What is Carding in Spinning?
Carding is considered as the heart of the spinning process. Carding is a mechanical action of reducing tufts of entangled fibers into a continuous web of individual fibers suitable for subsequent processing. The disentangling of fiber tufts facilitates effective trash removal. This is achieved by passing the fibers between closely spaced surfaces clothed with opposing sharp points. The carding process has a major impact on the final product, that is, yarn, in terms of uniformity, imperfections, and cleanliness. Carding machine individualizes the lumps of fibers that results disentangling of tufts in the “opening-and-picking” stage of primary processing and simultaneously removes impurities, neps, and short fibers, improving the orientation of fibers in the longitudinal direction and producing card sliver.
Background of Carding Machine:
In 1748 Lewis Paul of Birmingham, England invented the hand driven carding machine. The name card is derived from the latin “Carduus. It means thistle, the spiked fruit of which was used for plucking fiberd apart in earlier time.
The proverbs of experts,
- “The card is the heart of the spinning mill”
- ‘Well-carded is half-demonstrate the immense significance of carding for the final result of the spinning operation.
These proverbs demonstrate the immense significance of carding for the final result of the spinning operation. The importance of carding is still greater where new spinning systems are concerned. The considerable influence of the card on yarn quality arises from the very complex series of events in the process itself, and also from the pressure to adopt an extremely high production rate on economic ground.
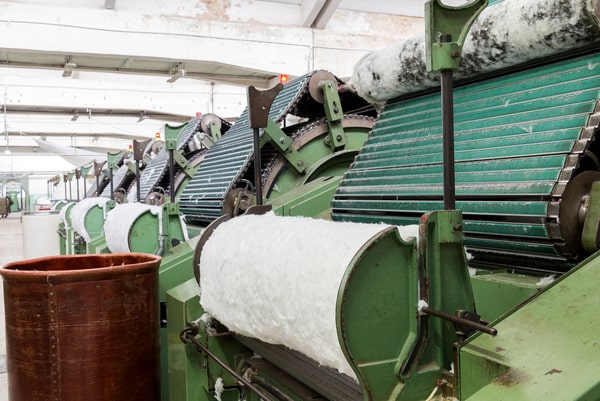
Carding is defined s the reduction of entangled mass of fibers to filmy web by working them between two closely spaced relatively moving surfaces clothed with sharp points. It is a preliminary process in spun yarn technology just after blow room process.
New Development in Carding Machine:
In previous discussed that on 1748 Lewis Paul of Birmingham, England invented the hand driven carding machine. This carding machine has been added many values and developed for the requirement of spinners.
The most recent developments are given below:
- Higher production rate up to 250 kg/hour
- Direct feeding system FBK: Chute feed
- Feed rate control system: CFD (CORRECTA FEED)
- Multiple licker-in system: 3 Licker-in
- Precision Flat Setting System PFS
- Precision Mote Knife Setting System PMS
- Aluminum flats without bolted connection
- Computer control with Touch Screen
- Electronic Flat Measuring System FLATCONTROL TC-NCT
- ON-line nep counting with NEPCONTROL TCC-NCT
- Waste quality measuring with WASTECONTROL TC-WCT
- Digitally controlled, maintenance-free servodrives
- Integrated Carding Grinding system:
- IGS Tops
- IGS Clssic
- Magnetic flat bar: MAGNA TOP
- Integrated and continuous suction system
- Larger can size: 1000X1200 mm
- Roller doffing system
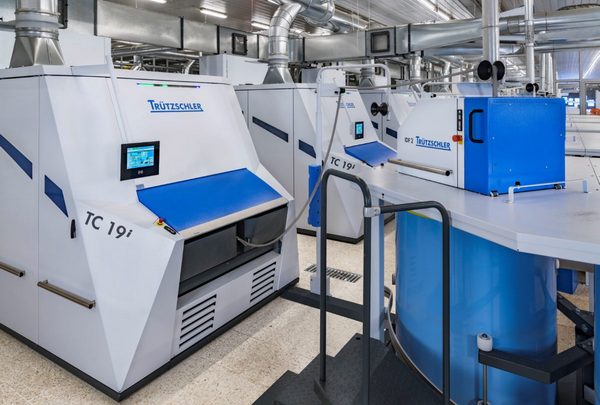
Grinding and Its Importance:
There are three areas in any carding machine. These are:
- Opening and Cleaning area
- Carding area
- Sliver formation
The main segments of carding machine are covered by card clothing. These metal cloth with sharp wire. The wire looses its sharpness due to metal to metal or metal to fiber friction. That’s why it needs re-sharpening. The process re- sharpening, he car clothing wire is called grinding.
