Cationization of Cotton by Using Chitosan for Reactive Dyeing to Avoid Electrolyte
Md. Obydullah & Md. Shibli Sadique
Department of Textile Engineering
Dhaka University of Engineering & Technology, Gazipur
ABSTRACT
This study presents finding on the possibility of dyeing of cotton fabric with reactive dyes using chitosan instead of salt. Reactive dyeing is now the most important method for the coloration of cellulosic fibres. Reactive dyes have good fastness properties owing to the covalent bonding that occurs with the terminal (primary and secondary) hydroxyl group of cellulose at alkaline condition during dyeing. All the reactive dyeing systems require huge amount of electrolyte to exhaust the dye. These electrolytes are neither exhaust nor destroyed and hence remain in the dye bath after dyeing. All the above, only 60-65% dye utilization is attainable even with the use of salt in the normal dyeing systems. On the other hand, reactive dyeing pollutes the environment by discharging highly colored reactive dye bath and higher electrolyte concentration. To retain the desired exhaustion of dyes with elimination of salt a convenient method is introduced for cotton treated with chitosan showed a better reactivity and dyeability. In this experiment, dyeing with chitosan instead of salt shown a better possibility owing to the dye absorption test. The dyeing of chitosan treated sample-1, 2, 3 & 4 with NOVACRON RED FN-2BL (1%) dyes shows the absorption rating of 1.6, 1.7, 2.1 & 2.95 respectively at a given wavelength whereas salt treated sample (standard) show the absorption rate 1.9. Dyeing shade varies for different molecular weight of chitosan but low molecular weight chitosan give even shade.
CHAPTER 1
INTRODUCTION
1.1 Introduction
Reactive dyeing is now the most important method for the coloration of cellulosic fibres. Reactive dyes have good fastness [1] properties owing to the covalent bonding that occurs during dyeing. Cotton is made of cellulose molecules which react with the dye. During reactive dyeing the hydrogen atom in the cellulose molecule combines with the chlorine (cl2) atom in the dyeing process and results in a bond. Reactive dyes used to dye cellulosic fibres. The dyes contain a reactive group, either a haloheterocycle or an activated double bond, that, when applied to a fibre in an alkaline dye bath, forms a chemical covalent bond with a hydroxyl group on the cellulosic fibre. There are some benefits, because the reactive dye consists with Chromospheres of dye part, Bridging Groups, Reactive group bearing parts and Reactive groups. Reactive groups are the responsible for the fixation on alkali condition. All the reactive dyeing systems require huge amount of electrolyte and alkali to exhaust and fix the dye respectively. These electrolytes are neither exhaust nor destroyed and hence remain in the dye bath after dyeing. All the above, only 60-65% dye utilization is attainable even with the use of salt in the normal dyeing systems. Reactive dyeing pollutes the environment by discharging highly colored reactive dye bath and higher electrolyte concentration. Higher electrolyte concentration in the effluent cause worst effects such as- impairing the delicate biochemistry of aquatic organism, destructive attack on concrete pipes if sodium sulphate is used as electrolyte due to the formation of alumino-sulphato complexes which swell and crack concretes with considerable alumina content. To retain the exhaustion of dyes without use of salt, a convenient method is introduced for cotton treated with chitosan showed a better reactivity and dyeability. Chitosan is a non-toxic and chemically reactive, and biocompatible natural functional polymer, and has long been used as a biopolymer and natural material in many fields. Recently, chitosan effects widely studied are antistatic, bacteriostatic, biocompatibility properties conferred on various textiles. According to some previous experiences, wrinkle-resistance finishing with chitosan for fabric can improve its wrinkle degree but its handle and mechanical property got worse to a certain extent. Chitosan adsorption also increased the moisture absorption of the fibers. Chitosan with lower molecular weight increased the hydrophilicity of the treated fibers, but chitosan with higher molecular weight, decreased it.
1.2 Objectives of the Project and Thesis
The main objectives of the study to increase the dyeability reactivity dye by using eco-friendly biodegradable chitosan.
- To get desired exhaustion of dye in dyeing of cotton fabric with reactive dyes without using salt.
- To avoid the salt which impart in the environmental pollution.
- To improve color intensity of cotton fabric by using chitosan which provide more dye sites than that of untreated fabric.
- To improve the dye uptake and also to reduce the effluent load.
CHAPTER 2
REACTIVE DYE
2.1 Reactive Dye
A dye, which is capable of reacting chemically with a substrate to form a covalent dye substrate linkage, is known as reactive dye. Here the dye contains a reactive group and this reactive group makes covalent bond with the fibre polymer and act as an integral part of fibre. This covalent bond is formed between the dye molecules and the terminal –OH (hydroxyl) group of cellulosic fibers on between the dye molecules and the terminal –NH2 (amino) group of polyamide or wool fibres. Reactive dyes in the simplest terms, all reactive dyes are made up of three basic units, a chromophore, a bridge and a reactive group/ groups (either a haloheterocycle or an activated double bond). One problem is that instead of reacting with the -OH groups on the cellulose, the fibre-reactive group may react with the HO- ions in the alkali solution and become hydrolysed. The hydrolysed dye cannot react further. This must be washed out of the fabric before use.
2.2 Properties of Reactive Dye
- Reactive dyes are anionic dyes, which are used for dyeing cellulose, protein and polyamide fibres.
- Reactive dyes are found in power, liquid and print paste form.
- During dyeing the reactive group of this dye forms covalent bond with fibre polymer and becomes an integral part of the fibre.
- Reactive dyes are soluble in water.
- They have very good light fastness with rating about 6. The dyes have very stable electron arrangement and can protect the degrading effect of ultra-violet ray.
- Textile materials dyed with reactive dyes have very good wash fastness with rating Reactive dye gives brighter shades and have moderate rubbing fastness.
- Dyeing method of reactive dyes is easy. It requires less time and low temperature for dyeing.
- Reactive dyes are comparatively cheap.
- Reactive dyes have good perspiration fastness with rating 4-5.
- Reactive dyes have good perspiration fastness.
2.3 The Components of Reactive Dye
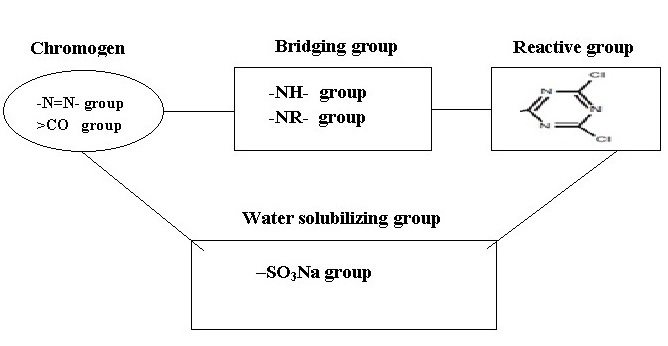
a) The chromogen:
Dye part or chromogen (color producing part), which contains chromophores. Chromophore – a color-bearing compound, typically meaning the part of a larger organic molecule that makes it appear colored. Some chemicals groups which are responsible for the impart color to the substrate. Dyes typically have a chromophore chemically bonded to other structures that impart desired characteristics such as affinity for the fibre and solubility in water. A particular chromophore structure may be found in a variety of dye classes and in pigments. In practice, monoazo, disazo, metallized monoazo, metallized disazo, formazan, anthraquinone, triphenodioxazine, and phthalocyanine chromophores have been used for the preparation of reactive dyes.
b) The water solubilising group (ionic groups, often sulphonate salts):
The groups which have the expected effect of improving the solubility since reactive dyes must be in solution for application to fibres. This means that reactive dyes are not unlike acid dyes in nature. Solubilizing groups provide characteristics such as water solubility, substantivity, migration and wash off. The dominant solubilizing group in reactive dyes is the sulphonic substituent.
c) The bridging group:
It links the chromogen and the fibre-reactive groups. Frequently the bridging group is an amino, -NH- group or –NR- group. This is usually for convenience rather than for any specific purpose and they also influence the reactivity, degree of fixation, stability of the reactive dyeing and other dyeing characteristics, such as substantivity and migration, significantly. The typical bridging group is an imino (-NH-) group.
d) The fibre-reactive group:
This is the only part of the molecule able to react with the fibre. Reactive group do not contribute color which is determined by chromogen group. The reactivity of vinyl sulphone group is less than halogen group. If no of reactive group incresase, binding also increase depending on the dye structure. If the molecular weight of reactive group increases, reactivity also increases.
2.4 Classification of Reactive Dyes
Reactive dyes may be classified in various ways as below:
a) On the basis of reactive group:
i) Halogen (commonly chlorine) derivatives of nitrogen containing heterocycle, like 3 types-
- Triazine group. e.g. Triazine derivatives: procion, cibacron.
- Pyridimine group e.g. Pyridimine derivatives: reactone
- Quinoxaline dyes. e.g. Quinoxaline derivatives: levafix E.
ii) Activated vinyl compound:
Vinyl sulphone e.g. Vinyl sulphone: remazol
Vinyl sulphone dyestuffs possess poor affinity for cellulosic fibers in absence of salt and alkalis. For this reasons, they are suitable for use on pad. Their substantivity can be increased by addition of glauber salt or common salt and alkali, making the dyestuff suitable on all conventional dyeing machines for loose material, yarn in hanks and packages and piece goods. The dyeing methods may therefore, be classified under the padding and exhaust processes, standing baths are not recommended, as in alkaline medium inactivation of the dyestuffs by reaction with water takes place as a side reaction.
