Study on Efficiency and Productivity of Sewing Line
Authors:
Md. Rakibul Islam Apurba1
Kanig Silvia Zerin
Sakibur Rahman Rony
Dept. of Textile Engineering
Daffodil International University, Dhaka, Bangladesh
Email: apurba13.ani@gmail.com1
ABSTRACT
This project is on “Study on Efficiency and Productivity of Sewing Line”. Traditionally operated garment industries are facing problems like low productivity, longer production lead time, high rework and rejection, poor line balancing, low flexibility of style changeover etc. In this paper, we have collected 10 days data from the industry. In the data, we have showed here target production, actual production, working hour, SMV, manpower, machine quantity. From that we have calculated the target efficiency, actual efficiency, machine productivity, labor productivity, the variance between the actual efficiency and the target efficiency. We have showed here all this data what we have collectedfrom industry in 12 line for 10 days. Also we have showed here how to calculate the target efficiency, actual efficiency and machine productivity, labor productivity. Numerous developments and handlings are drilled by the administrators which are superfluous. In this paper, we have seen the target efficiency and the actual efficiency of the day 1 have 43% and 42.8% and the last day that means day 10 target and actual efficiency have increased to 49.7% and 49.7%. So, here we have seen the variance of the first day and last day efficiency. And we have also showed here the summery of 10 days efficiency, where the target efficiency have 46.4% and the actual efficiency have also 46.4%. The summery of 10 days productivity have machine productivity 63.01 and labor productivity 44.01. Here we have also showed the graph of figure where we have seen the variance of the actual efficiency and the target efficiency easily. We have discussed here the result and discussion from this data and how to increase the efficiency and the productivity of the sewing line.
1. INTRODUCTION
1.1 Introduction
Presently a day’s Textile industry acquired a wonderful situation to upgrade the mechanical development and financial thriving. This industry assumes a noteworthy job to build the work potential just as to procure outside cash. Bangladesh is considered as one of the monetary rival in pieces of clothing fabricating. An assortment of pieces of clothing items are sent out from Bangladesh to everywhere throughout the world as it is considered as a 100 percent send out arranged area. In excess of 70 percent of remote income are gotten by readymade piece of clothing. Low work cost is one of the best extraordinary points of interest of this industry. As the worldwide monetary condition has changed quickly, attire makers has given more spotlight on client interest for top notch item and improved efficiency. The interest for more excellent item at lower cost is expanding. To make due in an undeniably focused attire industry, clothing makers need to improve the quality just as efficiency of the pieces of clothing activities through deformities minimization.
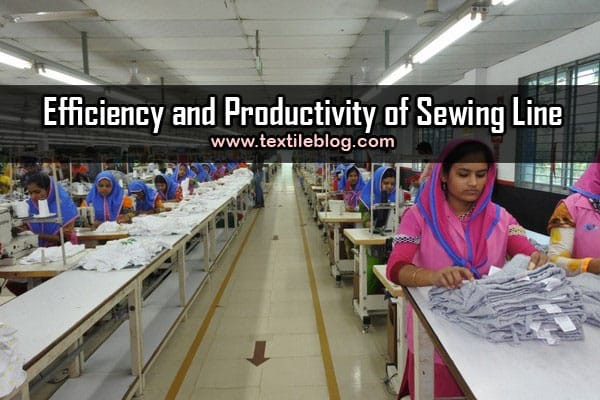
The greatest and the most fundamental portion in an article of attire industry is its sewing section. In this section each sewing machine and occupations of machine heads should be surveyed on an ordinary explanation behind perceiving changing and controlling of imperfections and keeping up nature of things. Sewing deficiencies are an issue generally looked by bit of garments makers. Still it being an outstandingly essential issue, it is incredibly hard to discard it completely. Amassing clothing is burdensome procedure since sewing line contains number of tasks. In this way working limit much of the time goes fluctuate from individual to individual. The initial step for improving the efficiency and quality is to distinguish the factors influencing and by diminishing these can without much of a stretch accomplish quality just as the creation in sewing line. As we probably am aware the monetary condition changing exceptionally quick it turns out to be progressively imperative to concentrate on starting venture as high challenge in the modern zone. Efficiency is assessed by accomplishment toward set up objectives dependent on connections among data sources and yields of industry. The exhibition of an operational arrangement for upgrading productivity was comprehended by a scientific investigation. Since, on shop floor, there might be many machines, representatives and a huge number of group subassemblies all at the same time dynamic.
2. LITERATURE REVIEW
2.1 Efficiency
Efficiency is the ability to avoid wasting materials, energy, efforts, money & time in doing something or in producing desired result. In a more general sense, it is the ability to do things well, successfully, and without waste. In more mathematical or scientific terms, it is a measure of the extent to which input is well used for an intended task or function (output). It often specifically comprises the capability of a specific application of effort to produce a specific outcome with a minimum amount or quantity of waste, expense, or unnecessary effort. Efficiency refers to very different inputs and outputs in different fields and industries.
Efficiency can often be expressed as a percentage of the result that could ideally be expected, for example if no energy were lost due to friction or other causes, in which case 100% of fuel or other input would be used to produce the desired result. [1]
2.1.1 Line Efficiency
Line Efficiency is a known term in the readymade articles of clothing division. Line effectiveness assumes a significant job to deliver target pieces of clothing generation. Typically it’s finished by modern designers. As its significance in articles of clothing fabricating.
Factory capacity is estimated according to operator efficiency or line efficiency. Hence, efficiency is one of the most used performances measuring tools.
2.1.2 Calculation Method of Efficiency
To calculate the efficiency of a line for a day, we will require the accompanying information (data) from the line chief or line recorder.
- Number of operators – what number of operators worked in the line in a day.
- Working hours (Regular and additional time hours) – how long every one of the operators worked or how long the line run in a day
- Production of pieces – what number pieces are delivered or absolute line yield toward the day’s end.
- Garments SMV– What is the accurate standard moment of the style (piece of clothing).
When we have above information we need to ascertain following utilizing above data –
- Total minutes produced by the line: To get absolute production minutes, multiply production pieces by garments SMV.
- Total minutes attended by all operators in the line: Multiply the quantity of administrators by every day working hours and convert absolute hours into all out minutes (duplicating by 60).
Now, calculation method of line efficiency –
2.1.2.1 SMV
SMV is characterized as the time which is permitted to play out work agreeably. Ordinarily it is communicated in minute worth. The full elaboration of SMV is Standard Minute Value. SMV term is comprehensively utilized in the pieces of clothing fabricating industry. SMV is otherwise called Standard Allocated Minute (SAM).
General formula of SMV:
SMV = Basic time + (Basic time x Allowance)
Where,
Basic time = Observed time x Rating
Allowance = Relaxation allowance + Contingency allowance + Machine Delay Allowance.
Rating = the pace or speed of activity at which the operator is playing out the activity.
Observed time = Observed time can be found when important to finish an activity. This observed time determined by stop watch. Ratting is an assessment of efficiency. This ratting is finished by the operator who is playing out the activity. It very well may be estimated by an onlooker who experienced in explicit employment which is being watched.
SMV of garments depends upon a good number of factors. They are as following-
- Type of garments
- Types of fabrics
- Garments size
- Garments design
- Difficulty of the processes
- Types of machine
- Types of technology
2.1.3 Target Efficiency
Target Efficiency is related to target production. In a garments section there have lots of line and every line produce same or different production. In a line the operator and helper produce a certain amount of production. Everyday in a line have some target to produce. These targets are given from IE department. They have to fulfil the target in every line. From these target production the target efficiency are calculated. The formula of target efficiency is,
2.1.4 Actual Efficiency
As target efficiency, the actual efficiency is also related to actual production. After given the target in a line they try to fulfil the target, but sometime they can’t fulfil these or sometime they produce more production than the target production. After working whole day the line produce as much production for a day that is the actual production. The actual efficiency is calculated from these actual production. The formula of the actual efficiency is,
2.1.5 Overall Efficiency
When operators are on the shop floor, sometimes they will work on the standard jobs, sometimes they will work on off-standard jobs and sometimes they may not be doing any job due to lost time (unavailability of work). In a day, each operator is given 8 or 10 standard hours for the work. The 8 or 10 hours shift time can be separated as standard work hours, off-standard work hours and lost-time hours. When the whole shift hours are used in the calculation, irrespective of how much time (hours) operators do an off-standard job and remain idle, it gives overall efficiency. When you calculate overall line efficiency, you don’t need to deduct any hours.
