Viscose Rayon Fibre – An Overview
Ashish Kumar Dua
M.Tech, Dept. of Textile Engineering,
Indian Institute of Technology (IIT), Delhi.
Email: ashisdua@gmail.com
Introduction of Viscose Rayon Fibre:
- Viscose rayon fibre is oldest regenerated cellulose fibre.
- Viscose rayon fibre is biodegradable and renewable polymer.
- Common sources wood pulp and cotton lint.
- Highly purified wood pulp consists of of 90-95% cellulose called chemical cellulose and dissolving pulp.
- The process used to make viscose either continuous or batch process.
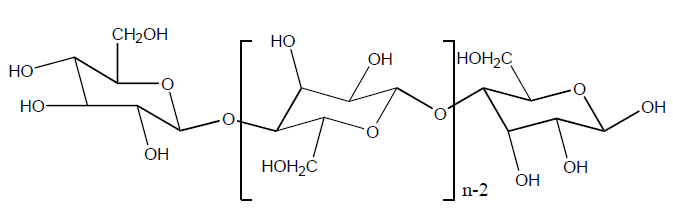
Manufacturing Process Flow Chart of Viscose Rayon Fibre Manufacturing:
Steeping
[Cellulose pulp 13”X18” or 20X30” and cellulose: 87-98% are vertically stacked in 3”-6” apart to each other and tank contain 17-18% NaOH. (C6H10O5)n + nNaOH —> (C6H9O4ONa)n + nH2O]
↓
Shredding
[To make cellulose in fluffy crumbs by mechanical action]
↓
Ageing
[De-polymerization]
↓
Xanthation
[Add CS2: 32-35%, 1-3 hr, 20-30oC 1-4 rev.
(C6H9O4ONa)n + nCS2 —-> (C6H9O4O-SC-SNa)n ]
↓
Dissolution
[Add 4-6% NaOH + agitators and total sulphr-2 to 2.5%]
↓
Ripening
[Storage at 15-25 0 c for 1-3 days. In this time redistribution of xanthate take place.
(C6H9O4O-SC-SNa)n + nH2O —> (C6H10O5)n + nCS2 + nNaOH]
↓
Filtration and Blending
[Remove undissolved material, bubble air]
↓
Spinning
[H2SO4-8-10%
Na2SO4-16-24%
ZnSO4-1-2%
(C6H9O4O-SC-SNa)n + (n/2)H2SO4 –> (C6H10O5)n + nCS2 + (n/2)Na2SO4
Spinning speed may be high as 120m/min at Spinning Bath ]
↓
Neutralization
↓
Drying and Winding
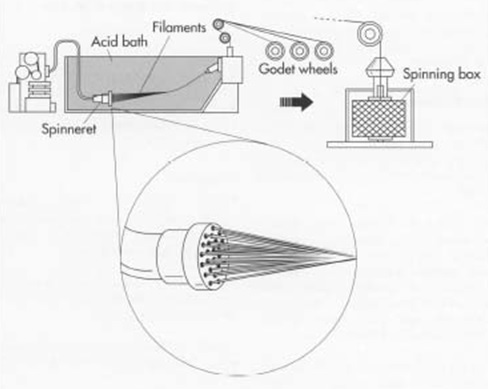
Properties of Viscose Rayon Fibre:
- Tenacity ranges between 2.0 to 2.6 g/den when dry and 1.0 to 1.5 g/den when wet.
- Wet strength of the viscose rayon fibre is of importance during its manufacturing and also in subsequent usage. Modifications in the production process have led to the problem of low wet strength being overcome.
- Dry and wet tenacity extend over a range depending on the degree of polymerization and crystallinity. The higher the crystallinity and orientation of rayon, the lower is the drop in tenacity upon wetting.
- Thermal properties: Viscose rayon loses strength above 149°C; chars and decomposes at 177 to 204°C. It does not melt or stick at elevated temperatures.
- Chemical properties: Hot dilute acids attack rayon, whereas bases do not seem to significantly attack rayon. Rayon is attacked by bleaches at very high concentrations and by mildew under severe hot and moist conditions. Prolonged exposure to sunlight causes loss of strength because of degradation of cellulose chains.
- Abrasion resistance is fair and rayon resists pill formation. Rayon has both poor crease recovery and crease retention.
Role of Zinc in Spinning Bath:
Spinning With Modifiers:
- Modifiers enhance the action of zinc in the spinning bath without effecting the viscose.
- Formation of semipermeable membrane by the combined action zinc ions by the product trithocarbamate ions viscose and modifiers and makes an barrier which retards the diffusion of both Zn+ and H+.
- So the acidification boundary shift further away from the nozzle in the presence of modifiers.
