What is Textile Printing?
The word ‘printing’ is derived from Latin, meaning ‘pressing’, and implies the process in which pressure is applied during the printing process. Textile printing is the process of applying designs, patterns, or images to fabric or other textiles. Printing can be considered as “localized dyeing”. Usually printing is performed on one side of the textile. The purpose of textile printing is to produce high-quality, vibrant prints that can be used for a variety of purposes, such as clothing, home décor, and promotional products. In this article I will discuss different types of textile printing processes.
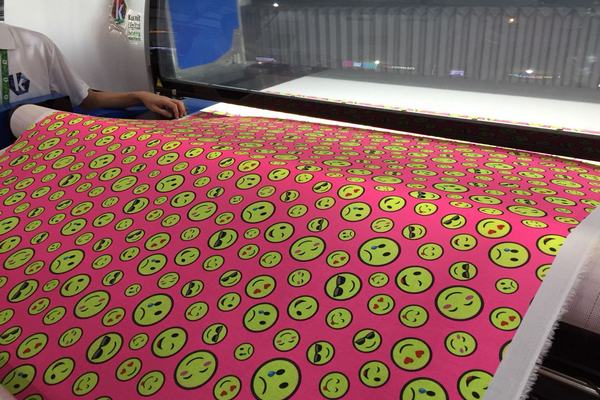
Different Types of Printing in Textile Industry:
- Screen printing
- Block printing
- Roller printing
- Transfer printing
- Digital Printing / Ink-jet printing
- Stencil printing
- Burn-out printing
- Special printing techniques
Above types of textile printing processes are described below:
A. Screen printing:
Screen printing is a type of textile printing that involves pushing ink through a stencil or screen onto fabric. The screen printing is the most commonly used printing method in textile industry.
Screen printing is a versatile printing method that can be used to produce a wide range of designs on a variety of materials, including fabric, paper, plastic, and more. Screen printing involves passing the print paste onto a fabric through a mesh or screen which has some open and some blocked areas according to the desired print pattern. The print design obtained on the fabric depends on the pattern of the open areas of the screen.
Types of screen printing in textile industry:
There are two main types of screen printing in textile industry:
- Flat-bed screen printing and
- Rotary screen printing.
Advantages of Screen Printing:
- Screen printing creates a long-lasting, durable print that can withstand wear and tear.
- It can be used on a variety of surfaces and materials, including paper, fabric, plastic, and metal.
- This printing method is cost-effective for large runs and is more affordable than other printing methods for bulk orders.
- It provides precise ink coverage and consistent results, which is particularly important for logos and designs that require fine details.
- Screen printing allows for the use of a wide range of inks, including metallic and fluorescent colors, resulting in bright, vibrant prints.
- It produces sharp and clean lines, making it suitable for printing fine details and text.
- Screen printing is highly customizable and can be used to produce unique, one-of-a-kind designs.
Disadvantages of Screen Printing:
- Screen printing requires a significant investment in equipment, supplies, and setup costs.
- Limited in the number of colors that can be used in a single design, as each color requires a separate screen.
- It is a time-consuming process, particularly when preparing the screens and setting up the equipment.
- Screen printing is not suitable for small runs, as the setup costs can be prohibitively expensive.
- It can be inefficient for multi-color designs, as each color requires a separate printing process.
- Limited color accuracy
- Not suitable for photographic images
B. Block Printing:
The block printing is a method of printing which involves the use of wooden blocks with raised printing surface, which are inked and then pressed on to the fabric. Block printing is an ancient form of printing that has been used for thousands of years and is still used today, particularly for creating textiles and stationery items. Block making required patience and skill. A fairly hard wood was required, such as pearwood, and four or five layers were usually glued together with the grain running in different directions.
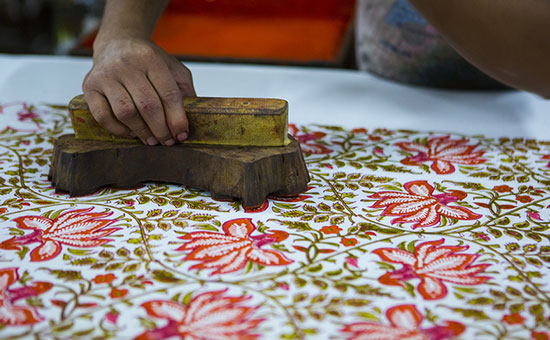
Advantages of Block Printing:
- Simple to operate.
- Don’t require expensive equipment.
- Multi-colors design can be produced.
- There is no limiting factor in repeat unit.
Disadvantages of Block Printing:
- Slow method, low output and Costly.
- It involves manual work and hence quite laborious.
- Not possible to obtain sharp out lines of design.
- Difficult to join up each impression or repeat perfectly.
C. Roller printing:
Roller printing or engraved-roller printing is a type of machine printing that involves the use of cylindrical rollers to transfer ink onto fabric or other materials. The rollers are coated with the desired ink color and then pressed against the material, transferring the ink to create a design or pattern. Roller printing is a continuous printing process, making it suitable for producing large quantities of printed fabric in a short amount of time.
Advantages of Roller Printing:
- Suitable for large scale production.
- High speed, hence more production.
- Used for fine printing.
- High quality design.