According to the hours they spend on these different type of activities their efficiency can be calculated as on-standard efficiency, off-standard efficiency. [2]
2.1.5.1 Calculation Method of Overall Efficiency
To calculate daily overall line efficiency, we need to measure how much hours (minutes) are produced by employees working on the line and how much time workers spent on the line for producing the output. The efficiency calculation will be done based on the line output data. Then use the below formula to calculate the line efficiency in percentage.
We need to know some data to calculate overall efficiency:
- Line output – Number pieces produced by the line. It may be of one style or more than one style.
- Garment SMV – Standard Minute Value of the garments.
- Manpower – Total manpower worked in the line including operators and helpers
- Shift hours – Total hours factory works in a day. [2]
2.1.6 On-Standard Efficiency
In a shift, operators attend 480 or 600 minutes (8 hours or 10 hours shift), but they may not always sewing garments. Sometimes operators wait for work due to external reasons or they do off-standard jobs (operations) in the 480 or 600 minutes duration. Reasons are like waiting for work, machine break-down, power failure, line setting, meeting, non-availability of trims and accessories. All these off-standards reduce operator’s real performance (efficiency level).
When operators are not working the standard jobs, they are simply not producing any garments or any minutes. That is why, to know the operator’s actual performance on the standard jobs, the operator’s efficiency is presented as On-standard efficiency.
The formula for calculating on-standard efficiency is same but attended time. In case, of overall efficiency calculation total produced minutes is divided by total attended minutes at work. But for the On-Standard efficiency calculation, total produced minutes is divided by total attended minutes at standard jobs. [3]
2.1.6.1 On-Standard Efficiency Calculation Formula
2.1.7 Difference between On-Standard Efficiency and Overall Efficiency
The On-standard efficiency of a line/operator will be higher than or equivalent to the Overall Efficiency. On the off chance that the worker chips away at the standard employment for the entire day, the On-standard productivity and Overall Efficiency worth will be equivalent.
In the event that, an operator does an off-standard occupation (spent some of the time in the off-standard employment), the On-standard efficiency will be higher than the general productivity.
Ascertaining the general proficiency (for a line or an administrator) is simpler contrasted with figuring the On-standard effectiveness, as to compute On-standard productivity, you have to gauge time spent on the standard occupation.
2.2 Target Production
Target Production is the amount of production, which should be produced by an operator or a line in a fix time that management desires. The time can be 8 or 10 hours what is also called shift.
2.2.1 Standard Time & Target Setting
Various associations don’t use standard time systems; target setting relies upon puzzle and experience. Establishment of Standard events and the progression of the best methodology to make is fundamentally crucial to improve benefit. Every association that wants to battle later on must get this. This graph clearly diagrams the favorable circumstances to assembling plant capability if standard events and all around made methodologies are used.
2.2.2 Time Study
A work estimation procedure comprising of cautious time estimation of the errand with a period estimating instrument, balanced for any watched difference from typical exertion or pace and to permit satisfactory time for such things as outside components, unavoidable or machine delays, rest to defeat weakness, and individual needs.” Time study is generally prominent and utilized technique for line adjusting and comprehending bottlenecks. One issue of time study is the Hawthorne Effect where it is discovered that workers change their conduct when they realize that their being estimated.
2.3 Productivity
Productivity is a measure of the efficiency and effectiveness to which organizational resources (inputs) are utilized for the creation of products and/or services (outputs). Productivity measurement is both a measure of input utilization and an assessment as to whether or not input utilization is growing faster than output.In the case of a garment manufacturing factory, “output” can be taken as the number of products manufactured, whilst “input” is the people, machinery and factory resources required to create those products within a given time frame. The key to cost-effective improvements in output – in “productivity” – is to ensure that the relationship between input and output is properly balanced.
3. METHODOLOGY
3.1 Data Collection
We have collected for 10 days data of garments sewing line. In there we followed 12 lines what was in 4th floor of the building. These operation sheet and its data was collected from FAR EAST KNITTING & DYEING INDUSTRY LTD. Here these sheet showed buyer name, style name, and number of machine in the line, number of operator and helper in a line. This sheet also showed SMV, Target, efficiency etc. Here in the line there was different types of machine used to sewing for different process of t-shirt. Such as, Plain Machine, Overlock machine, Flat lock Machine was most used.
3.2 Data Analysis
In data sheet we showed many things what was we followed in sewing line. There we followed target, actual production. After that we have calculated the target efficiency, actual efficiency, the variance of the target and actual efficiency, target gap and target gap%.
Here the enhancements in regards to capacity, efficiency, profitability and execution of the administrators just as the sewing line after the activities of strategy institutionalization, process improvement, line adjusting also, preparing occurred are expressed in the accompanying. Here we show the calculation of the Target Efficiency, Actual Efficiency, Line productivity, labor productivity from the data of line 1 into the day 1. In these way, we calculated the other days calculation and the result are shows in the data sheet.
Here we show the example calculation of line 1 of day 1 data.
3.2.1 Calculation of Target Efficiency
Here,
Target Production = 1500
SMV= 5.6
Working Hour = 10
Manpower (OP+HP) = (23+8) = 31
…….1500 * 5.6
= …………………….. * 100
……10* 60 * 31
……8400
= ……………. * 100
….18600
= 0.451 * 100
= 45.1%
So, the Target Efficiency of the line 1 of day 1 is 45.1%
3.2.2 Calculation of Actual Efficiency
Here,
Actual Production = 1490
SMV = 5.6
Total Working Hour = 10
Total Manpower (OP+HP) = (23+8) = 31
…….1490 * 5.6
= ………………… * 100
…..10 * 60 * 31
…….8344
= ……………. * 100
…..18600
= 0.449 * 100
= 44.9%
So, the Actual Efficiency of the line 1 of day 1 is 44.9%
The Variance of the Actual Efficiency and the Target Efficiency is,
= (44.9 – 45.1) %
= -0.2%
3.2.3 Calculation of Productivity
Here,
Line output = 1490
Total manpower (OP+HP) = (23+8) = 31
Total machine used = 21
3.2.4 Sewing Line Efficiency Data Sheet (Day 1)
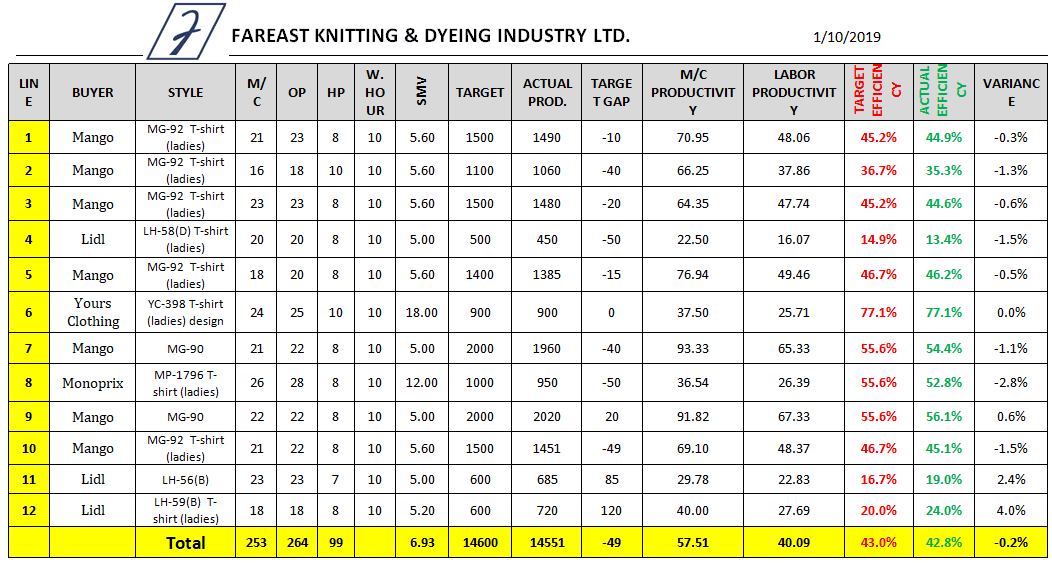
3.2.4.1 Sewing Line Efficiency Report (Day 1)
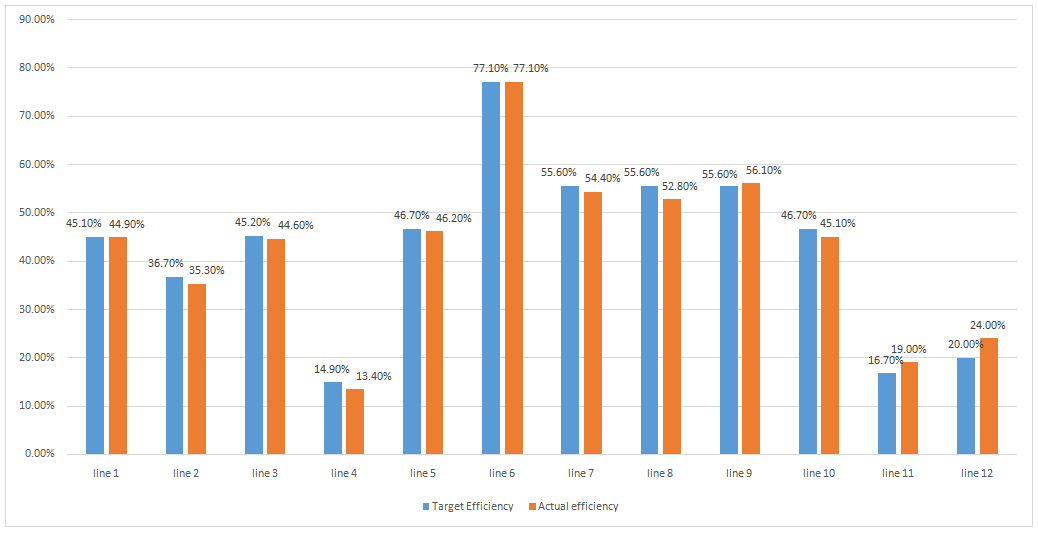
Here in this graph we can see the variance of the target efficiency and the actual efficiency of the line from day 1. In here different line produced different production and their target was also different. Here line 4, line 11 and line 12 efficiency was low because that was first day of that line for this type product.
