In textile industry, quality is the most important thing. So maintaining quality control in textile is a supreme priority task for textile engineers. To me it seems like my own heart and it’s really true that it’s like same as me to everyone related to textile industry. Because we all know the slogan that is “Quality first”.
Suppose you go to a tailor shop and order a custom white shirt for your upcoming job viva. You give all the requirements to the tailor master for your desired shirt but in the end when you get the shirt you feel that it is not in the perfect shape you had mentioned in your requirements. That means tailor cannot meet the level of your requirements. From this coincident we can understand that how important the fact of quality is. Because in industry they deals with the bulk amount of production. So, from this we can easily define the term quality.
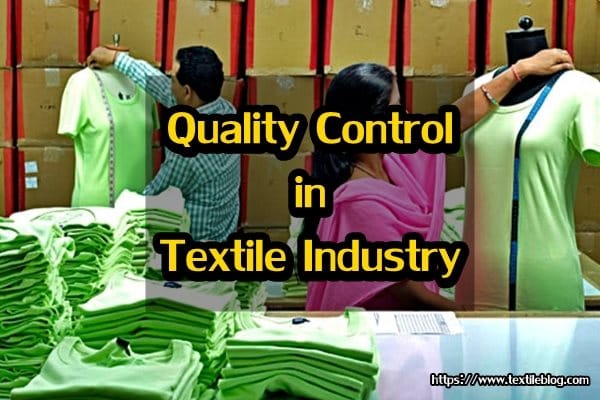
What is Quality?
Quality may be defined as the level in which manufacturers can finely meet the requirements of a buyer.
Or, we may define it as the Features of a product which can sharply meet the buyer’s demands.
Important Aspects of Quality:
There are some aspects of quality. Most importantly 9 aspects of quality is given bellow:
1. Performance:
This term actually refers to the accurate features of a product or we can say that the desired satisfaction point of a product to the customer.
2. Reliability:
It may be defined as the mentioned features or functions of a product is fulfill it’s committed features in during time period.
3. Durability:
The durability of a product is may be defined as the assurance of a product that how long the product will be usable for the customers.
4. After sales service:
It means extra pleasure service after sales. Nowadays this is one of the best ways to increase selling with the proper customer pleasure.
5. Innovative Features:
Customer’s choice has no boundary they need more and more new design or they give more and more new requirements. Innovative features are aspects that can try to fulfill the customer satisfaction.
6. Conformance:
Conformance refers to the accurate specifications. It define that how finely a product or service meet the design and customers.
7. Aesthetics:
Many customer are very much concern about the amazing fashion or style. Aesthetics is one of the important aspects of quality.
8. Perceived quality:
To maintain the perceived quality by the requirements is one of the most important aspects of quality.
9. Maintainability:
This is also same as after sales service. Maintenance or servicing agreement with customers is amazingly increasing the quality of a product.
Fundamental Factors Affecting Quality:
1. Customers:
Customers are the destination of a product. Mainly they are the last user of a product. Because of that the entire quality unit should have to be focus on customer factor.
2. Manufactures:
In the industry the types of raw materials used and packing materials used in the production by the specifications is a concern. Nowadays in the modern quality managements point out that management board and materials both are cordially responsible for quality.
3. Employee:
In time during employee plays a great role to delivering a good quality product. Very specifically employees think as the internal customers of their product. So that they can be satisfied with the end product as a point of view of customers.
4. Materials:
To get a good quality product the role of supplied raw material is a big factor. Without good quality raw materials there is no way to meet the good quality product.
Quality Control:
Quality is the first priority of a iconic business or brand. To assure the quality we have to follow the quality control procedure.
Quality control may be defined as the process or system by which we can check and verify the perfection of product characteristics by given requirements.
In garment industry quality control process keeps up from the initial stage of collecting raw materials to the final finished garments.
If there is any fraud in any step of a whole process then it would not be easy to get a good quality product.
Objectives of Quality Control:
- To assure the buyers requirements
- Make a good product impression
- Create a brand value
- Assure the customer’s satisfaction
Types of Quality Control:
Mainly two types of quality control system followed in our industries. These are:
1. Process control:
When a product is on process line the quality control system applied step by step in during process time to meet the excellence of end product this is known as process control.
2. Product control:
This system is applied after production process. This system is used for decreasing faulty product within different lots of manufactured good.
You may also like: 4 Point System for Fabric Inspection with Example
Here we can classify process control in two types. These are:
1. On-Line Quality control:
When the process of a production is going on this type of quality control system is performed. In during this quality control system production doesn’t need to stop. It automatically performs during the process time and detects the fault and takes urgent steps to correction. We can say it is an automatically quality control system.
2. Off line Quality control:
These types of control are done by stopping the production process and in a laboratory. Detected faults are correct by the step of test results.
Quality is the identity of a last product. It is the most important thing of matter. In Bangladesh different garments industry they follow different types of management and quality control system. Whatever it is, everything is for a good quality end product. Without good quality industry will never create brand value or product impression or we can say industry will never shine or survive in this sector easily.
Quality Control in Textile and Apparel:
In our daily life we use different types of garments product like shirt, pant, t-shirt etc. Always when we buy any product we try to aware about the quality. Because by spending money we don’t want to get the bad quality product. But we actually don’t know the hidden quality specification of a product. We always buy a product by judging the level or brand tag. The brand provides us the product they have a quality control team. In the production process they inspect whole process of production and detect the faults and resolve it urgently. A quality controller assure that there is no fault in a product. Because nowadays customers are very much concern about their product quality. We need quality control to meet the buyers or customers satisfaction level. To assure the right uses of raw materials. To reduces defects and increase quality of product. To make a good bonding between buyers and customers. To added brand value. To survive in the competitive market place. Low quality product can not be acceptable by the customers or buyers. It takes more time to deliver a product. Bad quality decreases the production. Decreases of brand value just because of low quality product. So a quality controller team try to maintain the best quality of a product. Without quality control a industry never survive in the market. We should have to be focused on maintain the perfect quality of a product.
References:
- https://www.cleverchecklist.com/blog/thoughts/quality-productivity/
- https://www.researchgate.net/publication/301789034_QUALITY_MANAGEMENT_IN_GARMENT_INDUSTRY_OF_BANGLADESH
- https://textilelearner.net/basic-concept-of-quality-in-apparel-industry/
- https://study.com/academy/lesson/what-is-quality-control-in-textile.html
- https://www.cleverism.com/lexicon/product-quality/
Author of this Article:
Asif Hasan Mim
Daffodil International University
Department of Textile Engineering
E-mail: asifhasanmim16@gmail.com