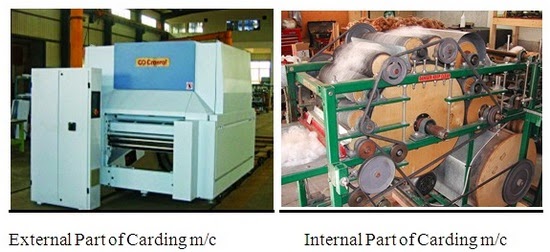
The performance of card clothing reduces continuously with the processing of materials. The operating life of clothing expressed in terms of the total throughput or material. For the cylinder it normally lies between 300 tons to 600 tons. But it can be higher for some circumstances. The amount of fiber, type of fiber etc. could be the reason. Processing of fibers strongly wears down the teeth-they become rounded of the sliver. The points must therefore be sharpened from time to time, in order to give a better shape to the edges by grinding them. Each grinding operation reduces the number of neps, but the level nerve returns to that prior to the preceding grind. The deterioration in quality from one grinding interval to the nest arises from the fact that the teeth are ground down to successively lower heights, the land at the teet points become stadily larger, and softer metal layers are gradually exposed.
You may also like: Basics of Textile Fibers
The interval is best selected in dependence upon the nep limit. The doffer clothing works much less than that of the cylinder works. That’s why it should be ground less frequently except when synthetic fibers are being processed. The clothing on the Taker- in should not be ground. It should be renewed after a throughput of 100 tons to 200 tons.
The grinding tools:
There are types of grinding tools are commonly in use. These are:
- The full-width grinding roller
- The traversing grinding disc
Developments in licker-in section of carding machine:
Automation, higher production and improved quality of the products are the requisite of any recent developments.
Chute feeding is a recent development in feeding small tufts of cotton fibers directly from blow room to a series of cards, arranged in a circuit through ducts and chutes.
Already we have seen the working of chute feeding system in a third unit.
In this unit, we shall discuss some other developments in licker-in section of carding one by one in the following pages.
The objects of major developments in licker in section that have taken place are
- To improve the opening of tuft at high rate of feed in H. P card.
- To distribute the tufts as evenly as possible on the cylinder.
- To extract the maximum trash with minimum loss of spinnable fibers.
Following are the developments that have taken place in the licker-in section.
- Card analyzer
- Development in place of mote knife
- Shirley modification.
- Fiber retriever.
Card Analyzer or Uni Opener:
- M/S. Nagoya a leading card clothing manufacturer of Japan has offered an evener roller under the trade name of card Analyzer. This may also be called as uniopener.
- As shown in fig, this evener roller is placed above the licker in. It opens the large unopened tufts released by the licker-in and also remove the excess fibers on the cylinder which is returned to the feed roller again through a space provided between the taker-in and its cover.
- Thus, it helps to feed the tufts as evenly as possible on the cylinder. It is claimed that the neps formation and the waste are reduced.
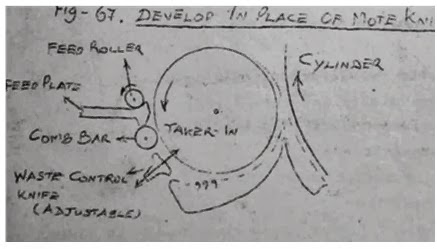
Development in Place of Mote Knife:
- M/S. Mafatlal Engineering has introduced comb bar and wast control knife attachment in their super card in place of mot knives, as shown in fig.
- The arrangement consists of a small diameter cylinder clothed with coarse pitch wire. It replaces conventional mote knives when processing cotton and is positioned directly under the feed plate nose so that the material feed is immediately subjected to carding action.
- This opens the cotton and gives high trash yield by permitting the trash to separate from the main stream of fiber in the large free space following the comb bar.
Shirley Modification:
The essential changes in the cleaning region are: 1. The replacement of conventional mote knives by a deflector plate which is provided under side of the feed plate.
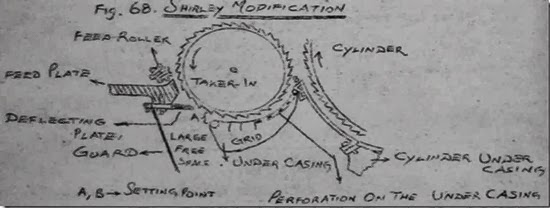
The taker-in grid is replaced by a shorter grid usually 7″ long, incorporating 3 bars and the normal perforations. & The Setting between grid and taker-in is made wider than the conventional card.
A safety guard is fitted under the feed plate to cover the exposed portion of the taker-in.
For short staple cotton 8″ grid is usually suitable, for medium 7″ grid and for long staple cotton 6″ grid may be employed.
Advantages of Shirley Modification:
- The amount of trash passed on to the cylinder was 31% less than normal resulted in cleaner sliver.