These dyes require higher dosage of alkali and salt for exhaustion and fixation. But these dyes have on continuous contact with the alkali and water medium for longer duration time dyeing process, about 30 to 40% will get hydrolyzed and become in active as dyestuff. But in order to make active and fix on the fiber we need to give higher dose of alkali and salt along with temperature of up to 60°C.
- Vinyl acrylamide e.g. Vinyl acrylamide: primazine
- Vinyl sulphonamide e.g. Vinyl sulphonamide: levafix
b) On the basis of reactivity:
i) Lower reactive dye: Medium reactive dye: here pH is maintained 11-12 by using Na2CO3 in dye bath.
ii) Higher reactive dye: here pH is maintained 10-11 by using NaHCO3 in dye bath.
c) On the basis of dyeing temperature:
i) Cold brand:
These types of dyes contain reactive group of high reactivity. So dyeing can be done in lower temperature i.e. 320-60ºC. e.g. PROCION M, LIVAFIX E.
ii) Medium brand:
This type of dyes contains reactive groups of moderate reactivity. So dyeing is done in higher temperature than that of cold brand dyes i.e. in between 60-71ºC temperatures e.g. Remazol, Livafix are medium brand dyes.
iii) Hot brand:
This type of dye contains reactive groups of least reactivity. So high temperature is required for dyeing i.e. 720-930 C temperature is required for dyeing. e.g. PRICION H, CIBACRON are hot brand dyes.
d) On the basis of functional group present:
i) Mono functional reactive dyes.
ii) Bi functional reactive dyes.
The dyes were first introduced by Hoechst, based on ß-sulphato ethyl sulphone as a reactive group. The range made the successful breakthrough due to comprehensive shade range, versatile application, ability to be dyed at 60°C and good compatibility with other bifunctional dyes. Being a compact structure, it offers ease in wash off for removal of unfixed dyes at the end of dyeing during washing. The dye fibre bond offers good acid stability. With the limitations to above, there may be problems with reproducibility associated with it, which is not accepted especially for pale shades. There is the possibility of unlevel dyeing with a small variation in the process due to its lower molecular weight. Hetero bifunctional dyes made a get through in early 80’s. The dyes were based on a quite simple but beautiful chemistry. They had filled a big vacuum of various hues of bright shades, which were not possible with vinyl sulphone type. The dyes were conventional dichlorotriazine type, with the end condensation of ß-sulphato ethyl sulphone to have different type of reactive group in a single molecule. Being a dual reactive, the primary mode of fixation is from vinyl sulphone group and the dyeing temperature is same as vinyl-sulphone, which enables good intercompatibility in between the two classes.
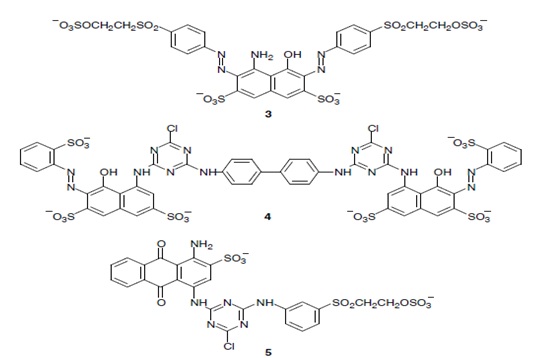
(4) MCT-VS type. (5) Sumifix Supra dyes (Sumito)
iii) Poly functional or multifunctional reactive dyes.
2.5 Reactive Dyes for Cellulosic Fibers
Cellulosic fibers are significantly dominated by cotton. Other cellulose based fibers include viscose rayon, linen, cupraammonium rayon, jute and lyocell, and these can be dyed with dyes used on cotton. The structure of cellulosic fibers is characterized by the poly-(1, 4)-β-D-glucopyranose molecule (fig 3.2), and consequently may be considered as a polyhydric alcohol. Each glucopyranose ring on the cellulose chain contains three hydroxyl groups, a primary hydroxyl group in the 6 position and secondary hydroxyl groups in the 2 and 3 positions.
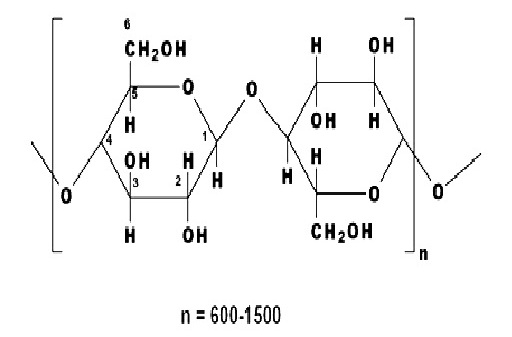
A polyhydric alcohol such as cellulose is more acidic than a simple alcohol and, in fact is comparable with water as shown by the dissociation constants (K) listed below.
- Water K= 2.09×10-14
- Methanol K= 8.1×10-15
- Manitol K= 7.5×10-14
- Cellulose K= 1.84×10-14
The dissociation constant for cellulose refers to the ionization of the hydroxyl group in the 6 position of the glucopyranose ring. The hydroxyl groups in positions 2 and 3 of the ring are less acidic. Therefore, cellulose is ionized under alkaline conditions and can behave as a nucleophile towards compounds containing electron-deficient carbon atoms (e.g. reactive dyes).
A variety of attempts have been made to bring about the formation of a covalent bond between a dye and a fiber. In this respect, there are two general approaches: producing a dye within the fiber, and producing a dye that is reactive towards the fiber. A covalent dye cellulose combination was achieved in 1895 by Cross and Bevan. These workers showed that cellulose (Cell-OH) treated with strong alkali was changed into “soda cellulose” which could be treated with benzoyl chloride to form benzoyl cellulose. The resultant benzoyl cellulose was nitrated, the nitro group was reduced, and the amino group was diazotized. The diazo group was coupled with N, N-dimethylaniline to give “dyed” fibers.
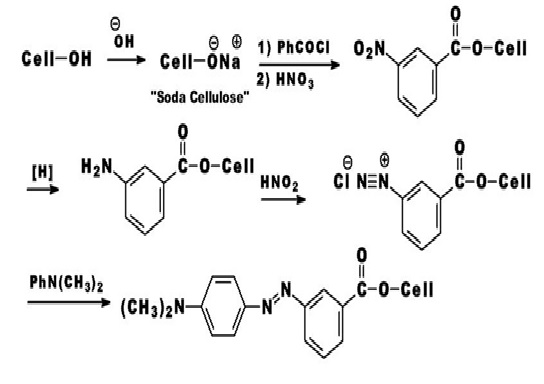
The first commercial reactive dyes for cellulose were developed by Rattee and Stephen and marketed by ICI in 1956 under the trade name Procion M. These dyes were introduced for the production of fast bright shades on cellulosic fibers using continuous dyeing methods. Procion Brilliant Red M-2B in (Fig. 3.4) is one of the early members of this family. Procion M dyes contained the highly reactive dichlorotriazine group, and reacted with cellulose under alkaline conditions at room temperature.
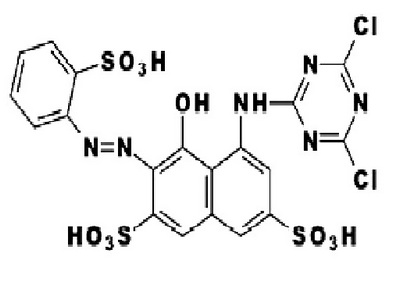
The major factor contributing to the long delay in producing the first reactive dye for cellulose was the belief that cellulose was a relatively inert substrate and that conditions required to effect a chemical reaction would cause serious fiber degradation. Therefore, in early studies dyestuff chemists were led astray in thinking that they needed to convert cellulose to the more reactive soda cellulose to make fiber reactivity possible. No one expected that any reactive group would prefer to react with a hydroxyl group of cellulose when cotton was placed in an aqueous dyebath containing numerous competitive hydroxyl groups from water. However, a large number of reactive dyes with varieties of reactive groups have been developed.
2.6 Chemical Reactions between Reactive Dyes and Fibers
a) Nucleophilic Substitution:
Nucleophilic substitution characterizes dye-fiber fixation that occurs when a leaving group in the reactive system is displaced as a result of an interaction with a nucleophilic group on the polymer chain. Nucleophilic substitution is facilitated by the electron withdrawing properties of the aromatic nitrogens, and the chlorine, and the anionic intermediate is resonance stabilised as well. This resonance means that the negative charge is delocalised onto the electronegative nitrogens.
For example:
But this requires harsh conditions. To improve the rate under mild conditions, powerful electron-withdrawing groups such as -NO2 may be added.
However, this will only work if there is a good leaving group, such as -Cl or -N2.
The major fibre-reactive group which reacts this way contains six-membered, heterocyclic, aromatic rings, with halogen substituents.
For example, the Procion dye-
Where X = Cl, NHR, OR.
The reaction of a monochlorotriazine reactive dye with a hydroxy group of cellulose is typical of this process.
a)
b)
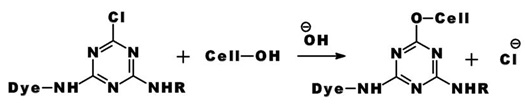
The same process accounts for the competitive hydrolysis reaction between the dyes and water during dye application.