- No joint mark.
- Possible to print in complex weave design.
Disadvantages of Roller Printing:
- Changing time high. So not suitable in small scale production.
- Engraving the printing roller is an expensive operation.
- May be light printing shade.
- May produce crush effect.
D. Transfer printing:
Transfer printing is a printing process in which an image or design is printed onto a transfer paper, which is then applied to a fabric or other material using heat and pressure. Transfer printing is often used to produce high-quality images or designs on textiles, ceramics, and other materials.
Transfer printing is the term used to describe textile and related printing processes in which the design is first printed on to a flexible nontextile substrate and later transferred by a separate process to a textile.
Advantages of Transfer Printing:
- Standard printing can be done by this printing.
- No need of after treatment or washing.
- Produced fabric is not stiff.
- The degree of wastage is very small.
- Suitable for knitted fabric.
- The cost of the equipment is comparatively low.
Disadvantages of Transfer Printing:
- Only volatile dye can be used.
- There is extra step of 1st working on paper.
- Once the transfer printing paper has been used it cannot be used.
- Costly process
E. Digital Printing:
Digital printing is a process of printing designs and patterns directly onto fabric using digital printing technology. The process involves printing the design directly onto the fabric using specialized inkjet printers, which deposit tiny droplets of ink onto the fabric. Digital inkjet printing is one of the most modern ways of printing textile fabrics. This method can be used for most of the commercially available fabrics. This printing process has become increasingly popular in recent years due to its ability to produce high-quality, full-color designs in a short amount of time.
Advantages of Digital Ink-jet Printing:
- No limitations of number of colors.
- Large repeats are possible.
- Saving of expensive printing materials.
- Low energy consumption.
- Flexibility-individual, exclusive design.
- Eco-friendly wastage.
- Optimum surface appearance results.
Disadvantages of Digital Ink-jet Printing:
- Machine is not commercially available.
- Initial investment is high.
- Printing speed is limited.
- Pretreatment are necessary before printing.
- Very skilled persons are required for operating.
- It may create blockage in jet nozzles.
F. Stencil printing:
Stencil printing is a printing process that uses a stencil as a mask to transfer ink or paint onto a material. The stencil is cut to the desired design, and ink or paint is then applied to the stencil and pressed onto the material. The ink or paint only passes through the open areas of the stencil, creating the desired design on the material.

Advantages of Stencil Printing:
- Stencil is much easier handle than the block.
- The cost of production is low, profitable for small scale production.
- Possible to produce various shade effect.
- Any kind of color can be used in stencil.
Disadvantages of Stencil Printing:
- Complete circular/rings can’t be obtained and designer’s freedom is limited.
- Complex design is not suitable.
- Not suitable for large scale production.
- It involves manual work and hence laborious.
G. Burn-out printing:
Burn-out is the removal of fibers from a fabric. Burn-out prints involve printing with a chemical substance that destroys the fiber in a designed pattern of print area. It is also called devour printing. This printing technique is used to create unique, semi-transparent designs on fabric, often with a vintage or distressed look. Burn-out printing is popular in the fashion industry for creating distinctive and eye-catching garments.
Advantages of Burn-out Printing:
- Burn-out printing is used to make fashion dresses and decorative purposes.
- No special or costly machine is required.
- Novel design can be produced.
Disadvantages of Burn-out Printing:
- If the process not properly controlled the whole fabric will be damaged.
- May impair tensile strength & stability of fabric.
- It can’t be corrected.
- The highly concentrated chemicals are harmful to operator and machinery.
- Only blended fabrics can be printed.
H. Special printing techniques:
i. Non-fabric printing:
Printing techniques can be applied also on pre-stages in textile production, e.g. sliver yarn, warp beams, thus leading to special irregular patterns.
ii. Flock printing:
Flock printing is a representative for techniques where an adhesive is printed in the first stage. In the second step, an effect material is fixed to the adhesive.
In case of flock print, short staple fibers (flocks, 0.3–3 mm) are fixed on the adhesive layer by means of an electrostatic field (20–60 kV) which also orients the fibres in direction perpendicular to the fabric surface, thereby a velvet-like surface structure is obtained.
iii. Batik printing:
In the classical processes, a wax was printed on the fabric to form a resist. After dyeing with usual dyeing procedures, the resist was removed. In a special case indigo was used for dyeing. During dyeing of the fabric the waxy layer cracks and the cracks become marked with dye, which leads to the characteristic appearance of this article.
iv. Two-phase printing:
In two-phase printing, the pattern printing and dyestuff fixation processes are separated into two stages. As an example after printing of a reactive dye and intermediate drying, the print is fixed in a continuous process through padding in rather concentrated alkali solution. Similarly, vat dyes can be printed and fixed in the reducing agent.
References:
- Textile Printing (Revised Second Edition) Edited by Leslie W C Miles
- An Introduction to Textile Coloration: Principles and Practice By Roger H. Wardman
- Textile Engineering – An Introduction Edited by Yasir Nawab
- Textile Chemistry By Thomas Bechtold and Tung Pham
You may also like:
- Study on Printing of Cotton Fabric with Direct Dyes
- Application of Automation in Textile Printing and Finishing
- 9 Unique Ideas for Custom T-Shirt Printing