3.2.5 Sewing Line Efficiency Data Sheet (Day 2)
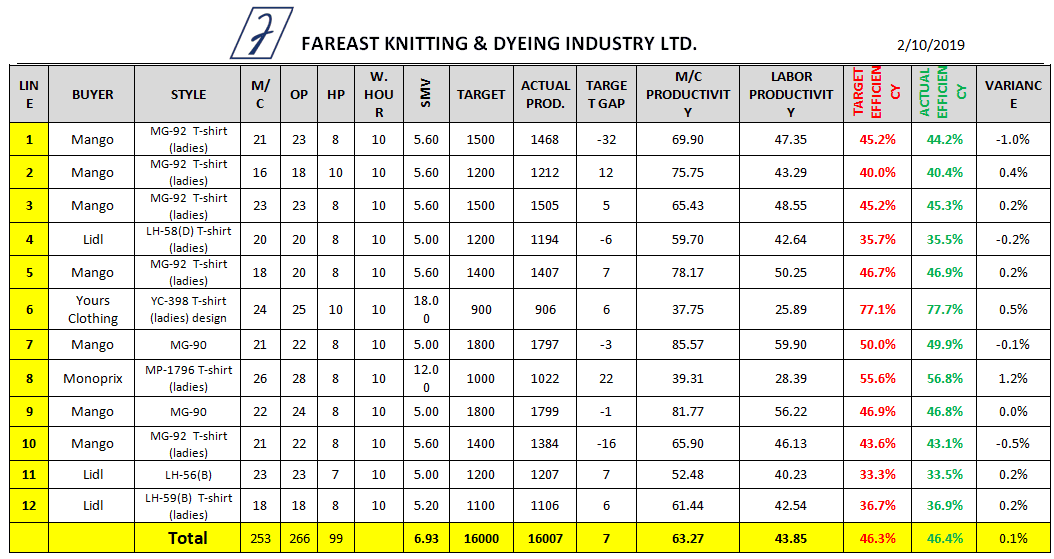
3.2.5.1 Sewing Line Efficiency Report (Day 2)
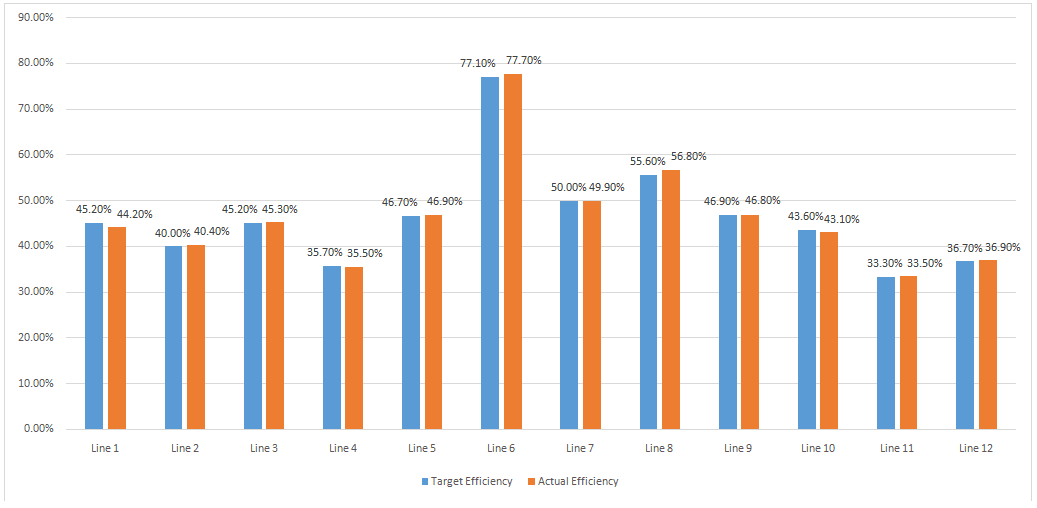
Here we showed the variance of target efficiency and the actual efficiency of different sewing line from day 2. Here different line had different efficiency. We can see here the line no. 11 was the lowest efficiency.