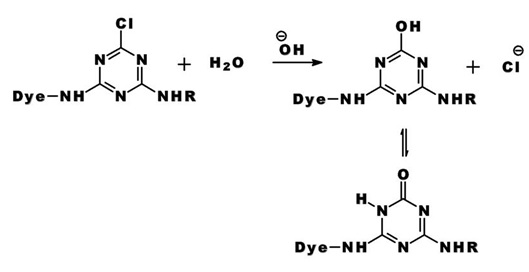
b) Nucleophilic Addition:
Nucleophilic addition characterizes the dye-fiber reaction in which a nucleophilic group in the fiber adds across an activated carbon-carbon double bond in the reactive group. Most of reactive systems used contain a vinylsulphone moiety. The vinylsulphone reactive group itself is usually not present in commercial form of the dyes employed. Instead, more stable precursor such as the β-sulphatoethylsulphone group is used. The two-stagenprocess associated with fiber fixation is structurally related dyes containing a β-sulphatoethylsulphamoyl group probably form a cyclic compound capable of reacting with cellulose to give cellulose ether.
Systems based on activated double bonds also undergo a competitive hydrolysis reaction.
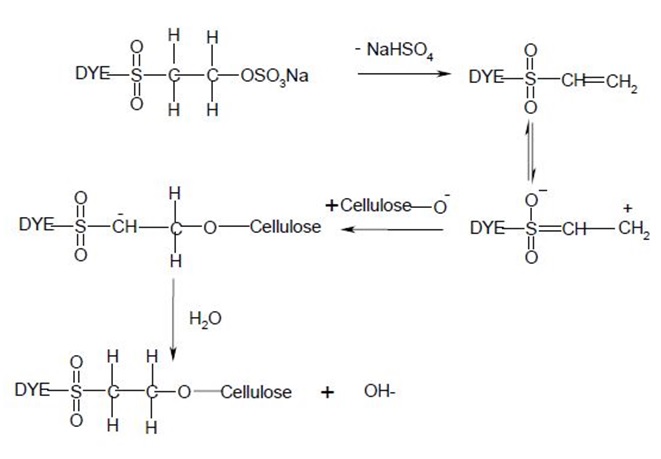

CHAPTER 3
COTTON FIBER
3.1 Cotton Fibre
Cotton is unique in nature which has the highest percentage of cellulose. It varies from 90% to 95%. This concentration depends upon many factors, such that maturity level and variety of cotton, place on cottonseed from where it is drawn. In cotton fiber there is certain non-cellulosic matter, which plays important role in growth and on forth coming processes. These are located either on the surface of the fiber or in center of fiber means inside the lumen. Being a natural fiber, there are many factors which affect the structure of cotton cellulose. There are primary and secondary walls in the cotton cellulose. Primary wall or outer wall is less crystalline and has less percentage of cellulose. Whereas, secondary wall is around the lumen and consist of pure cellulose cotton fiber is composed of the crystalline and amorphous structure.
3.2 Chemical Structure of Cotton Fiber
The molecular structure of cellulose has always been of great interest to scientists and over time several structures have been proposed. The linear polymer, β-D-glucopyronose with 1,4-glycosidic bonds, is the widely accepted structure for cellulose. Consequently it may be considered as a polyhydric alcohol. Each glucopyranose ring in the cellulose chain contains three hydroxyl groups, a primary hydroxyl group in the 6- position and secondary hydroxyl groups in the 2- and 3- positions.
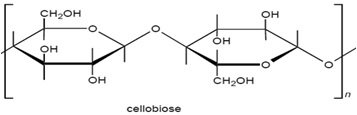
3.3 Cotton Fiber Ingredients
The basic ingredients, that are responsible for complicated interconnections in the primary wall, are cellulose, hemicelluloses, pectins, proteins and ions. These components are present throughout the primary wall. The only difference is the concentration and nature of each component, as when approaching the secondary wall. In the secondary wall, only crystalline cellulose is present, which is highly ordered and has compact structure the cellulose fibrils in the secondary wall are laying parallel to one another.
Table: 3.1 Typical Composition of Dry Mature Cotton Fiber
Constituents | Composition (%) | |
Whole fiber | Outer layer | |
Cellulose | 94 | 54 |
Waxes | 0.6-1.3 | 14 |
Pectin substances | 0.9-1.2 | 9 |
Protein (nitrogen substances) | 0.6-1.3 | 8 |
Ash | 1.2 | 3 |
Organic Acid | 0.8 | – |
Others | 1.4 | 12 |
- Cellulose: 94%. It is main part of the cotton fiber and secondary wall posse’s highest percentage of the total cellulose
- Waxes: 0.6-1.3%. It is higher monovalent alcohol-tractional, palmitic, oleic acid, glycerin. Its melting point is 77.0. It is found on surface and in primary wall.
- Pectin’s: 0.9 -1.2%. These are ploygalacturonic acid, and its magnesium salts, methyl ester, xylose. These are mainly present in primary wall.
- Proteins: 0.6-1.3%. These are protoplasm rest in lumen and aspartic, glutamic acid and proline, 0.2-0.3% of nitrogen are found in primary wall
- Ash: 1.2%
- Organic acids: 0.5-1.00%. Salts of citric and L-maleic acid
- Others: (i) Mineral salts: 0.7-1.6%. Hypochlorites of sulphates, phosphates, oxides of silicon, calcium, potassium, magnesium. (ii) Sugar: 0.3%. Glucose, galactose, fructose, pentose. (iii) Toxine: 0.9%. Endotoxine, evolved from bacterial cells.
3.4 Fiber Macro Structure
Under a microscope, a cotton fiber appears as a very fine, regular fiber. It ranges in length from about 10mm to 65 mm, depending upon the quality of the fiber. Each cotton fiber is composed of concentric layers. The cuticle layer on the fiber itself is separable from the fiber and consists of wax and pectin materials. The primary wall, the most peripheral layer of the fiber, is composed of cellulosic crystalline fibrils. The secondary wall of the fiber consists of three distinct layers. All three layers of the secondary wall include closely packed parallel fibrils with spiral winding of 25-35o and represent the majority of cellulose within the fiber. The innermost part of cotton fiber- the lumen- is composed of the remains of the cell contents. Before boll opening, the lumen is filled with liquid containing the cell nucleus and protoplasm. The twists and convolutions of the dried fiber are due to the removal of this liquid. The cross section of the fiber is bean-shaped, swelling almost round when moisture absorption takes place.
The overall contents are broken down into the following components.
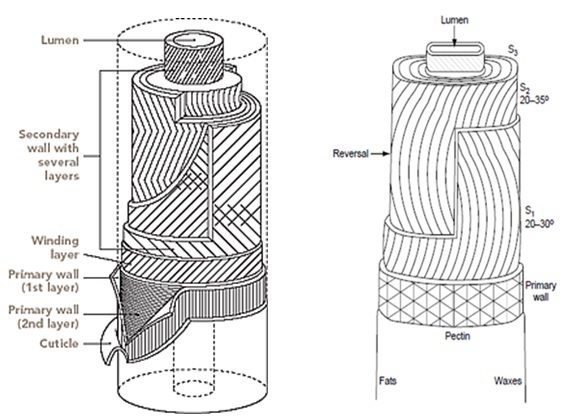
3.5 Polymer System of Cotton
The density method used to determine cellulose Crystallinity is based on the density gradient column, where two solvents of different densities are partially mixed. Degree of Crystallinity is, then, determined from the density of the sample, while densities of crystalline and amorphous cellulose forms are known (1.505 and 1.556 respectively). Orientation of untreated cotton fiber is poor because the crystallites are contained in the micro fibrils of the secondary wall, oriented in the steep spiral (25-30o) to the fiber axis.
3.6 Chemistry of Cotton Cellulose
Cellulose is an insoluble substance and mainly composed of polysaccharide, which holds chains of glucose monomers. It is only soluble in some specific solvents. It is the main constituent of plant cell walls and as well as of vegetable fibers. Cotton is one of the vegetable fibers which have the highest percentage of cellulose. There is a diverse structures and compositions of cellulose of cotton. Its structure makes it divergent from other naturally occurring matters. Cotton cellulose is unique in many ways and possesses distinct characteristics which make it highly useful for many purposes. It has been assumed that cotton cellulose structure is based on glucose unit only. However, it is also believed that there is modest amount of pentose is present, which is removed during scouring process. They further report that it has been notices from the chromatographic analysis that glucose, xylose, arabinose and a trace of rhamnose are also present in raw cotton. There is no evidence of the presence of pentose. Cotton cellulose is highly crystalline in nature and well oriented and has along and rigid molecular structure. The 1,4-D glucopyranose are the principle building blocks of cotton cellulose chain and are linked by l,4-glucodic bonds. Free rotation of the anhydrogluco-pyranose C-O-C link is stopped by steric effects. There are three hydroxyl groups attached to each anhydroglucose. One group is attached at C-6 and two at C-2 and C-3. Due to the presence of hydroxyl groups and the chain conformation, there are many more bonds possible (inter molecule and intramolecular). Such bonds make the fiber more rigid by increasing the rigidity of the structure of cotton cellulose.
3.7 Cross Section of Cotton Fiber
The cell wall is a dynamic structure which composition and form can change markedly, not only during cell growth but also after the cells have become matured. The cotton fiber is structurally built up into concentric zones and a hollow central core known as the lumen.
