Types of Fabric Losses:
The fabric cost is the most dominant one and it is the first priority of the cut order plan. Science about 70% of the garment cost is represented by the cost of the fabric. In order to reduce the fabric wastage, it is necessary to classify the various kinds of fabric wastes that occur during garment manufacturing and then segregate them into essential and nonessential ones and, finally, develop ways to minimize or eliminate the wastes.
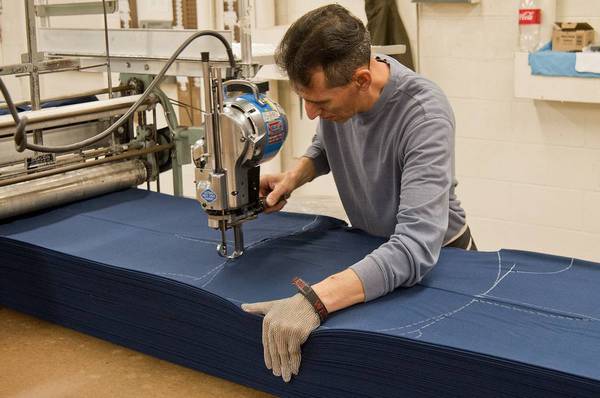
Fabric losses in the garment manufacturing process can have a significant impact on production costs, efficiency, and environmental sustainability. Reducing fabric losses is a key goal for manufacturers.
Let’s consider how to make the most efficient cut order plan when a garment factory receives an order. The optimal cut planning should minimize fabric wastage, minimize fabric cost, and minimize time and labor.
The types of fabric wastes are given below:
1. End loss:
It is an extra fabric left at the ends of a ply in a spread to ease cutting. The standard end loss per ply is 24 cm.
2. Fabric joint loss:
Fabric rolls are stitched jointly while going to the manufacturing processes. This results in fabric wastage of the areas having stitch holes or marks. It is known as fabric joint loss.
3. Edge loss:
The width of the marker is always a few centimeters lesser than the width of the fabric roll. This has been considered to accommodate the selvedge of fabric. The loss of fabric on the sides for selvedge accommodation is called edge loss.
4. Splicing loss:
Cutting of fabric cross ways along the fabric width and overlapping fabric layers in between the two ends of a lay is known as splicing. The splicing operation could be used for adjustment of fabric fault, which has been observed during the spreading operation. The length of overlapped fabric during the splicing operation is known as splicing loss.
5. Remnant loss:
It is the remnant fabric left after the complete laying of a single fabric roll is thrown aside or used for part change. More precise fabric roll allocation methods are necessary to reduce the remnant loss.
6. Ticket length loss:
Normally, the actual fabric length and the length mentioned in the fabric roll will not be the same. The variation between these two lengths is known as ticket length loss.
7. Stickering loss:
Sometimes the patterns are cut a little extra for pattern marking and stickering and this area may get damaged because of glue or ink. It has to be cut off and is wasted.
8. Cutting edge loss:
It is a minor loss due to uneven and faulty cutting during fabric spreading and cutting. This is caused by faulty cutting methods or faulty cutting machinery.
Remedial Measures to Reduce Fabric Loss:
1. End Loss:
- Standardization of end loss in fabric: The end loss of fabric for one particular spread/lay should be standardized and kept as a minimum value as per the requirement of the spread. The standard end loss set for straight knife cutting of garment panels is around 2 cm.
- Minimizing the number of plies in a lay: To reduce the overall end loss of fabric, the number of plies in a lay should be reduced. The minimum number of plies required for a particular order could be determined by
Minimum number of plies,
……………………………Total Order Quantity
= ———————————————————————————————
….Maximum number of pattern Pieces Allowed in one marker
2. Edge Loss:
- Markers in cuttable width: The fabric loss at the width of the fabric could be lessened by preparing the markers whose width is equal to the minimum width (cuttable width) of the fabric.
- Fabric grouping: If more variation in width between as well as within the fabric roll is noticed, grouping of fabrics having similar widths could be tried to reduce the edge loss.
3. End Bits:
- Roll allocation: Generally, the fabric rolls are picked at random and are spread during the spreading process, which leads to enormous amounts of fabric end bits after the completion of spreading of particular lays. Association of fabric rolls with lays should be done in a manner that minimum end bits are left.
- Planning of fabric end bit: Consideration of fabric end bits during the planning of the spread could minimize the end bits.
4. Ticket Length Loss:
- Complete inspection of fabric rolls: This ensures no surprises on the cutting floor and effective fabric control.
- Vendor management: Fabric received in the factory should be tracked vendor-wise. Vendor-wise tracking enables the management to tab the vendors giving less fabric and make informed decisions for the future.
Conclusion:
Reducing fabric losses requires a combination of strategic planning, technology utilization, skilled labor, and continuous improvement efforts. By implementing these practices, garment manufacturers can achieve better fabric utilization, lower production costs, and contribute to a more sustainable production process.
References:
- Apparel Manufacturing Technology by T. Karthik, P. Ganesan, and D. Gopalakrishnan
- CHARLOTTE JACOBS-BLECHA , JANE C. AMMONS , AVRIL SCHUTTE & TERRI SMITH (1998) Cut order planning for apparel manufacturing, IIE TRANSACTIONS, 30:1, 79-90, DOI: 10.1080/07408179808966439
- Practice of Garments Merchandising and Management by Engr. Md. Faruk Hosen
- Garments and Technology by M. A. Kashem