3.2.6 Sewing Line Efficiency Data Sheet (Day 3)
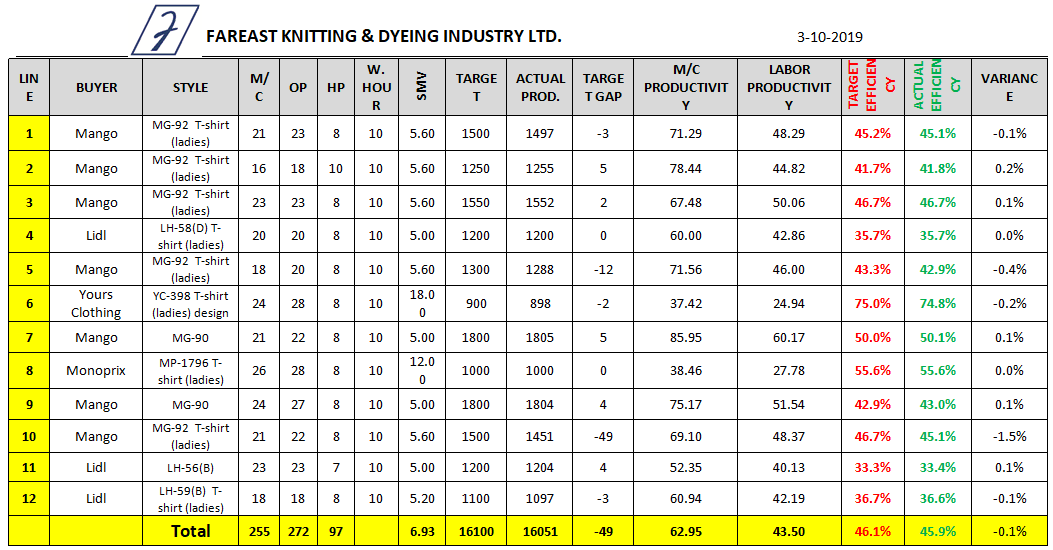
3.2.6.1 Sewing Line Efficiency Report (Day 3)
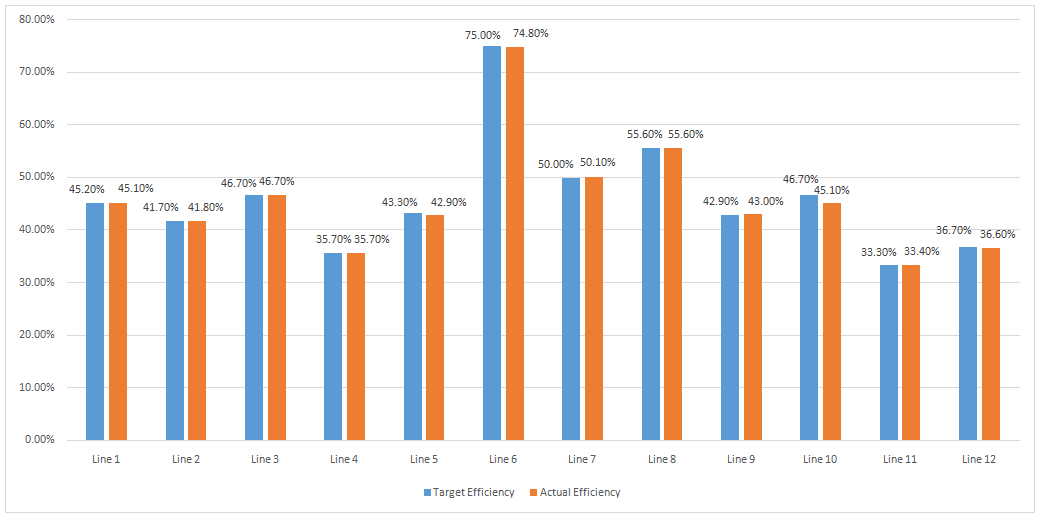
Here we showed the variance of target efficiency and the actual efficiency of different sewing line from day 3. Here different line had different efficiency. We can see here the most of the line efficiency was increased from previous day.
3.2.7 Sewing Line Efficiency Data Sheet (Day 4)
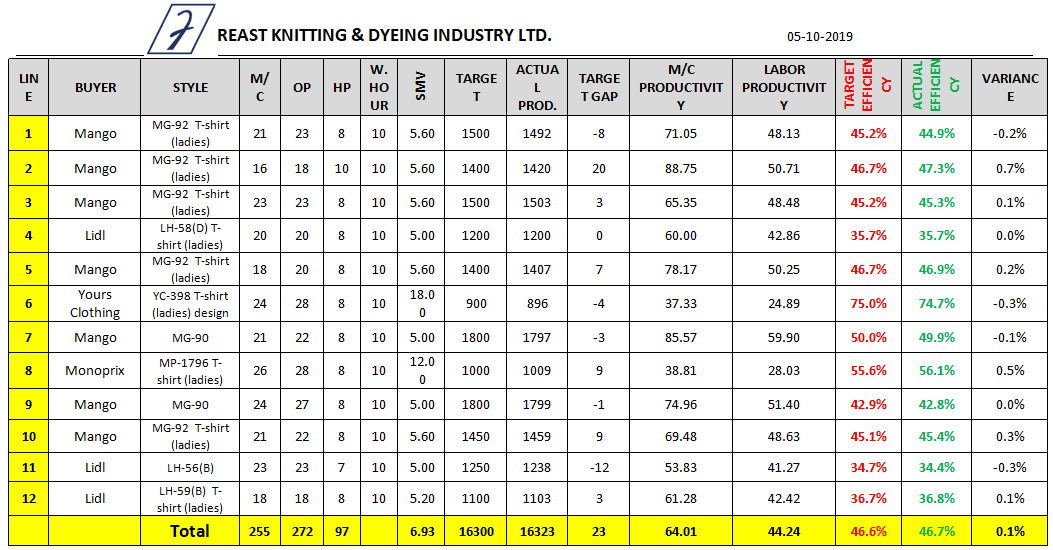
3.2.7.1 Sewing Line Efficiency Report (Day 4)
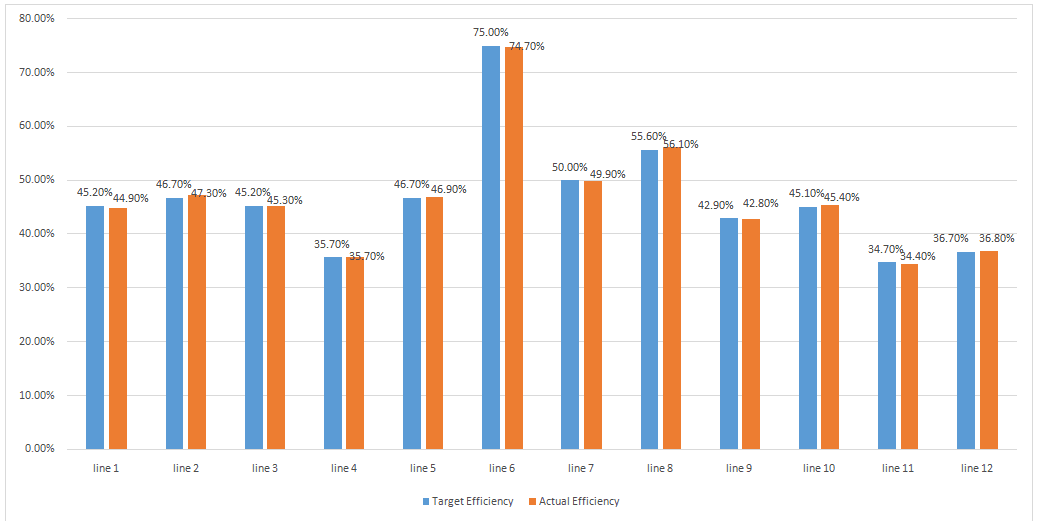