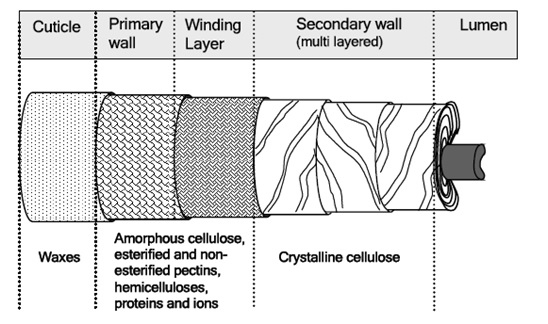
The mature fiber essentially consists of (from outside to inside) – the cuticle i.e. the outermost layer, the primary cell wall, the secondary wall and the lumen. Figure 1.1 systematically shows the different layers present in the cotton fiber with the compositions of each layer. Cotton contains nearly 90% of cellulose and around 10% of non-cellulosic substances, which are mainly located in the cuticle and primary wall of the fiber. Typical components in dry mature cotton fibers most of the non-cellulosic materials are present in the outer layers of cotton fiber.
Figure illustrates schematically the distribution of cellulose and other non-cellulosic materials in the various layers of cotton fiber.. The outermost layer is the cuticle. It is a thin film of mostly fats and waxes. Owing to non-structured orientation of cellulose and non-cellulosic materials, the primary wall surfaces is unorganized and open. This gives the flexibility to the primary wall, which is required during the cell growth.
3.9 Different Layer of Cotton Cellulose Structure
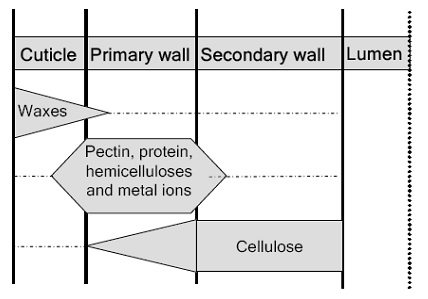
a) Cuticle – the outermost layer:
The aerial surfaces of vascular plants are covered with an extra cellular layer called the cuticle or cuticular membrane that overlays the cell wall of epidermal cells. The term “cotton waxes” has been used for all lipid compounds found in the cuticle of fiber. The main function ascribed to the cuticle is to minimize water losses from cotton fiber. Other functions are, to limit the loss of substances from fibers internal tissues, and to protect the fiber against physical, chemical and biological aggressions. The cuticle contains primary alcohols, higher fatty acids, hydrocarbons, aldehydes, glycerides, sterols, acyl components, resins, cutin and sobering, which are called waxes. The cuticle gives a soft touch to the fiber and reduces the friction forces during spinning. At the same time, presence of these waxy materials is Initiation of fiber growth detrimental in chemical processing of cotton yarn because it gives the fiber surface a high hydrophobicity. The cotton waxes are solid substances with rather high and wide range of melting points (64°C to 214°C) and constitute around 0.4 to 0.8% dry weight of raw cotton After treatment with boiling NaOH, waxes are hydrolyzed into a sodium salt of the fatty acid and alcohol. Apart from the above mentioned components in the cuticle, there are also some complex biopolymers present.
b) The primary wall:
Cotton is longest single cell as compared to other agro-based fibers. Its growth initiates with the single cell from the individual epidermal cells on the outer integument of the ovules in the cotton fruit. There is a number of cotton fibers grow simultaneously from the same cotton bowl (cotton seed). Each fiber presents a single cell of plant. In first step this plant goes to its full length and during this period primary wall is formed. This primary wall holds the whole cell plant and keep it aligns and well oriented. During this period, when the fiber is totally consisting of primary walls, fiber width is 2.98 mm and crystalline percentage is up to 30%.
The primary wall in a cotton fiber is a thin film with a thickness of about 0.5 μm. It serves as the exterior surface of the fiber. In the primary wall, apart from amorphous cellulose, most of the constituents are non-cellulosic materials. This layer is flexible and swells uniformly in all directions. the typical composition of the primary wall with details of each component. The primary wall contains amorphous cellulose, pectin’s, proteins, hemicelluloses and coloring components. It is important to study the individual component and interconnections in the primary wall, for attacking specific components with enzymes to destabilize the primary wall efficiently.
A brief description of the primary wall components, followed by a description of their interconnections is given below.
Details of each constituent in the primary wall
i) Cellulose:
Cellulose in the primary wall is heterogeneous and has a low degree of polymerization (DP up to 2000 glucose units) compared with cellulose in the secondary wall. The amorphous region of cellulose in a cotton fiber is characterized by its ability to swell in water. The orientation of cellulose macromolecules in the primary wall is low, that means that individual macromolecules are not arranged in any definite order. The cellulose micro fibrils in the primary wall are surrounded by a matrix of other non-celluloses. Micro fibrils of cellulose are crystalline aggregates of β(1-4)-linked glucose polymers. They are omnipresent elements of the plant cell wall and are responsible for much of its tensile strength.
ii) Hemicelluloses:
Hemi cellulose is the name of a heterogeneous group of branched matrix forming polysaccharides. Hemicelluloses bind non-covalently to the surface of cellulose micro fibrils in the primary wall. They form a coating over the cellulose micro fibrils and are able to cross-link them into a complex network of the primary wall. There are several classes of hemicelluloses with an average 50 glucose units that are linearly β (1-4)-linked to one another. The difference between various classes of hemicelluloses is expressed in terms of oligosaccharide side chains
iii) Glycoprotein:
Glycoprotein also known as extensions account up to 15% of the primary cell wall mass. Glycoprotein contains a protein backbone with extended rod like carbohydrates that protrude outwards. The carbohydrates in the glycoprotein account for 65% of the total structure. For a cotton fiber, these rod shape extensions are made up of roughly 300 amino acids, and abundantly contain hydroxyl-proline (Hyp). Most of the hydroxyl-prolines are glycosylated with chains of three or four sugar residues e.g. arabinose and galactose. The carboxyl-terminal peptides in the glycoprotein molecule are covalently linked by disulfide bonds and often contain an oligosaccharide chain. These oligosaccharides chains are also interconnected with other polysaccharides in the primary wall.
iv) Pectin’s:
Pectin’s are acidic polysaccharides, which are found in fruits, fibers and vegetables. Pectin being a non-cellulosic material in cotton fibers plays several important roles. It contributes to the firmness and structure of cotton fiber, both as a part of the primary cell wall. Pectin acts as cementing material for the cellulosic network in the primary wall. Pectin, as a hydrating agent, controls the movement of water and other plant fluids through the rapidly growing fiber.
v) Coloring matters:
Coloring matter (pigments) in cotton fibers is rarely studied. In the natural state, cotton is off-white, cream, brownish or greyish green, depending on the source and growing conditions. However these coloring components do not take part in the scouring process.
vi) Metal contents:
The primary wall of a cotton fiber contains different quantities of metal depending on their growing conditions and source. Potassium is the most abundant metal ion in cotton fibers followed by magnesium and calcium. Other metal ions which are present in traces are sodium, iron, manganese, copper and zinc. Removal of calcium is essential during the scouring process for better primary wall destabilization. However, removal of rest of the metals from cotton fibers is also important, because they can contribute to problems during further wet-pretreatment processes like oxidative bleaching.
c) The secondary wall:
Secondary wall formation originates just after the completion of primary wall. Primary wall takes around 20-25 days and after that secondary wall synthesis commences which takes 15-22 days and it continues for 30-40days. During this period fiber gains weigh of 130 ng/mm, as compared to 2ng/mm while primary wall was under development. After completion of primary wall, secondary wall is formed. Secondary wall is in the shape of a ring inside the tube or cylinder. Notwithstanding, during this period a lumen in the center is also produced at the time of fiber maturity. Secondary wall is an example of pure cellulose. Study further reveals that secondary wall is 94% of the total mass of the fiber material. Thereby secondary wall is contemplated as the main responsible for all sorts of mechanical properties. There is a slight variation in the density of the cell wall before and after desiccation. It is 1.55 gm before drying and after dehydration it reduces to 1.52 gm under the 65% RH conditions.
Cellulose in the secondary wall is characterized by a higher degree of polymerization (nearly 5000 units) compared with cellulose in the primary wall. Table 2.4 shows the various units and sub-units of cotton cellulose with their diameter. In the secondary wall of a cotton fiber, two cellulose molecules can form a long planar chain of β (1-4)-linked glucose units, resulting in a ribbon like structure. These two cellulose chains forms a sheet, which is called an elementary fibril. Micro fibrils of cellulose are crystalline aggregates of approximately 21 elementary cells (Table 2.4). Intermolecular hydrogen bonds play an important role to stabilize chains of elementary fibril to become a micro fibril. Finally, a large numbers of such micro fibrils are laying in parallel direction forms the various layers of the secondary cell wall.
