Silk Degumming Process:
The process of eliminating sericin or gum from raw silk is known as degumming of silk. The raw silk consists of 70–80% fibroin and 20–28% of sericin. The main objective of silk degumming process is to impart soft handle and lustre to silk by removing sericin, any impurities picked up during reeling throwing etc. Sericin is the important element of silk. You can see chemical composition of silk below section. Degumming can be carried out on yarn or fabric, in manually or mechanically operated machines. Mechanisms of degumming remain to be investigated.
Raw silk does not possess the luster and softness for which this fiber is known. The gummy substance called sericin (about 20%–25% in mulberry silk and about 15% in wild silk) covering the fibrous material, fibroin, imparts a harsh handle and must be removed in order to bring out the supple and lustrous qualities. Although sericin and fibroin, the two components of raw silk are both proteins, they differ considerably in their relative compositions of various amino acids and accessibility. Degumming also removes accompanying substances such as fats, oils, natural pigments, and mineral components. The thorough and uniform removal of these impurities are important not only for uniform dyeing, but also particularly for good printing results. The process for removal of sericin is known as degumming, boiling off, and less commonly scouring.
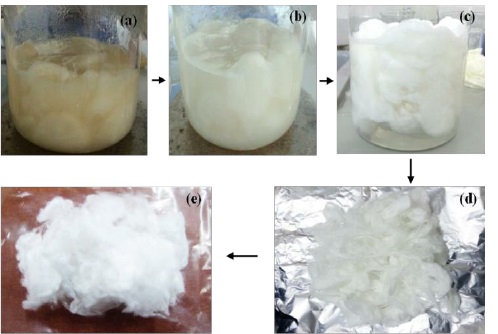
Objectives of Silk Degumming Process:
We already know that the main purpose of degumming process is to remove sericin from silk. Without this below reasons for doing silk degumming.
- Improves dye absorption: Degumming allows for better dye penetration, resulting in a more vibrant and evenly colored fabric.
- Enhances luster: Removing the sericin from silk fibre enhances their natural luster, giving the fabric a glossy and luxurious appearance.
- Softens the fabric: Sericin can cause silk fibers to feel stiff and rough to the touch, and removing it through degumming can result in a softer and more comfortable fabric.
- Allows for better handling and processing of the silk fibres: Silk fibres that have been degummed are easier to handle and process, making them more suitable for use in various textile applications.
- Reduces allergic reactions: Sericin can cause allergic reactions in some people, and removing it through degumming can make silk products safer for those with sensitivities.
- Increases durability: Silk fibers that have been degummed are more resistant to damage and wear, resulting in a more durable fabric that can withstand repeated use and washing.
- Improves the quality of the finished product: After all, degumming is an important step in silk production, as it helps to ensure a high-quality finished product.
Chemical Composition of Silk Fiber:
The composition of raw silk is as follows:
- Fibroin: 70-80%
- Sericin: 20-305
- Waxy matter: 0.4-0.8%
- Carbohydrates: 1.2-1.65
- Inorganic matter: 0.7%
- Pigment: 0.2%
Silk Degumming Methods:
Degumming mainly involves the removal of sericin from the fibroin. It is synonymous with the scouring process used for the purification of cotton and wool. Sericin is insoluble in cold water but is comparatively easily hydrolysed, which breaks down the long protein molecules into smaller fragments easily dispersed or solubilized in hot water. There are some methods of degumming of silk. Following are the main degumming processes:
- Extraction with water.
- Boil-off in soap.
- Degumming with alkalies.
- Degumming with acids.
- Degumming with enzymes.
- Degumming with organic amines.
The conventional working method for degumming or boiling off mulberry silk is as follows:
- Soaking overnight or for 6 h in a bath with 3–5 g/L Marseilles soap and 1–2 g/L wetting agent.
- Boiling off for 2–6 h at 90°C−95°C in a bath containing 8–10 g/L Marseilles soap at pH 9.5 with soda ash.
- Repeat the treatment in a second bath similar to the first one for 2 h, if necessary.
- Rinsing first at 50°C with ammonia and then followed by two rinsing, one at 40°C and another at room temperature.
A rapid method of degumming with soap is to treat for 1–2 h at 90°C–95°C at pH 9.5–10 in the following bath:
- 8–10 g/L Marseilles soap
- 1–2 g/L wetting agent
- 1 g/L soda ash
- 1 g/L sodium tripolyphosphate.
The wild silk (e.g., Tussah or Tussar) requires an initial scouring in a liquor: material ratio of 30:1 (minimum) and 10% (by weight of silk) soda ash.
References:
- Textile and Clothing Design Technology Edited by Tom Cassidy and Parikshit Goswami
- Silk: Processing, Properties and Applications By K. Murugesh Babu
- Advances in Silk Research By Dr. N. Gokarneshan
- Handbook of Textile and Industrial Dyeing, Volume 1: Principles, Processes and Types of Dyes Edited by M. Clark
- Different Methods of Degumming of Silk, https://textilelearner.net/silk-degumming-process/
- http://nptel.ac.in
You may also like: Application of Enzymes in Textile Chemical Processing