Introduction:
In any production organization has main goal to manufacture quality product with short time and less cost. Apparel industry is undergoing enormous change. Due to the increased competition and survival in the market, garment manufactures must design production systems that are able to respond to customer demands as soon as possible, minimize production costs and produce a cheap product. As a result increasing pressure on retailers and manufacturers. They have to complete production not just in terms of price, but also in delivery times and services offered. So they have to follow a specific production system. Like other industries, garment manufacturing industry have own production organization systems.
Production Organization Systems in Garment Industry:
In industrial garment manufacturing, there are three main systems of production organization. These are mention in below:
- Synchronized system
- Section system
- Progressive bundle system
1. Synchronized system or Straight-line system:
The synchronized or straight line system is suitable for large volume production (mass production or large batches). As the name suggests, the work flow in a straight line through a series of work stations, each of which is synchronized to the next by ensuring that the time spent at each station is exactly the same. This required that each individual step in the assembly of the product has to be analyzed carefully and the steps distributed in a balanced way over the available work stations. Each operator then performs exactly the same operation over and over again on the identical parts of successive garments. Detailed work plans have to be drawn up to facilitate this balancing of the line.
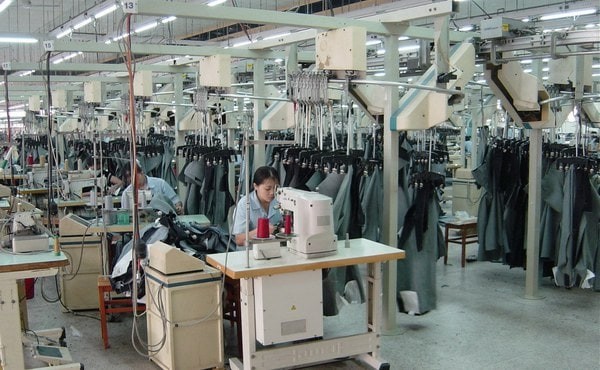
Advantages:
- Synchronized line system includes short distance between stations.
- Low volume of work in process.
- Precise planning of production times.
- Highly visible production progress and predicting production quantity.
Disadvantages:
- It includes the need for intensive detailed pre-planning.
- High cost of style changes.
- Sensitivity to disruption by production difficulties or absenteeism.
- The dependence of productivity on maintaining a strict rhythm of work.
2. Section or process system:
This system is used by factories with frequent style changes and small numbers of items per style. The sewing room has a number of sections, each of which specializes in the assembly of a major garment component. Then it is passed on to the next section. The spatial arrangement of the sections is such that the output end of the one section is close to the input end of the section which requires that component.
Advantages:
- Semi skilled, skilled, trainee labors can be work here.
- The advantages of this system include a small influence of personnel changes and easy style changes.
- labor cost is low from the individual system.
- Productivity is higher from the individual system.
Disadvantages:
- It include large space requirement.
- To continue this simple operation, high skilled operators are required.
- Imprecise production time planning and longer throughout time.
- They need more WIP, which increases the inventory cost.
- More possibility to mix up of lost, shade variation, sizes, etc. so, apparel quality and production will be hampered.
3. Progressive bundle system or batch system:
The progressive bundle system of garment assembly embraces some of the features and advantages of both the straight-line and the section systems. machine and operatives are organized into sections, according to basic functions, which produce sub-components e.g. small parts, sleeves, pockets, joining. Within each section the work is balanced according to the time required for each sub-function. The combination of small bundles and a line system provides the best solution to the problems of frequent style changes, small lot sizes, and short delivery deadlines.
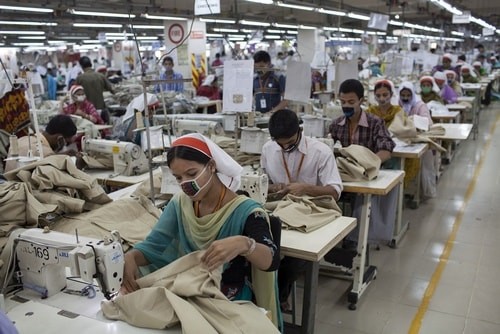
Advantages:
- In this system all types of labors are involved like, unskilled, skilled, and semi skilled labors.