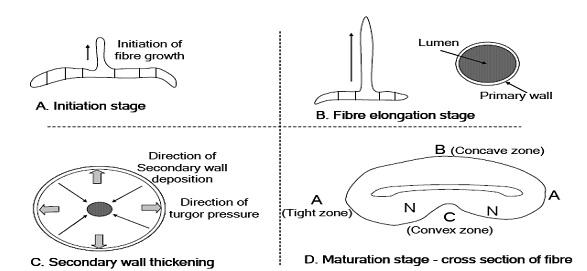
CHAPTER 4
CHITOSAN
4.1 Chitosan
Chitosan is a useful biopolymer obtained by alkaline deacetylation of chitin. Generally, chitin is converted into chitosan with various degrees of deacetylation (DD) and molecular weights (Mw) depending upon the purpose of chitosan utilization. Chitosan differs from chitin in that it is soluble in mild acidic medium. The cationic form of chitosan in acidic solution plays a role in not only governing its solubility but also acting as an active site. The applications of chitosan for improving dyeability of cotton fabric have been widely studied. In the textile area, the higher the active site of chitosan favors the higher the dye adsorption (including natural dye) as well as film formation on fiber surface. Chitosan film on fabric surface is not desirable since it causes the problem of fabric stiffness (poor handling). Fortunately, these effects could be adjusted by the usage of chitosan’s proper molecular weight. Normally, chitosan with various molecular weights could be achieved by depolymerization techniques. In this study, the depolymerization of native chitosan using sodium nitrite under mild acidic condition was proposed in order to prepare chitosans with various low molecular weights. Then they obtained depolymerized chitosans and mangosteen dye extract as a colorant were applied onto cotton fabrics. To investigate the co-application of chitosan and mangosteen dye extract on cotton fabric, the dyeing properties including dyeability, colour fastnesses, i.e. light fastness, wash fastness, and fabric stiffness were evaluated. Recently, chitosan effects widely studied are antistatic, bacteriostatic, biocompatibility properties conferred on various textiles. According to some previous experiences, wrinkle-resistance finishing with chitosan for fabric can improve its wrinkle degree but its handle and mechanical property got worse to a certain extent. Besides that, good washing resistance of improved recoverability resulting from chitosan treatment is needed by adding crosslinkers. Organosilicon has advantages such as excellent flexibility, elasticity can the easiness in film forming due to dual characteristic of both organic and inorganic materials and unique structure. Reactive Organosilicon can create a covalent binding with other molecules of textile fibre owing to its active groups on the side base of main chains, which makes the resulting textile product possess new features and good washing resistance.
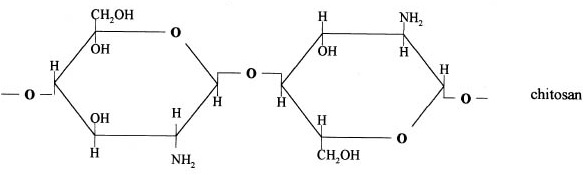
4.2 Properties of Chitosan
a) Chemical Properties of Chitosan
The chemical properties of chitosan are as follows:
- Linear polyamine.
- Reactive amino groups.
- Reactive hydroxyl groups available.
- Chelates many transitional metal ions.
b) Biological Properties of Chitosan
The biological properties of chitosan are as follows:
- Biocompatible
- Natural polymer
- Biodegradable to normal body constituents.
- Safe and non toxic (the research chitinase is noteworthy in this respect).
- Binds to mammalian and microbial cells aggressively.
4.3 Methods of Preparation
A schematic representation of the processes to prepare chitin and chitosan from raw material is shown in following figure.
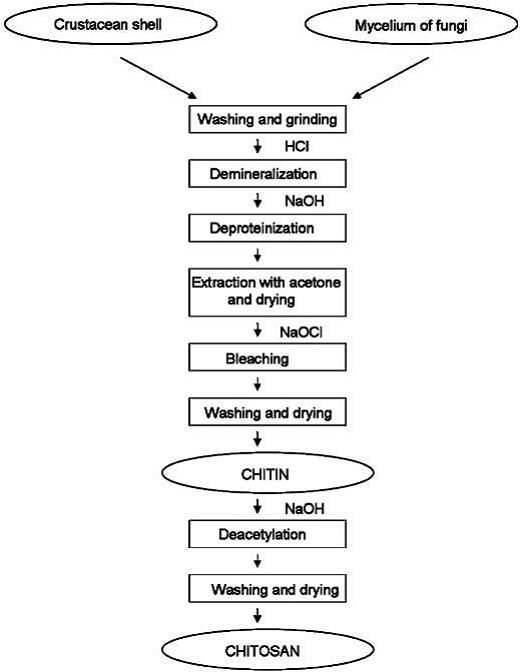
4.3.1 Chitin Extraction
As mentioned above, chitin is present within numerous taxonomic groups. However, commercial chitins are usually isolated from marine crustaceans, mainly because a large amount of waste is available as a by-product of food processing. Chitosan is produced commercially by deacetylation of chitin, which is the structural element in the exoskeleton of crustaceans (such as crabs and shrimp) and cell walls of fungi.
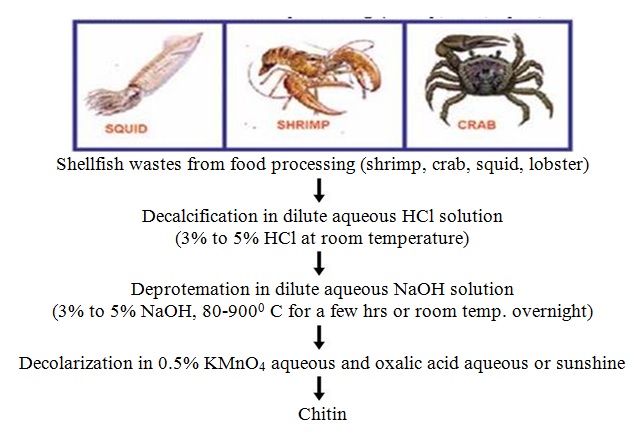
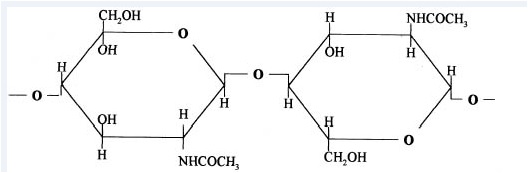
4.3.2 Chitin Deacetylation
Chitosan is prepared by hydrolysis of acetamide groups of chitin. This is normally conducted by severe alkaline hydrolysis treatment due to the resistance of such groups imposed by the Trans arrangement of the C2-C3 substituents in the sugar ring. Thermal treatments of chitin under strong aqueous alkali are usually needed to give partially deacetylated chitin (DA lower than 30%), regarded as chitosan. Usually, sodium or potassium hydroxides are used at a concentration of 30-50% w/v at high temperature (100ºC). Partial deacetylation of chitin gives rise to chitosan, a linear polysaccharide with interspersed D-glucosamine, and acetyl-D-glucosamine units. The preponderance and distribution of acetyl-D-glucosamine residues lead to differing physicochemical properties and biological responses. Chitosan is a weak cationic polysaccharide composed essentially of β (1→4) linked glucosamine units together with some N-acetylglucosamine units. It is obtained by extensive deacetylation of chitin, a polysaccharide common in nature. Chitosan is obtained by removing enough acetyl groups (CH3-CO) for the molecule to be soluble in most diluted acids. This process, called deacetylation, releases amine groups (NH) and gives the chitosan a cationic characteristic. This is especially interesting in an acid environment where the majority of polysaccharides are usually neutral or negatively charged.
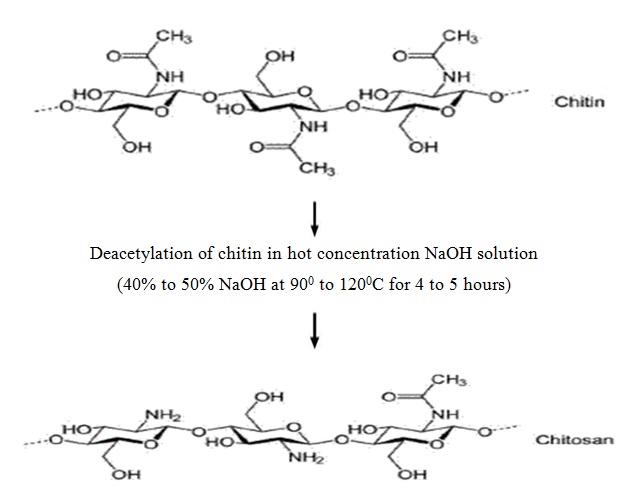
4.3.3 Chitosan Depolymerization
The main limitations in the use of chitosan in several applications are its high viscosity and low solubility at neutral pH. Low molecular weight (Mw) chitosans and oligomers can be prepared by hydrolysis of the polymer chains. For some specific applications, these smaller molecules have been found to be much more useful. Chitosan depolymerization can be carried out chemically, enzymatically or physically.
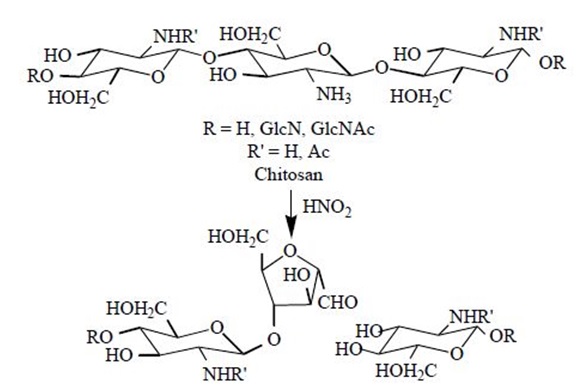
Chemical depolymerization is mainly carried out by acid hydrolysis using HCl or by oxidative reaction using HNO2 and H2O2. It has been found to be specific in the sense that HNO2 attacks the amino group of D-units, with subsequent cleavage of the adjacent glycosidic linkage. In the case of enzymatic depolymerization, low molecular weight chitosan with high water solubility were produced by several enzymes such as chitinase, chitosanase, gluconase and some proteases. Non-specific enzymes including lysozyme, cellulase, lipase, amylase and pectinase that are capable of depolymerizing chitosan are known. In this way, regioselective depolymerization under mild conditions is allowed. Physical depolymerization yielding dimers, trimers and tetramers has been carried out by radiation (Co-60 gamma rays) but low yields have been achieved.
