rate |
Though costing is a critical and most important task in apparel business. I have tried to explain above process with very simple way. After reading this post I think you understand how to estimate factory cost for garments. If you have any query about this article then please let me know, I will try to give answer.