- The dust generated during carding -is reduced.
- The life of the metallic clothing is increased due to less trash on cylinder.
- Increases the trash extraction of 10% with 24% less lint loss than conventional card.
Fiber Retriever:
This arrangement reduces the loss of spendable fibers.
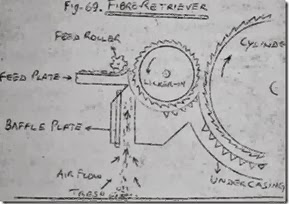
The nose of the fiber retriever deflects the heavier trash particles, downwards away from the licker-in.
Air drawn in by the fast-rotating licker-in is channelled between the buffle plates of fiber retriever, so that the trash particles fall downwards in the up current of air, which detaches any spinnable fiber entangled with the trash particles and carries the good fibers back to the licker-in.
It is claimed that as much as 1 % waste is reduced.
Dust extraction systems in carding:
The high-pressure area in the card-at the junction between cylinder and flats at taken-in end-causes ejection of dust over top of the back plate and between the flats.
Another high-pressure area- at the junction between the main cylinder and doffer -leads to ejection of dusty air over the doffer.
Doffer comb produces air turbulences, which causes dust to rise and at the calender roller the air that is mixed with the cotton in the web is squeezed out, together with dust and fly.
Air escaping into the atmosphere from the high-pressure zone carries dust with it and is responsible for most of the dust in the card room.
Modern HP cards are equipped with the dust and fly collector such as shirley pressure point system for extracting the dust, fly and fibers which are collected in a special chamber without rendering unhygienic the atmosphere in the card room.
This has low running cost and useful
- To prevent the ejection of dust by suitably covering the regions of the machine where the dust is liberated.
- To move the dust from several forces to a central region from which it can be conveniently removed.
An Exhaust fan, through suitable hoods fitted to critical regions of the card draw off air with fly and dust and after separating these from air, pure air is returned to the department.
The dust passing through the slits between the flats is retained (and then exhausted) by a flexible metal sheet across the full width of flats and placed inside the flat chain to cover about 2/3 of the flats.
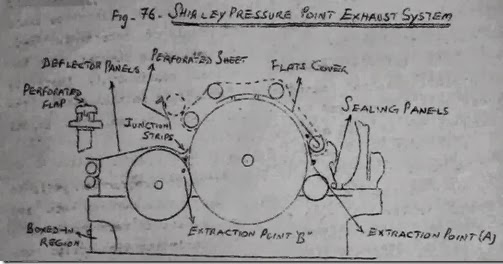
The region where flats take position on the bend is also boxed in and exhausted.
A deflector shield is fitted over the doffer comb and extends forward to the calender roller and the region under the calender roll is boxed in to collect the fly that falls from the underside of web.
A screen of perforated metal is fixed in front of the flat cleaning brush to catch any fly released there, and a similar screen is fitted on the coiler where the sliver turns through a right angle to proceed to the can.
The complete shirley pressure point system reduces the dust load in the card room atmosphere by about 90%.
Following are the improved waste removal system of latest high production carding,
Internal suction system:
The integral fan for internal suction creates a vacuum with in the outer shell. Thus, no dust from the card escapes into. the workroom. the suction is very effective in the removal or fly waste, dust and micro dust which are released during carding. Dust and wastes are removed at all points of occurrence, feed, flat entry, flar strips, web delivery and waste chamber under the card. The internal suction operates continuously there by maintaining constant auto dymanic conditions in the card.
The exhaust air is conveyed to air conditioning system. The amount of exhaust air is 2300 m3/h per card. Under card waste removal system. The under-card waste is transferred by programmed periodic blasts of compressed air into the vicinity of a suction hood and collected in the rear most filter of the two filters built into the outer shell. The over card wastes including flat strips are collected in the foremost filter. The intermittently acting central suction system programmed to empty first the foremost filter and then the rear most filter.
The card can be connected to a continuously acting suction system in which case there is no need for fan and filters. manual cleaning of filter is necessary in the absence of central suction system.
Conclusion:
Carding is the process of arranging the fiber in parallel fusion. This is necessary for all staple fiber. Otherwise it would be impossible to produce fine yarn. Before the raw stock can be made into yarn, the remaining impurities must be removed. The fiber must be in different angle and they must be straight turned. The card is the hard of the spinning mill and well carded is half spun. Demonstrated the immersed significance of carding for the final of opening operation.
You may also like:
- Basics of Textile Fibers
- Applications and Impacts of Automation in Fiber and Yarn Manufacturing
- List of Top 10 Yarn Manufacturers and Exporters in Bangladesh
- Comber Machine Production Calculation