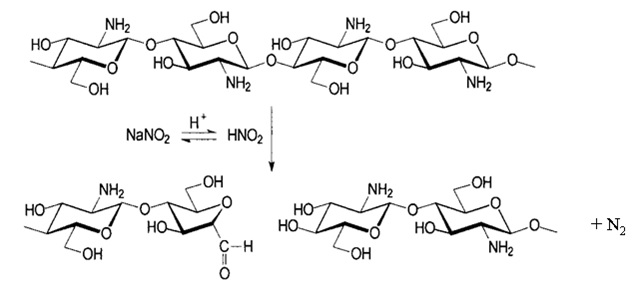
According to above, sodium nitrite chemically transforms to nitrous acid prior to depolymerization of chitosan polymer chain, resulting in chitosan with low Mw. Following to the depolymerization reaction, the aldehyde end group is also formed, which could act as a reactive group when applied onto cotton fabric. The products of depolymerized chitosans have a dramatic decrease in the molecular weight, namely 10.8 and 7 kDa, respectively. However, the nitrogen content was slightly decreased since the weight loss of amine group was relatively small when compared to the molecular weight of chitosan.
CHAPTER 5
RAW MATERIALS
5.1 Required Raw Materials
- Fabric.
- Reactive Dye.
- Chitosan
- Electrolyte (Glubar Salt).
- Sodium Carbonate (Soda ash, Na2CO3).
- Weak acid (acetic).
- Wetting Agent (Surfactants).
- Leveling Agent.
- Water.
- Sandoclean PCLF- (Detergent).
5.1.1 Fabric
Table: 5.1 Specification of Fabric
Fabric Type | 1×1 Plain Knit |
Type of Cotton | 100% cotton combed yarn |
GSM | 140 |
The fabric was scoured, bleached and enzyme by following the standard scouring and bleaching agent.
5.1.2 Dye
Table: 5.2 Specification of Dye
Common Name | Reactive Dye |
Trade Name | NOVACRON FN RED-2BL |
Company | Huntsman |
Country | Switzerland |
Molecular Formula | Molecular Formula |
Colour | Red |
Odour | None |
5.1.3 Chitosan
Table: 5.3 Specification of Chitosan
Common name | Chitosan |
Chemical Name | Poly-(1-4)-2-Amino-2-deoxy-ß-D-Glucan |
Molecular Formula | (C6H11NO4)n |
Molecular Weight | (160.9)n |
Solubility | Soluble in mild acidic medium |
5.1.4 Electrolyte (Glubar Salt)
Table: 5.4 Specification of Salt
Common name | Glauber’s salt |
Chemical Name | Sodium sulfate decahydrate |
Molecular Formula | Na2SO4·10H2O |
Appearance | White or colorless monoclinic crystals |
Solubility | Water soluble |
Taste | Walty, bitter taste |
5.1.5 Sodium Carbonate (Soda ash, Na2CO3)
Table: 5.5 Specification of Soda Ash
Common name | Sodium carbonate (also known as washing soda or soda ash) |
Chemical Name | Sodium salt of carbonic acid |
Molecular Formula | Na2CO3 |
Appearance | White powder |
Characteristics | Water softener, fixation of dye |
Solubility | Water soluble |
Procedure | Salt (sodium chloride) and limestone |
5.1.6 Wetting Agents (Surfactants)
Table: 5.6 Specification of Wetting Agent
Common Name | Wetting Agents |
Composition | Mixture of surface-active compounds. |
Appearance | Clear, colorless, slightly viscous liquid |
PH | 5.5 |
Specific Gravity at 20ºC | About 1 g/cm3 |
Suitable dilute | Very stable in hard water and to salts, alkalis, acids and bleaching agents. |
5.1.7 Leveling Agents
Table: 5.7 Specification of Leveling Agent
Common Name | Leveling Agents |
Chemical basis | Mixture of an addition complexing agent and polymers. |
Appearance | Coffee Color, low-viscosity liquid |
PH | About 7.0 |
Specific gravity at 20ºC | About 1.1 |
Suitable dilute | Cold or warm water |
General stability | Stable in hard water, Alkalis and acids. |
5.1.8 Water
An abundant supply of clean water is necessary in order to run a dyeing and finishing plant. Dye houses are usually located in areas where the natural water supply is sufficiently pure and plentiful. Knowledge of the impurities and how to remove them is important. This section will briefly discuss some of the more important water purification methods. More emphasis will be placed on dealing with trace amounts of certain metal ions which are especially troublesome. Rivers, lakes and wells represent the major sources of fresh water available for use in wet processing. Rain inevitably finds its way into rivers, streams and lakes, all classified as surface water. When water passes over the surface of the earth, it carries with it organic matter in various stages of decay and dissolves and/or suspends a certain amount of minerals, depending upon the nature of the soil or rock with which it has come in contact. Well water is surface water which has percolated through soil or rock formations. Subsoil water is usually free of suspended matter but is rich in dissolved carbon dioxide. Dissolved carbon dioxide will convert insoluble calcium carbonate (limestone) into soluble calcium bicarbonate. Presence of calcium and magnesium ions in process water is undesirable because these ions are responsible for hardness in water and lead into the formation of insoluble precipitates of soaps and dyestuffs. The bicarbonate salts of calcium and magnesium are called Temporary hardness because boiling will liberate carbon dioxide and precipitate calcium carbonate. Chloride salts of calcium and magnesium are called Permanent hardness because boiling will not cause a precipitate.
5.2 Required Machineries
Table: 5.8 Machineries Used.
Name of Machine | Model | Brand | Origin |
Infra Red Lab Dyeing Machine | Supermat | Sandolab | Taiwan |
Washing and Dry Cleaning Color Fastness Tester | 415/8 | James H. Heal | UK |
Crock Master Color Fastness to Rubbing Tester | 670 Hand Driven crock Master | James H.Heal | UK |
Perspirometer | James H. Heal | UK | |
Spectrophotometer | 650 | USA | |
Color matching cabinet |
CHAPTER 6
METHODOLOGY
6.1 Stock Solution Preparation
During the lab deep preparation a little amount of dyes and others chemicals are required. The measurement of a little amount dyes and chemicals are very complex.1 gm of dye has take and soluble in 100 ml of warm water and make 1% dye stock solution. Similarly 5% of Na2Co3 (Sodium carbonate), 10% gluber salt of stock solution have make. By the preparation of stock solution we can easily take required amount of dyes and chemicals from the stock solution by the following calculation.
……………………………….Total Liquor x Recipe amount
Amount of Chemicals = ——————————————————-
…………………………………..1000 x Stock solution%
………………………Weight of materials x Shade%
Amount of Dyes = ———————————————————
……………………………….Stock solution%
6.2 Sample Preparation
The (Scoured, Bleached and Enzyme) fabric has cut and make sample about 5 gm ±0.5% by the precious electronic balance. There have to make an indicator on the sample to distinguish each to others by numbering on sample salves. The sample size has required as rectangular to take crocking fastness test. Now all samples are soak in distill water for few minute and squeeze well therefore the sample are ready for dyeing.
6.3 Recipe Formulation
To perform the experiment, there have differences between salt & chitosan evaluation of self shade (NOVACRON RED FN-2BL). For 1% dyes with gluber salt & various amount of chitosan without salt such as 1.0%, 2.0%, 3.0%& 4.0% chitosans are used and analyses with them. The standard recipe is following:
Table: 6.1 The Standard Recipe
Variables | Amount |
Dyes | 1.0 % (owf) |
Salt | 20 gm/L |
Soda ash | 8 gm/L |
Wetting Agent | 1 gm/L |
Leveling Agent | 1 gm/L |
ML Ratio | 1:10 |
The experiment has performed by the variation of chitosan concentration in the dye bath and others auxiliaries & chemicals are remain constant as standard recipe. The experimental recipes are following:
6.4 Experimental Recipe
Table: 6.1. Recipe for NOVACRON RED FN-2BL for 1.0% (owf) Shade with Salt (Standard).