Here we showed the variance of target efficiency and the actual efficiency of different sewing line from day 4. Here different line had different efficiency. We can see here the line no. 11 was the lowest efficiency
3.2.8 Sewing Line Efficiency Data Sheet (Day 5)
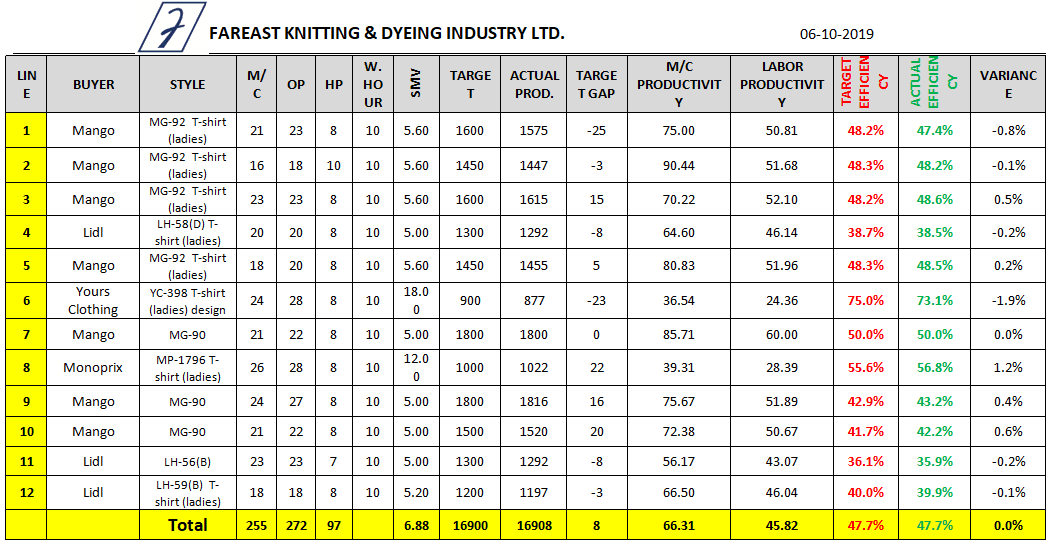
3.2.8.1 Sewing Line Efficiency Report (Day 5)
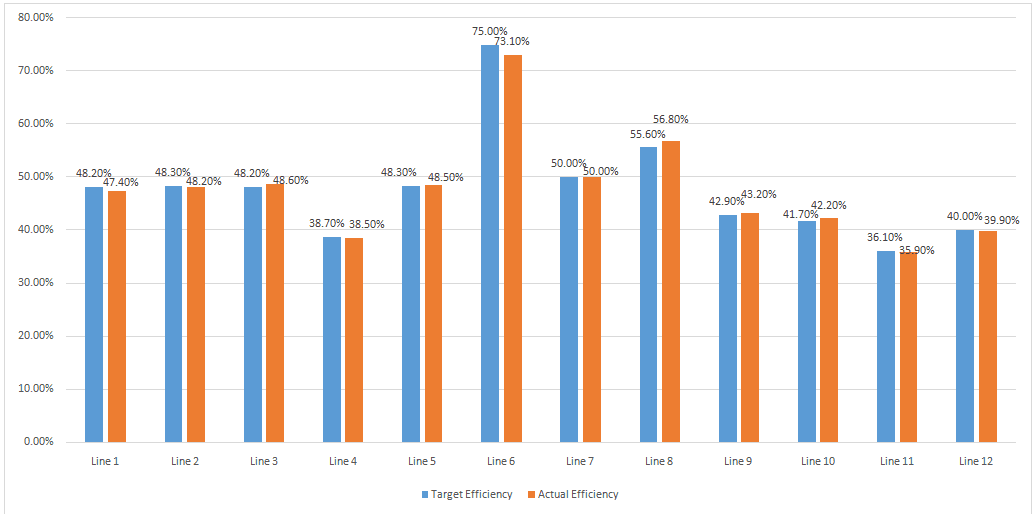
3.2.9 Sewing Line Efficiency Data Sheet (Day 6)
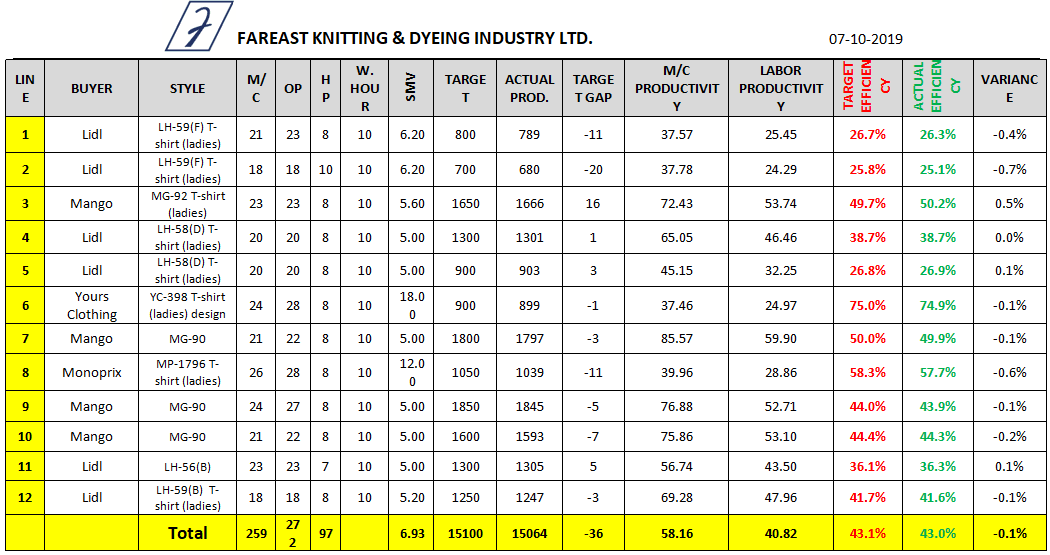
3.2.9.1 Sewing Line Efficiency Report (Day 6)
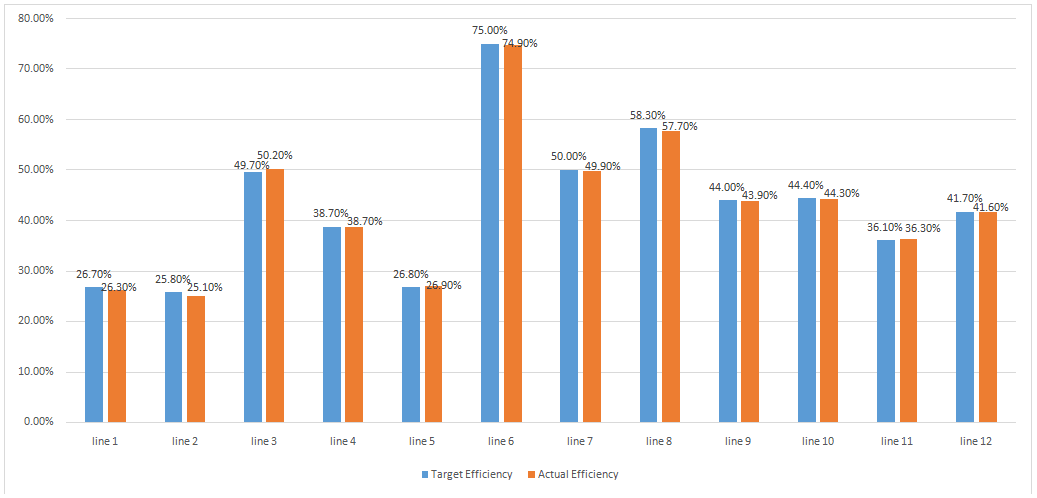
3.2.10 Sewing Line Efficiency Data Sheet (Day 7)
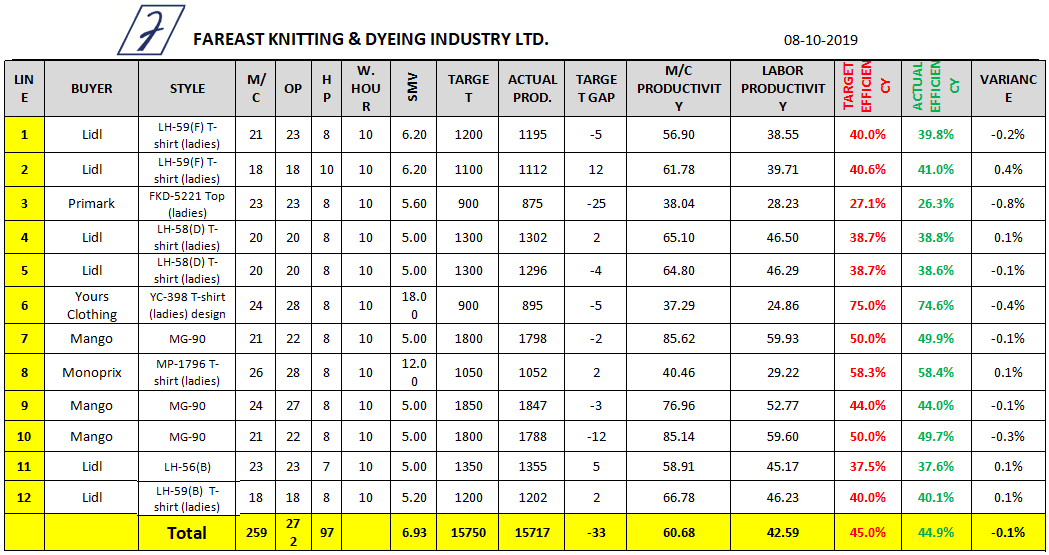
3.2.10.1 Sewing Line Efficiency Report (Day 7)