Modifiers |
Tertiary amine |
Quaternary ammonium salt |
Polyoxyalkylene derivative |
Polyoxyhydroxy polyamide |
Dithiocarbamates |
Tyre yarn:
A viscose solution of viscosity 100 poise containing modifiers 1-3% by weight of cellulose and with a CS2 content of 40% is spun under ripe into a aqueous spinning bath containing –
- H2SO4 —> 8-10%
- Na2SO4 —> 16-24%
- ZnSO4 —> 6%
The spin bath temperature is kept around 550C and the spinning speed is between 40 and 60 m/min. The stretch applied is 75-125%.
Modified high wet-modulus yarns-
The condition of viscose solution and spinning bath composition are generally similar to those tyre yarns.
Spinning bath temperature 350C is kept lower because it gives more deformable gel necessitating a slower spinning speed 20-40 m/min The result is that gel fibres are stretched at an earlier state of the gel dehydration and decomposition when the gel is more plastic and can be stretched more (125%-150%).
Polynosic fibre:
It is similar to rayon process but with-outing having the step of ageing and ripening stage, with dilute acid concentration and zinc sulphate.
Its having the high crystallinity and orientation, chemical resistance ,high wet modulus and more dimension stable.
Spinning bath-
- H2SO4—–>2-3%
- Na2SO4——>4-6%
- Temperature——>25oC
- Spinning speed——>20-30m/min
- Stretch——>150-300%
Crystallinity(%) | Birefringence | |
Standard Viscose | 45.2 | 0.027 |
Tyre yarn | 41.5 | 0.037 |
Polynosic | 55.2 | 0.046 |
Super high wet modulus rayon:
By adding 1% formaldehyde to spin bath.
Stretch – 500-600%
Fibre variant for improved bulk and handle:
To produce high performance crimped fibres where the bulk is due to the interaction between the fibres, creating bulk in resultant yarns and fabric. The second approach has been to produce an inherently bulky fibre using an inflation technique during fibre production.
Composition | Typical range(%) |
Cellulose | 7-7.5 |
NaOH | 6-7.5 |
CS2 | 30-32 |
Modifiers: Dimetylamine | 0.8-1.5 |
Polyethylene glycol | 0.8-1.5 |
We can produced different types of fibres-
- High performance crimped fibres.
- Super absorbent fibres.
- Flame retardant fibres.
Incorporation of carbon in viscose fibre:
1. Incorporation of carbon black for antistatic properties-
Electrically conductive carbon is used for the production of electrically conductive fibre. For the production of the electric conductive fibre a slightly alkaline electric conductive carbon black with a particle size 20 nm is dispersed in water and mixed in viscose solution prior to spinning.
2. Incorporation of graphite-
Incorporating 40% of lubricating graphite with a purity 99.5% into viscose yields fibres with excellent lubricating properties which as packing and sealing for crankshafts. Packings from graphite containing viscose fibers may be used to a temperature of 180-200oC.They are stable in the pH range 5-9.
Alternative Method to Dissolve to Cellulose:
A. N-Methylmorpholine N-Oxide and Water-
- It is the best solvent to dissolve viscose fibre.
- Its having strong oxidant property due to which it can dissolve cellulose.
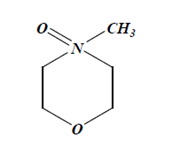
Dope Preparation:
Its having high potential to dissolve cellulose up to 50%.
Mixture transfer in air tight vessel
↓
Mix and stirred
↓
Heat it up to 130oC for 30 min
Disadvantage-
- During the dissolving step time and temperature are maintained properly otherwise thermal degradation and explosion takes place. Generally temperature is around 1300C.
- If the temperature is goes above 1500C, DP of cellulose goes down for this we add some phenolic oxidant. It stabilizes the solution and finally oxidize the colour compound.
B. N-N Dimethylacetamide and lithium chloride-
- It is another solvent which dissolve cellulose. It directly linked with very high reproducible.
- It was observed that fibres from wet spinning process exhibited superior properties.
- It makes an complex with OH-group of cellulose and help to dissolve cellulose. Solution is much stable in nature. It is stable few years in room temperature.
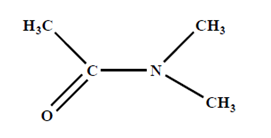
Dope preparation-
DMAc + Cellu-OH of mixture
↓
Distillated at 165oC in nitrogen atmosphere, 30 min
↓
Reduce temperature at 100oC +Licl
↓
Stirring continuously at 80oC for 40 min
↓
Solution is ready
C. Ionic liquid
Salt that melt at temperature below 100oC called as ionic liquid or green solvent.
Properties-
- Chemically and thermally stability.
- Non-flammability
- Generally contain imidazoloium, pyridinum or organic ammonium cation. The anion could be chloride, bromide. Room temp. have more stronger complex.