Chemicals | Amount |
Dyes (%) | 1.0 |
Salt gm/l | 20 |
Soda ash gm/l | 8 |
Wetting Agent gm/l | 1.0 |
Leveling Agent gm/l | 1.0 |
ML Ratio | 1:10 |
pH | 10.1 |
Table: 6.2 Recipe for NOVACRON RED FN-2BL for 1.0% (owf) Shade by Using Chitosan instead of Salt
Chemicals | Sample-1 | Sample-2 | Sample-3 | Sample-4 |
Chitosan (%) | 1 | 2 | 3 | 4 |
Dyes (%) | 1.0 | 1.0 | 1.0 | 1.0 |
Soda ash (gm/l) | 10 | 10 | 10 | 10 |
Wetting Agent(gm/l) | 1.0 | 1.0 | 1.0 | 1.0 |
Leveling Agent (gm/l) | 1.0 | 1.0 | 1.0 | 1.0 |
ML Ratio | 1:10 | 1:10 | 1:10 | 1:10 |
6.5 Fabric Preparation for Dyeing with Chitosan
Take 100ml of water
↓
Specific amount of chitosan
↓
Add 1 or 2 drops of acetic acid
↓
Warm up & shake until dissolve
↓
Filtration
↓
Extract water +fabric
↓
60ºC Temp & 60 min
↓
Drying
6.6 Dyeing Procedure
A) With Salt
At first take all auxiliaries and dyes from the stock solution in the dye bath and take water to maintain 1:10 liquor ratios therefore fabric is added in dye bath at room temperature and run 10 minute. Gluber salts are added in dye bath and temperatures gradually increase (2o/min) up to 60oC. Now soda ash is added in dye bath for fixation of reactive dye from the stock solution of sodium bicarbonate and measure pH of dye bath and run 60 minute at 60oC. Complete dyeing the dye liquor has drain.The process diagram is following:
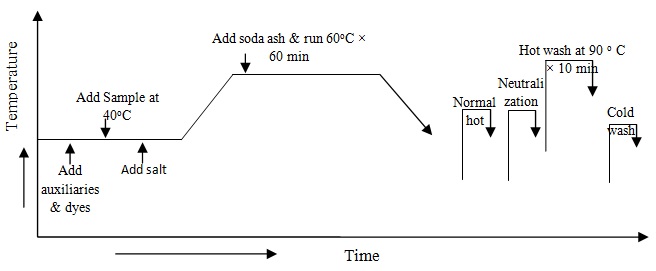
B) With Chitosan
At first chitosan treated sample has collected & take all auxiliaries and dyes from the stock solution in the dye bath and take water to maintain 1:10 liquor ratio therefore fabric is added in dye bath at room temperature and run 10 minute. Temperatures gradually increase (2o/min) up to 60oC. Now sodium bicarbonate is added in dye bath for fixation of reactive dye from the stock solution of sodium bicarbonate and measure pH of dye bath and run 60 minute at 60oC. Complete dyeing the dye liquor has drain. The process diagram is following:
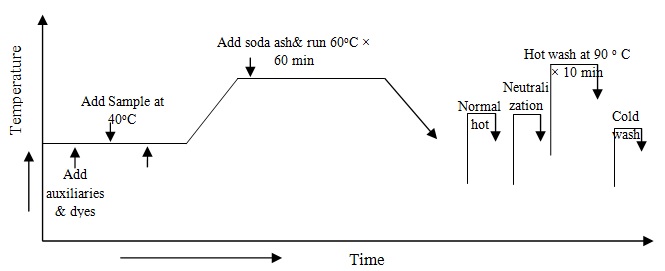
6.7 After Treatment
Removal of hydrolysed and unreacted dye from the goods is a vital step after dyeing. The amount of unfixed dye remaining in a cotton fabric dyed with reactive dyes may have to be less than 0.002% owf. Although bleeding out of such a small amount during subsequent washing by the consumer will not significantly alter the depth of shade of the material, it can visibly stain adjacent white goods. This is usually unacceptable. The entire washing operation involves achieving a compromise between the effectiveness of removal of unfixed dye and the cost of the large volumes of water used, including the heating costs. Low liquor ratio washing saves water but gives less dilution of the washing liquors. To remove unfixed dyed required the material is operating at atmospheric pressure. It can possible to carry out soaping at temperatures 90°C for 10 minute.
6.8 Drying & Finishing
The sample is squeeze well to remove the excess water and dry the sample in the CARBOILITE oven dryer which made by England. The drying temperature is 100ºC for 20 minute. Now the sample is calendaring at about 150ºC for few minute to make smooth surface of the fabric.
6.9 Shade Matching
Under the light box (Verivide light box made by England) all samples which are prepared by the different concentration of alkali used to fixing system are matching each to others. The Illuminant D65 is used to matching the shade. Which samples are similar depth of shade to the observer those have sent to make CMC report to compare difference of shade each to others. The CMC reports are taken from spectrophotometer.
6.10 Color Fastness to Rubbing Test (ISO 105 X 12)
The fastness test to rubbing used on a variety of fabric to evaluate the transfer of surface dye from the test fabric when it is applied surface friction or rubber against a rough surface. Crock meter & Grey scale are used for this test. To cut the fabric size 10cm × 4cm & The rubbing cloth size 50mm × 50mm.The crocking cloth against which the sample is rubbed is white, bleach, but without finish and undyed cotton fabric. Rubbing time: 10 Cycle/10 second.
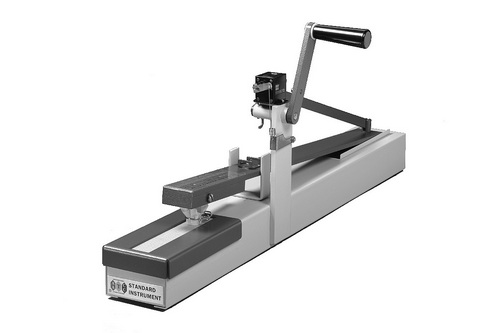
Working procedure:
- The rubbing arm is attached to the hook.
- Center a piece of abrasive paper, abrasive side up, on the base of the Crock meter.
The paper’s long dimension should be in the direction of the rubbing. - The specimen is placed flat and face-up on the abrasive paper. The specimen’s long dimension should be in the direction of the rubbing.
- A piece of test cloth is centered over the finger so that the weave is parallel with the direction of rubbing. Wrap the sides of the cloth evenly around the finger, making sure the cloth is smooth and taut over the finger’s rubbing area.
- The covered finger is then lowered onto the test specimen.
- The cycle counter is reset.
- The handle is turned at the rate of one turn per second for ten times. (Each back and forth motion of the arm equals one stroke and at a speed of 1 stroke/second.)
- After 10 strokes the specimen is removed and compared with the grays. The acceptable range is normally 3.This visual assessment is done in a color matching cabinet under standard lighting D65 (Artificial Daylight).
6.11 Color Fastness to Wash
The resistance of the loss of color of any dyed or printed material to washing is referred to as its wash fastness. Rota Wash, Scissor, Stitch machine are for this test. To cut the Fabric size 10 cm × 4 cm & also Multi fiber fabric .The color fastness to washing is measured by ISO Recommendation No. 1 (ISO 105 C03). A rating of 1(poor) – 5 (excellent) was assigned to each of the six fiber strips on the fabric.
Recipe:
- Soap : 5 g/l
- Soda ash : 2 g/l
- Temperature : (60 ±2)ºC
- Time : 30 min
- ML Ratio : 1:50
Working Procedure:
- Stitch the specimen with multi fiber fabric in one side (length direction).
- Weight the specimen and calculate the volume of wash liquor required for ISO method given 150 ml liquor.
- Place the specimen in the container with the wash liquor.
- Run the machine and raise the temperature to 50ºC and run for 30 min.
- At the end of the test, place the specimen in the beaker and wash with 2 litter distilled water for 2 min & continuously starring the sample. Then washing in running tape water for 2 min. Excess water remove by hand squeezing.
- Dry the composite specimen in incubator, temperature not more than 60ºC. Then keep in relax for 1 hours.
6.12 Color Fastness to Perspiration Test:
To assess the degree of change of shade or cross staining due to perspiration.
Apparatus:
- Chemical balance accurate to 0.01 gm.
- Volumetric flask.
- Beaker.
- PH meter.
- Petri dishes.
- Glass plate.
- Multi fiber fabric
- Incubator.
Sample size: (10×4) cm.
Requirement of Alkaline Solution:
- L – Histridine Mono-Hydrochloride monohydrate 0.5 g/l
- Di-Sodium Hydrogen orthophosphate di-hydrate 2.50 g/l
- NaCl 5 g/l
- PH 8.0
- Distilled water 1000ml
- Time 4 hours
Working Procedure:
- Amount of alkaline solution=220 ml-250 ml and pH 8.0±0.05
- After made perspiration fabric drop down the solution without glass at 30 min & after 30 min the solution fall down and fabric again drop down the solution with glass at 15 min and after 15 min the fabric dry & tested color.
- Dry the composite specimen in incubator, temperature not more than 60ºC. Then keep in relax for 1 hours.
CHAPTER 7
RESULTS AND DISCUSSIONS
7.1 Measurement of Dye Absorption
The objective of colorant formulation in the textile context is to calculate the amounts of dyes required to colour a given material with exactly the required shade. The basic information required is the relationship between reflectance of the dyed material and the concentration of the dyestuff. Many efforts have been made to arrive at a mathematical expression which will give the desired linear relationship. For a given CIE Illuminant and standard observer, the reflection spectrum of a sample determines the coordinates for its colour in any colour space. One method of matching the colour of a sample is to reproduce its reflection spectrum with an appropriate mixture of colorants. The colour coordinates of the sample and target must then be identical. This is called spectrophotometric matching. Many formulation procedures for spectrophotometric matching use a simplified form of the Kubelka–Munk equation relating the absorption and scattering coefficients and the concentrations of the colorants in the sample with its overall reflectance. For a mixture of a number i of colorants in a sample, the global Kubelka–Munk K/S value at a given wavelength is:
………(1 – R)2
K/S = ———————-
…………2R
Where, K and S are the respective values of the absorption and scattering coefficients of the various dyes and of the undyed textile material. R is the reflectance of a sample of fabric that is sufficiently thick to prevent light transmission through it.