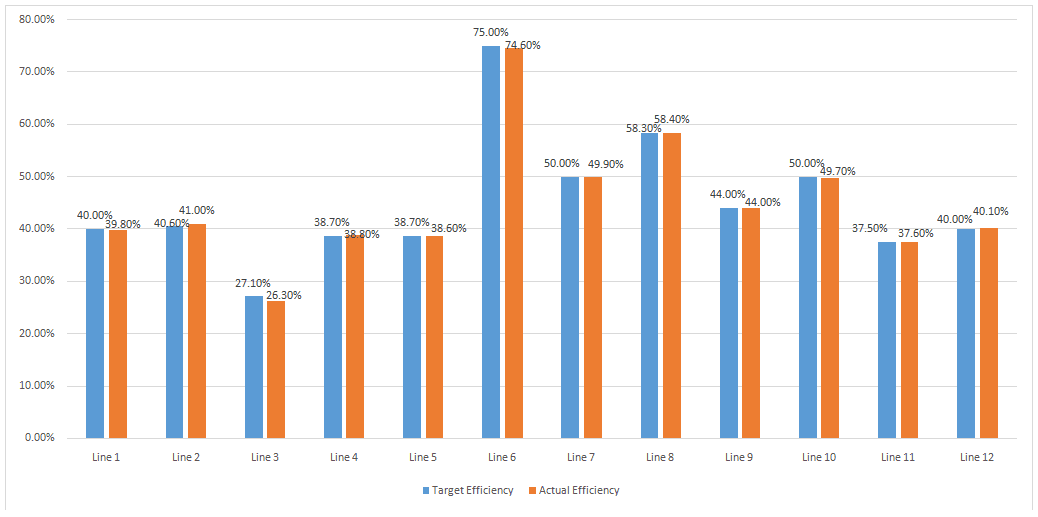
3.2.11 Sewing Line Efficiency Data Sheet (Day 8)
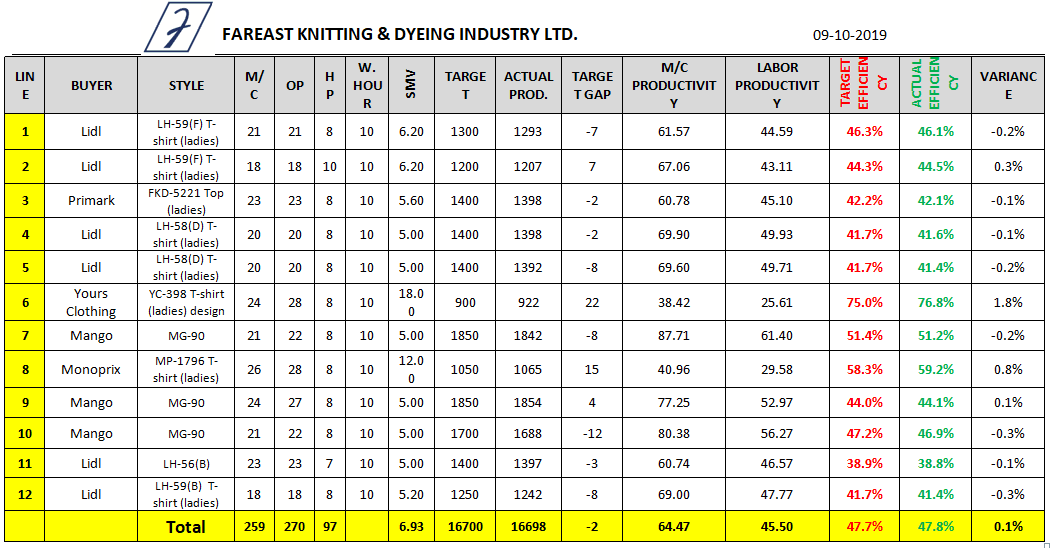
3.2.11.1 Sewing Line Efficiency Report (Day 8)
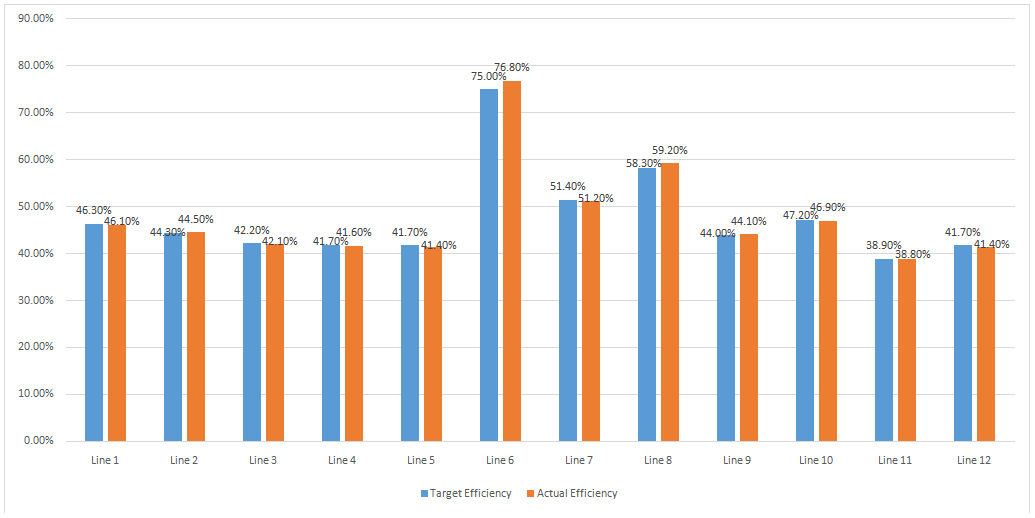
3.2.12 Sewing Line Efficiency Data Sheet (Day 9)
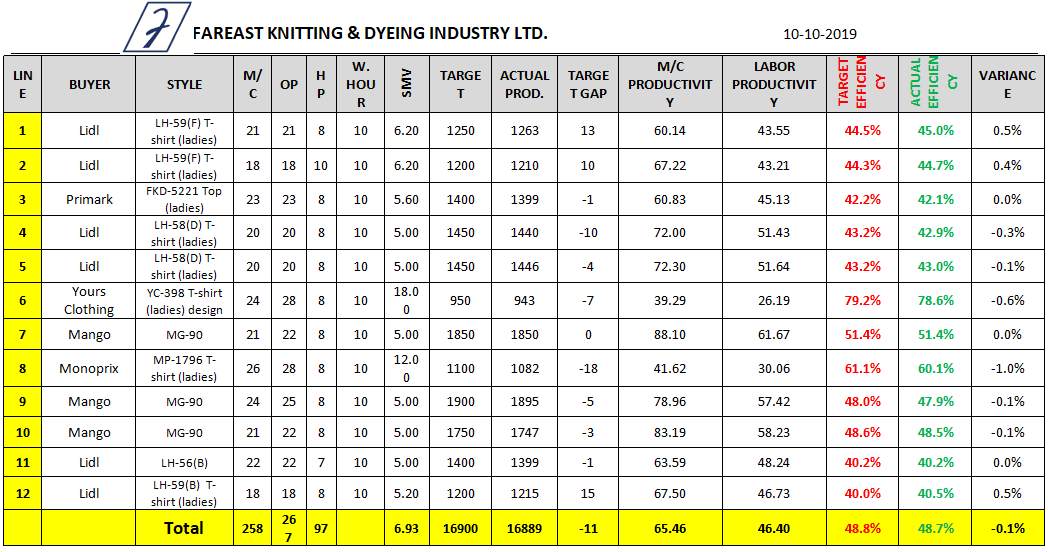
3.2.12.1 Sewing Line Efficiency Report (Day 9)
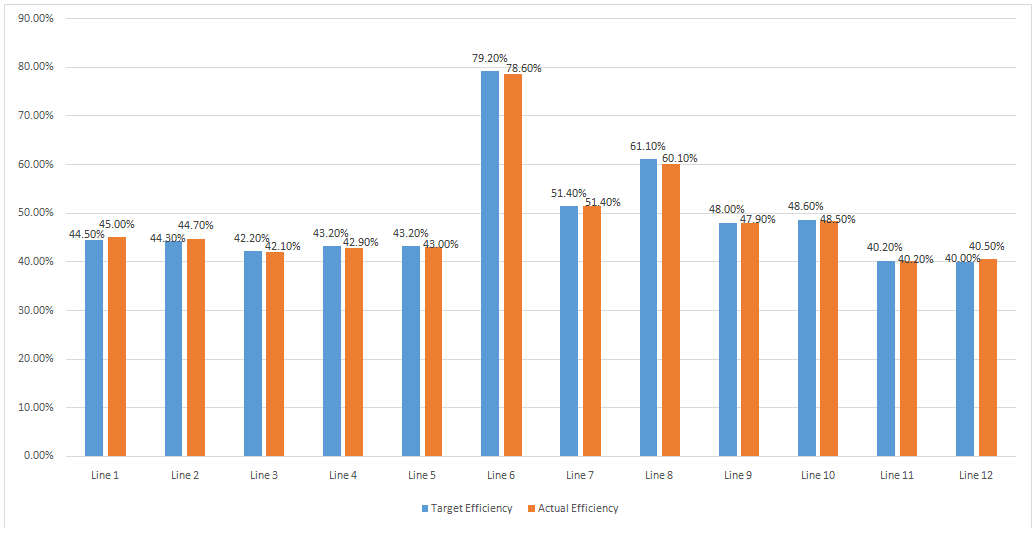
3.2.13 Sewing Line Efficiency Data Sheet (Day 10)
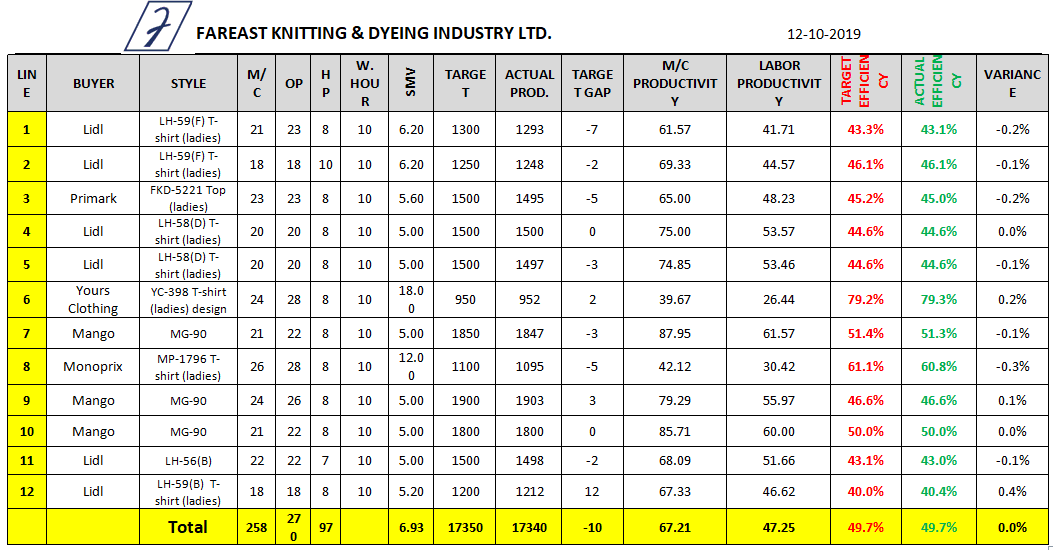
3.2.13.1 Sewing Line Efficiency Report (Day 10)
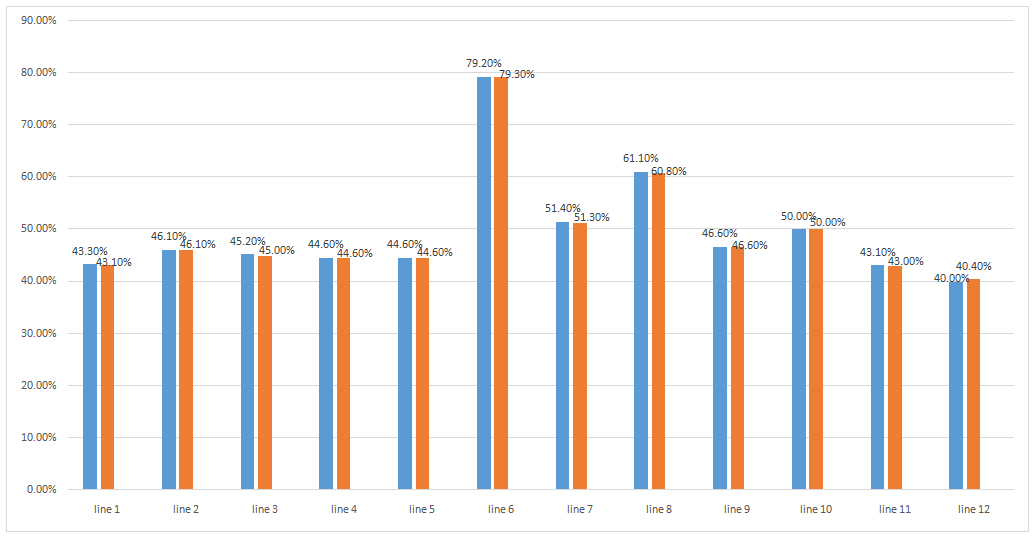
4. RESULT & DISCUSSION
4.1 Result
4.1.1 Summary of 10 Days Sewing Line Efficiency Data Sheet