- Cellulose can be dissolved, solubility of cellulose and its properties can be easily controlled by selection of ionic liquid compound.
- At high chloride concentration is responsible for breaking for hydrogen network. Thus allowing to dissolve cellulose.
- Dope solution can be easily precipitated by the addition of water, ethanol or methanol
- The regenerated cellulose is hardly degraded and has almost the same degree of polymerization and polydispersity as the initial cellulose.
- The ionic liquids can be recovered and reused by various methods, such as evaporation, ionic exchange, reverse osmosis and salting out.
Ammonia /ammonium thiocyanate:
Advantages-
- It has an excellent dissolving power as a solvent for cellulose.
- Low cost and readily available.
- Due to boiling solvent 700c, as a result it can handled easily.
- No degradation of cellulose.
- Solvent preparation (NH3/NH4SCN 24.5/75.5) is very simple.
Dope preparation:
Require amount of cellulose +Ammonia + Ammonium thiocyanate mix it
↓
Place it and mixed with hand and homogenized
↓
The bag place in cool place at -33oC for few mins
↓
Mixture pass through shearing force at room temperature
↓
Increase temperature up to 40oC to make solution
Amine salt:
Two component system (amine salt) consisting of hydrazine or ethylenediaine and various. Thiocyanate salt such as LISCN, NaSCN or KSCN that dissolve cellulose pump. A high concentration 40-50% salt is generally required to obtain high concentration up to 18-20% spinning dope.
Dope preparation:
Solvent +cellulose in polyethylene bag
↓
Place at -10oC for few hours
↓
Increase temperature up to 50oC
↓
Apply shearing force for 30 min to dope preparation
Development in process technology and process chemistry:
Difficulties-
- Old batch-wise process to continuous or semi-continuous system. In the batch wise process the sequence of steeping, pressing and ageing took up to 40 hr. to produce alkali cellulose.
- Difficulties in ensuring contact temperature and equal ageing time, because a large no. of bins involved, frequently resulted in a variable degree of polymerization in the resultant viscose.
Process-
- In the modern plants bales of wood pulp are automatically fed into continuously sulrry.
- By the use of catalyst and elevated temp during ageing have reduced to time 4-5 hr.
- Xanthation process has been improved with the use of wet churns. In which both xanthation and mixing carried out.
- More recently the introduction of back flush filters with non-woven metal screens has improved the filtration efficiency with the new non woven metal screens the filtration amount has increased 50 fold. Thus the filtration size could be decreased.
- Completely automatization.
Process chemistry- Reduction in chemical used such as CS2, NaOH and H2SO4
Process-in-process- Its also known as double steeping process operation of aged alkali cellulose at lower alkali concentration (10-12%). A second steeping after ages reduces the amount of free alkali in the crumb without changing the bound alkali. This reduces the formation of by-product and improves distribution of xanthate group to get a stable viscose
Other process-
- Activation of cellulose with liquid ammonia prior to xanthation also reduces CS2 consumption by as much as 33%.
- Xanthation in the presence of surfactants like Berol spin decreases CS2 consumption without effecting the quality of rayon produced. The addition of urea to the steeping solution result in change viscosity of viscose, the ripening time decreases and a high degree of xanthate substitution is obtained. It is presumed that complex with the alkali cellulose is formed which control the side reactions occurring during xanthation process.
Conclusion:
- Development in process technology and process chemistry are much environment friendly
- Polynosic fibre show high crystallinity, high resistant, high dimension stability.
- By different solvent, spinning specifications ,modifiers . We can make end use product.
- Solvent is very costly so need to recycle it.
- Ethylenediamine/KSCN System is the best solvent.
References:
- Spinning of cellulose from N-methyl morpholine N-oxide in the presence of additives, polymer 1990, vol 31, march.
- Structure formation of regenerated cellulose materials from NMMO solutions, progress in polymer science 26(2001). 3.Novel cellulose solvent system and dry jet wet spinning of cellulose ED/KSCN solution, by hyun jik cel (thesis)
- https://textilelearner.net/rayon-fiber-types-properties/
- Life cycle assessment of man-made cellulose fibres, lenzinges berichte 88(2010)
- Modified polynosic fibres.
- Handbook of fibre chemistry, M lewin and E.M pearce.
- V.B Gupta and V.K Kothari, Manfacturing of fibre technology 481-513.
You may also like:
- Properties, Production and Uses of Viscose Fiber
- Sisal Fiber: Properties, Production Process and Uses
- Properties, Processing and Uses of Kenaf Fiber
- Milkweed Fiber: Properties, Processing and Applications
- Kapok Fiber: Properties, Processing and Applications
- Hemp Fiber: Properties, Processing and Uses
- Properties, Extraction and Uses of Pineapple Leaf Fiber