What is Fabric Shrinkage?
Shrinkage is an undesirable property of fabric, so in order to manufacture high-quality clothing, shrink-resistant fabric should be used. Shrinkage can be defined as a dimensional change in a fabric or garment caused by an application of a force, energy or a change in environment that either allows the fabric to relax or forces it to move in a given direction.
The shrinkage of natural fiber fabrics on washing has been one of the major problems requiring attention by textile technologists. A part of fabric shrinkage is due to stretching by applied tensions during manufacturing and finishing operations.
Fabric shrinkage is a term associated with a reduction in the dimensions of fabric. A fabric on the weaving machine is under warp and weft tensions. As soon as the fabric leaves the templates that hold it in place, its width decreases. Similarly when the fabric is taken off the loom, one can observe a reduction in length and width; which can be checked by an increase in the ends and picks per cm. This is due to the release of tensions in the warp and weft so that the yarns recover to their relaxed state. This equilibrium is achieved by balancing of internal energy with the inter-yarn frictional force. It may be termed a pseudo-equilibrium and is designated as dry relaxation. The dimensional change accompanying the release of fiber strains imparted during manufacturing which have been set by the combined effects of time, finishing treatments and physical restraints within the structure is called relaxation shrinkage.
However, shrinkage is not only due to the release of strains imposed during manufacturing processes; it is also due to swelling caused by wetting bringing about an internal arrangement of the material resulting in external shortening. The diameter of cotton hairs may increase by 20% and the contraction due to swelling may amount to 2% out of the total fabric shrinkage, which is about 10%. Materials made of rayon show much greater swelling and consequent greater shrinkage. Unlike cotton, rayon may exhibit up to 9–10% yarn shrinkage. Fabrics made of synthetic fibers swell only very slightly on wetting, and so such fabrics are almost free from this type of shrinkage.
Mechanism of Fabric Shrinkage:
The mechanism of shrinkage of fabrics made from hydrophilic yarn. Shrinkage may be regarded as a change in yarn spacing. On wetting a fabric, water is absorbed by the fibers in the yarn and causes swelling of fiber and yarn. Typically an increase of 10% in yarn diameter can be expected. Nevertheless, transverse swelling of fibers results in longitudinal shrinkages of only 1%. Yarn shrinkage, which is related to the degrees of twist imparted on the yarn during spinning, can give rise to more shrinkage but accounts for shrinkages of only 2% in typical fabrics. The explanation of cloth shrinkage lies in the fabric structure. Figure 1 shows one repeat along the warp. When the cloth is wetted the yarn increases in diameter. If the crossing weft threads are to remain the same distance apart as they are in the dry state, than warp would have to extend. As the cloth is under no constraint, the weft threads move closer together in order that the warp yarn can remain the same length. Therefore the cloth shrinks in the warp direction. A similar explanation is valid for shrinkage in the weft direction. The major cause of fabric shrinkage due to the swelling of threads on wetting is that the thick warp yarn requires more space to enable fibers to pass over and under the swollen weft yarn. The warp adopts an undulating path and shrinks the cloth.
It was found that as water is absorbed into the fabric the transverse swelling of the fibers and yarns induced shrinkage in three ways: longitudinal fiber shrinkage, yarn shrinkage and crimp accentuation. The mechanism of crimp accentuation is illustrated in Figure1, which represents the position of warp and weft yarns before wetting.
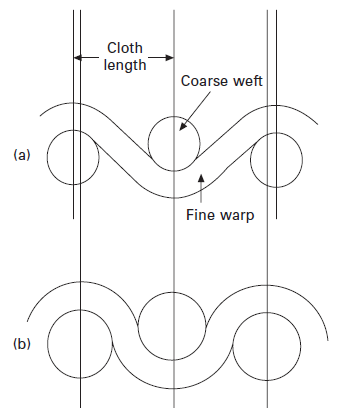
It also shows the swelling of both yarns when the fabric is wetted. For the fabric to maintain the same external dimensions it had before wetting, i.e. not shrink at all, the warp yarns would have to extend by a given length. An extension would be necessary for the warp yarns to travel around the swollen weft yarns. There is an energetically simpler mechanism that accommodates the increased path of the warp yarns. In this mechanism, the weft yarns move closer together and warp path length remains the same. Likewise, an increase in the diameter of the weft yarns results in the movement of warp yarns closer together. For this reason, shrinkage of the fabric in both directions is observed. From this description it is clear that the fabric structure has a significant effect on a fabric’s response to wetting. The degrees of yarn twist, yarn diameter and sizing have some influence, but the spacing of yarns (degree of crimp) is the most critical factor. Thus, closer yarn spacing and relatively compacted yarns give greater shrinkage effects. The mechanization of the textile industry gave rise to an abundance of tightly woven fabrics produced with power spinning and power weaving processes. This type of fabric shrinks more than a handmade fabric at high moisture levels.
References:
- Woven Textile Structure: Theory And Applications By B. K. Behera and P. K. Hari
- Principles of Textile Finishing By Asim Kumar Roy Choudhury
- Chemical Technology in the Pre-Treatment Processes of Textiles by S. R. Karmakar
- Woven Fabric Structure Design and Product Planning by Hayavadana
You may also like: Textile Testing Types, Purposes, Methods and Importance