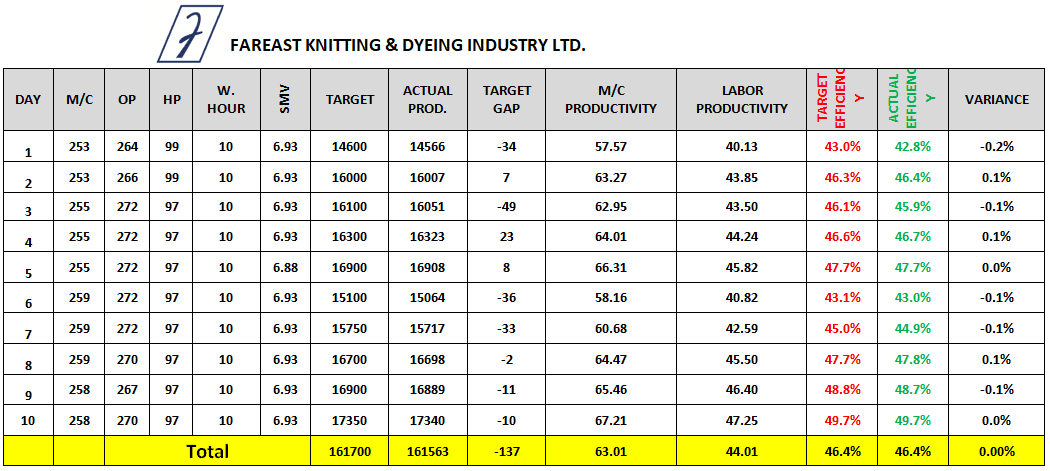
4.1.1.1 Summary of 10 Days Sewing Line Efficiency Report
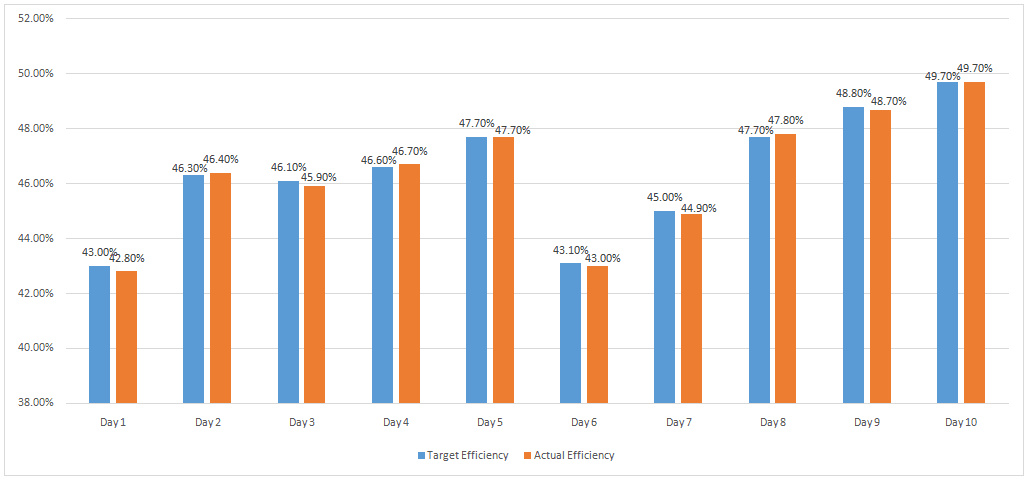
Here we can see that the efficiency of the garments sewing line was increasing day by day. First day the target efficiency was 43.00% and the actual efficiency was 42.80%. So, the variance of the target & actual efficiency was 0.2%. While at last or day 10 the target efficiency was 49.70% and the actual efficiency was also 49.70%. So, here the variance of the target & actual efficiency was 0.0%. And the increasing of the efficiency from first day to last day was about 6.70%.