7.1.1 Graphical Representation of Measurement of Dye Absorption
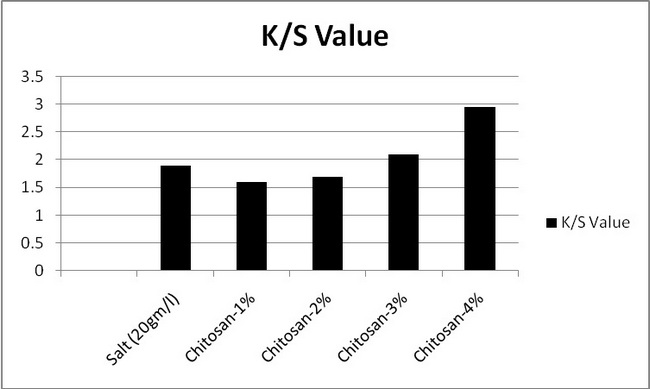
In the above figure 7.1 the absorption of samples 1,2,3,4 was compared to the standard sample. It is seen that the absorption of samples 1and 2 was decreased from the standard sample. And absorption of samples 3and 4 was increased from the standard sample. It is said that absorption is increased with increasing the chitosan%. Here maximum absorption of chitosan treated sample was higher salt treated sample.
7.2 Assessment of Rubbing Fastness Test
Table: 7.1 Color Change and Staining to Multifibre Fabric in Rubbing Fastness Test.
Sample No. | Shade% | Salt (g/l) | Chitosan% | Test Result | |
Dry | Wet | ||||
Standard | 1 | 20 | – | 5 | 4 |
Sample-1 | 1 | – | 1 | 4/5 | 3 |
Sample-2 | 1 | – | 2 | 4/5 | 3 |
Sample-3 | 1 | – | 3 | 4/5 | 2/3 |
Sample-4 | 1 | – | 4 | 4 | 2/3 |
The gray scale rating for samples 1 – 3 were 4/5 (very good to excellent) and samples -4 was 4 (very good) whereas the standard sample rating was 5 (excellent) for dry rubbing. Also the gray scale rating for samples 1-2 were 3 (good), and sample 3-4 were 2/3 (poor to good), whereas the standard sample rating was 4 (very good) for wet rubbing.
So from above result it is seen that there is no major change in fastness to rubbing of chitosan treated samples compare to the standard sample at dry rubbing. There is only change of different chitosan treated samples compare to the standard sample in wet rubbing fastness.
7.3 Assessment of Wash Fastness Test
Table: 7.2 Color Change and Staining to Multifibre Fabric in Wash Fastness Test.
Sample No. | Shade (%) | Salt (g/l) | Chitosan (%) | Test Result | ||||||||
CC | Color Staining | |||||||||||
Ac | C | N | P | A | W | |||||||
Standard | 1 | 20 | – | 4/5 | 5 | 4/5 | 5 | 5 | 4/5 | 4/5 | ||
Sample-1 | 1 | – | 1 | 4/5 | 4/5 | 4/5 | 5 | 5 | 4/5 | 4/5 | ||
Sample-2 | 1 | – | 2 | 4/5 | 5 | 4/5 | 5 | 5 | 4/5 | 4/5 | ||
Sample-3 | 1 | – | 3 | 4/5 | 4/5 | 4 | 5 | 5 | 4/5 | 4/5 | ||
Sample-4 | 1 | – | 4 | 4/5 | 4/5 | 4 | 5 | 5 | 4/5 | 4/5 |
A washing fastness test was carried out for the dyed samples (with chitosan) and was compared with those of reference (standard, with salt) sample with the grey scale ratings for the washed samples. In table 7.3 it is seen that fading i.e. color change of all samples is 4/5 (very good to excellent). So it can be said there is no change in color or a very slight loss in color for washing. In case of staining nylon and polyester all fibers gives ratting 5 (excellent). Acrylic and wool shows the rating of 4/5 (very good to excellent) different sample. Only Acetate and cotton shows different rating within very good to excellent but not unacceptable.
7.4 Assessment of Perspiration Fastness Test
Table: 7.3 Color Change and Staining to Multifibre in Perspiration Fastness Test.
Sample No. | Shade (%) | Salt (g/l) | Chitosan (%) | Test Result | ||||||||
CC | Color Staining | |||||||||||
Ac | C | N | P | A | W | |||||||
Standard | 1 | 20 | – | 4/5 | 4/5 | 4/5 | 4/5 | 4/5 | 4/5 | 4/5 | ||
Sample-1 | 1 | – | 1 | 4/5 | 4/5 | 4/5 | 4/5 | 4/5 | 4/5 | 4/5 | ||
Sample-2 | 1 | – | 2 | 4/5 | 4/5 | 4/5 | 4/5 | 4/5 | 4/5 | 4/5 | ||
Sample-3 | 1 | – | 3 | 4/5 | 4/5 | 4/5 | 4/5 | 4/5 | 4/5 | 4/5 | ||
Sample-4 | 1 | – | 4 | 4/5 | 4/5 | 4/5 | 4/5 | 4/5 | 4/5 | 4/5 |
In perspiration fastness test for the dyed samples (with chitosan) and was compared with those of reference (standard, with salt) sample with the grey scale ratings for the washed samples. In table 7.4 it is seen that fading i.e. color change of all samples is 4/5 (very good to excellent). So it can be said there is no change in color or a very slight loss in color for washing. Also in case of staining all fibers gives ratting 4/5 (excellent) and there was no unacceptable rating.
CHAPTER 8
CONCLUSION
8.1 Conclusion
Reactive dyeing process has been completed at 60ºC and the added time remains 60 mins. Fixation and exhaustion have been completed at 60ºC. The addition of glubar’s salt is necessary as it increase the exhaustion of the dye bath. From the researched it has been seen that salt increase the dye exhaustion but cause environmental pollution.
The results of this study conclude the chitosan treatment of cotton fabric improved depth of shade on dyed fabrics. This may be because the chitosan treated cotton fabric provided more dye sties to attach more dye extraction than that of the untreated fabric. The cotton fabric treated with chitosan not only provided better depth of shade but also provided better wash-fastness and light-fastness than those of untreated fabric.
To confirm the evenness of the depth of shade different molecular weight chitosan is used. In this study, depolymerization of chitosan using sodium nitrite to prepare various low Mw chitosans was carried out. FTIR analysis provided evidence to support that depolymerized chitosan contained an increase in free amine groups as a result of deacetylation of remaining N-acetyl groups. Then, obtained chitosans combined with mangosteen dye extract were applied onto cotton fabric. An effect of chitosan application methods on the properties of dyed fabrics was evaluated. In all cases, the pre-dyeing method in which the fabrics were treated with chitosan solutions prior to dyeing produced the optimum K/S value. An increase in chitosan concentration resulted in an increase in the dyeability of dye. This effect was associated with the presence of bonded chitosan through the chemical reaction of the chitosan aldehyde group with cellulose. As a result of low Mw employed, depolymerized chitosans with higher concentration (compared to native chitosan) could be employed without the concession of a stiffness problem. The reason for this is due to their low Mw depolymerized chitosans exhibited no film formation.
References:
- Broadbent, A. D. (2001). Basic Principles of Textile Coloration. west Yorkshire , UK, England: Sosiety of dyers and Colourists.
- Hustsman. (2004, 06 02). Hustsman Textile Effects. Safety Data Sheet .
- Ingamells, W. (1993). Colour for Textile. West Yorkshire, School of Home Economics and Institutional Management, University of Wales, England: Society of Dyers and Colourists.
- Park, J., & Shore, J. (2004). Practical Dyeing (Vol. 2). West Yorkshire, UK, England: Society of Dyers and Colourists.
- Rebecca, R. B. (2005). Fibre Reactive Dyes with Improved Affinity and Fixation Efficiency.
- Tomasino, D. C. (1992). Chemistry & Technology of Fabric Preparation and Finishing. Raleigh, North Carolina State University, North Carolina: Department of Textile Engineering, Chemistry & Science College of Textile.
- Trotman, E. (1975). Dyeing and Chemical Technology of Textile Fibre (Fifth ed.). High Wycombe, London, England: Charles Griffin & Company Ltd.
- Vassileva, E. V. (2008). The Kinetic Modle of Reactive Dye Fixation on Cotton Fibres. Bulgaria: Journal of the University of Chemical Technology and Metallurgy.
- Sundrarajan, R. Rajiv Gandhi, A. Rukmani, S. Selvam, J. Suresh and S. Gowri. Chitosan and Cyclodextrin Modification on Cellulosic Fabric for Enhanced Natural Dyeing.
- Inmaculada Aranaz, Marian Mengíbar, Ruth Harris, Inés Paños, Beatriz Miralles, Niuris Acosta,Gemma Galed and Ángeles Heras, Department of Physical Chemistry II, Faculty of Pharmacy, Institute of Biofunctional Studies, Complutense University, Paseo Juan XXIII, Madrid 28040, Spain, Functional Characterization of Chitin and Chitosan.
You may also like: Dyeing of Cotton Fabric with Reactive Dyes