- Very cheap labor cost.
- Every component is checked during operation. So, product quality is good.
- Bundles are moved from one operation to next operation so; lot mix-up, shade variation, size variation, etc are not happened.
- Increase the productivity.
- Quality control and production control system easily implemented here. Use Time study, method study techniques, operator training, material handling equipments etc.
Disadvantages:
- Line balancing is difficult.
- Maintenance of machine and its equipment is properly needed.
- Actual production planning is required. If the planning is wrong then increase labor turnover, poor quality, less production.
- For this system different types of styles and less quantity are not suitable.
- To balance the line, for each batch shuttle and utility operators are needed.
- Proper layout should be needed for smooth flow of material.
Besides, new methods of modern organization of production can be Just-in-Time, Toyota Production Systems, Total Quality Management and Lean Production.
JIT (Just-in-Time):
JIT stands for “Just-in-Time.” It is a production and inventory management philosophy that aims to minimize inventory and production costs by producing and delivering goods or services at the exact time they are needed.
JIT is an economic term that represents the strategy of reducing costs in the production of clothing where the calculation helps to achieve less storage of basic textile materials (lining, interlining, thread, buttons, etc.), i.e. raw materials or just avoiding the storage of finished garments. This tends to flexible production for a known customer, without storage, it shortens the time of making clothes, synchronizes the technological process of work and balances capacities.
In order to make JIT method successful in garment industry, many requirements must be met, such as:
- Quality.
- Minimal inventory.
- Reliable and solid cooperation relationship with suppliers.
- Suppliers located near the company, with reliable transportation available.
- Production size in correlation with demand.
- Team work, employees responsible for maintaining their equipment, bosses, coaches and mentors respect their employees and participate in the production process actively.
- Customer satisfaction.
Toyota Production System (TPS):
One of the most successful models for solving problems in production management is the Toyota Production System (TPS). TPS is a set of well-known techniques and methods for solving problems, the philosophy about responsible behaviour and returning of values to customers, employees, properties and society.
TQM (Total Quality Management):
TQM (Total Quality Management) is applied in order to improve effectiveness, efficiency, flexibility and competitiveness.
Basic principles of TQM are,
- Quality can and must be managed.
- All employees are responsible for the quality.
- Problems must be prevented, not just fixed.
- Quality must be controlled.
- Improving the quality must be a continuous process.
- Objectives are based on customer requirements.
- Management must be involved.
- Improving the quality requires planning and organization.
Lean production:
Lean manufacturing is a systematic approach that aims to eliminate waste and improve efficiency throughout the production process. It involves identifying and eliminating non-value-added activities or processes to streamline operations. Lean principles, such as value stream mapping, continuous improvement, and standardized work, are applied to optimize the garment production process and enhance overall productivity. Lean manufacturing refers not only to production, but also to all other functions within the business systems, as well as relationships with manufacturers.
Conclusion:
Efficient production organization systems are crucial in the garment industry to optimize productivity, reduce costs, and meet customer demands. Implementing effective systems such as lean manufacturing, computer-aided design, and automated production processes can significantly enhance efficiency and competitiveness in the industry.
References:
- Apparel Manufacturing Technology by T. Karthik, P. Ganesan, D. Gopalakrishnan
- Industrial Engineering in Apparel Production By V. Ramesh Babu
- Management of Technology Systems in Garment Industry by Gordana Colovic
You may also like:
- Garment Manufacturing Process: Step by Step Section Wise
- Efficiency and Productivity of Sewing Line
- Productivity Improvement Techniques in Garment Industry
- Line Balancing in Garment Industry
- How to Calculate Production Capacity of a Garment Factory
Your article is very inspiring with high-quality content. We are sure that you will find additional useful information on our website. Come on, visit us at Jasa Konveksi Bandung and we can collaborate with each other.
Warm Regard.