In the graph we can see here the target efficiency and the actual efficiency of the sewing line day by day. Here also we can see and measure the variance of the target efficiency and the actual efficiency of the garments sewing line.
4.1.1.2 Summary of 10 Days Sewing Line M/C Productivity Report
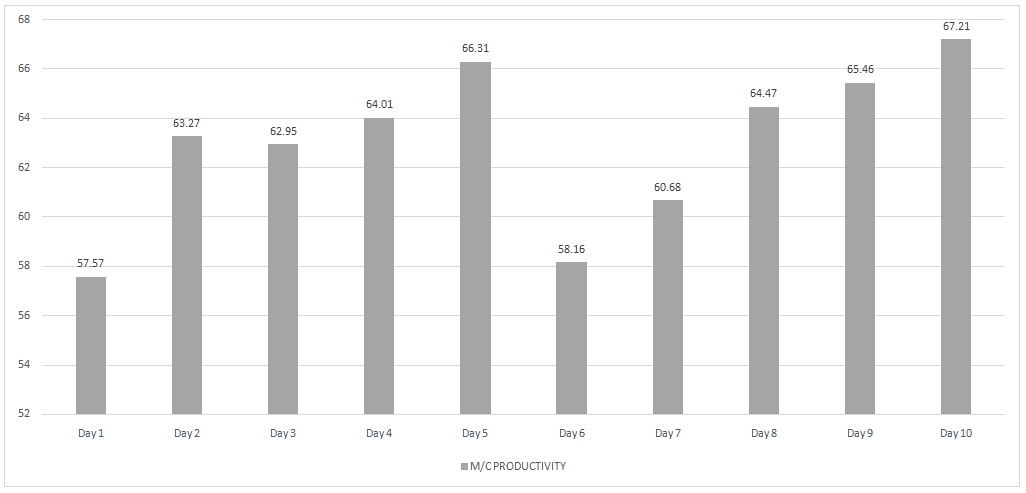
In this graph, we can see here the machine productivity of different days. Here we showed the variance of the machine productivity from day to day. Here day 1 and day 6 was the lowest productivity because of the first day production of different line. But after that day the productivity increased day by day and the last machine productivity was 67.21 pcs.
4.1.1.3 Summary of 10 Days Sewing Line Labour Productivity Report
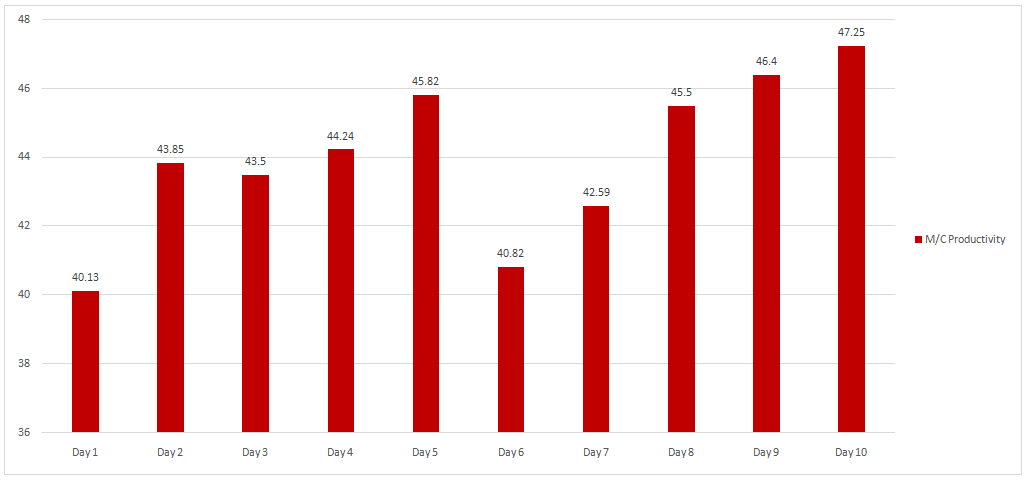
In this graph, we can see here the labor productivity of different days. Here we showed the variance of the labor productivity from day to day. Here day 1 and day 6 was the lowest productivity because of the first day production of different line. But after that day the productivity increased day by day. Here the first day productivity was 40.13 and after that it increased 47.25 at the last day.
4.2 Discussion
From the result we get the 10 days summery of the target and the actual efficiency. And also get the machine productivity and the labor productivity. The target efficiency of the 10 days summery is 46.4% and the actual efficiency is also 46.4%, here the variance of the actual efficiency and the target efficiency is 0%. The machine productivity of 10 days summery is 63.01 and the labor productivity is 44.01. We can see from the result or the graph of figure the efficiency is increased day by day also productivity is increased day by day but the day 6 is the lowest because in that day the new style was started to produce in some of the sewing line. But the overall efficiency and the productivity is increased.
There have many and different reason to increase the efficiency and the productivity that are showed below.
4.2.1 Efficiency Increasing Way
To increasing the efficiency of the garments of sewing line we should follow many things of this line. In garments manufacturing sector, sewing operator assumes a significant job. Sewing administrator productivity has an incredible effect in accomplishing higher pieces of clothing generation, at last which regards the delivery date. As its significance, today we will introduce here some significant key focuses which builds the sewing line& operator efficiency.
4.2.1.1 Increasing Line Efficiency
- Proper target setup;
- Proper manpower use;
- Proper lead time;
- Reduce nonproductive time (M/C breakdown, Power off, Absenteeism of worker);
- Reduce alter%;
- Reduce TPT (Through Put Time);
- Available input;
- Use proper skill matrix report;
- Auto machine use;
- Proper machine speed;
- Proper pressure feed;
- Regular machine servicing;
- Reduce helper;
- Maintain SOP (Standard Operating Procedure);
- Proper environment.
4.2.1.2 Increasing Operator Efficiency
The following are the most important key points for increasing sewing operator efficiency.
- Training sewing operator,
- Motivation,
- Selection of expert operator for critical process,
- Development of working methods,
- Set-up perfect machine layout,
- Continuous feeding to the operators,
- Remove unnecessary interruption during working,
- Set-up target for the operator,
- Avoid excessive overtime to the operator.
4.2.2 Productivity Increasing Way
Higher productivity gets higher edge a business. What’s more, increase in productivity level decreases article of clothing fabricating cost. Consequently a processing plant can make more benefit through productivity improvement. Here some important key points to increase the productivity –
- Hourly operator capacity checks;
- Use best possible line layout;
- Reduce line setting time;
- Improve line balancing;
- Continuous feeding to the sewing line;
- Training for Line Supervisors;
- Training to sewing operators;
- Setting individual operator target;
- Operator motivation.
5. CONCLUSION
Based on the practical experiment conducted, it can be seen that SMV and such like others tools can be effectively applied to apparel industries for better production efficiency. Using this tool, it is possible to map the current status and subsequently analyze to achieve better target. In any case, the work gives a few different ways of progress to expand the line productivity by applying time study and line balancing systems. As a consequence, good line balancing with small stocks in the sewing line has to be drawn up increase the efficiency and quality of production. Line balancing is very crucial in manufacturing sector especially in apparel manufacturing industries. The line needs to balance so that the line has the high value of efficiency. Higher estimation of line effectiveness shows that the line have the roughly equivalent process duration between operators along the line. Other than that, the outstanding task at hand between operators likewise dispersed similarly which make the higher line effectiveness and the objective yield can be accomplished without having extra time.
6. References:
- Garments Technology by Prof. M. A. Kashem
- Garment Manufacturing Technology by Md. Shafiul Azam, Md. Abu Saleh & Khondokar Abu Nafiz
- https://en.wikipedia.org/wiki/Efficiency [1]
- https://www.onlineclothingstudy.com/2018/11/how-to-calculate-overall-line-efficiency.html [2]
- https://www.onlineclothingstudy.com/2011/10/what-is-on-standard-efficiency-and.html [3]
- http://www.garmentsmerchandising.com/how-to-increase-sewing-operator-efficiency/ [4]
- http://textilemerchandising.com/how-calculate-smv/ [5]