Conductive Textiles:
The textile structures which can conduct electricity are called conductive textiles. It may be either made using conductive fibres or by depositing conductive layers onto non-conductive textiles.
A conductive fabric can conduct electricity and made with metal strands woven into the construction of the textile. It can be inhibited the static charge generated on fabric, to avoid uncomfortable feelings and electrical shocks also.
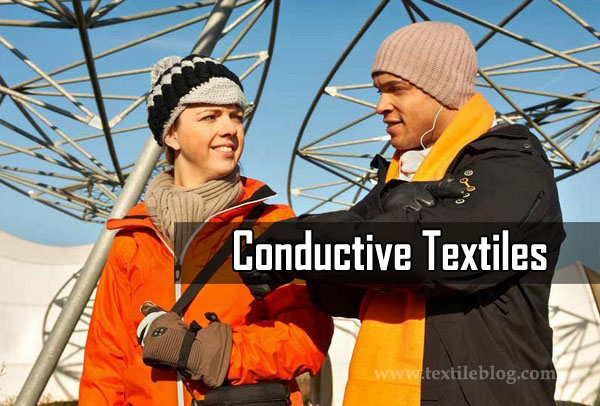
Methods of producing conductive textiles are summarized as follows:
- Adding carbon or metals in different forms such as wires, fibres or particles.
- Using inherently conductive polymers.
- Coating with conductive substances.
Types of Conductive Textiles:
Generally, four kinds of conductive textile as follow:
- Anti-static textiles
- EM shielding textiles
- E-textiles
- Functional coatings
1. Anti-static textiles:
Static electricity can the build-up of electric charge on the surface of objects. Which can be caused many problems for textile materials, manufacturing and handling the product. In dry textile process, fibres and fabrics can tend to generate electro-static charges from friction. When fibres and fabrics are moving at high speeds on different surfaces, (like: conveyer belts, transport bands, driving cords, etc) causing fibres and yarns to repel each other. These static charges can be produced electrical shocks and caused the ignition of flammable substances. Two techniques are known to prevent static electricity in textiles. One is to create a conducting surface and another is to produce a hydrophilic surface. In these ways antistatic textiles are produced to avoid the potential hazards caused by static charge or, electricity.
2. EM shielding:
Electro Magnetic shielding (EMs) is the process of restricting the diffusion of electromagnetic fields into a space. In this process, electrically or magnetically conductive barrier is used. Shielding is common technique for protecting electrical equipment and human beings from the radiating electro-magnetic fields. This barrier can be rigid or flexible. When an EM beam passes through an object, the electro-magnetic beam interacts with molecules of the object and this interaction may take place as absorption, reflection, polarization, refraction, diffraction through the object. EM Shielding textiles materials can be found in the form of woven, knitted, and nonwoven fabric also. The major components of these fabrics are fibres and yarns. To achieve an effective shielding behaviour, these fibres should be electrically conductive. Conductive yarns can be made by blending conductive fibres with conventional staple fibres, twisting conductive or insulator filaments together. For example, conductive metallic yarn (such as: silver, copper, etc.) can be wrapped with insulating textile materials to create hybrid yarns. Which could be integrated into woven or knitted structures. Hybrid yarns or metallic fibre can be integrated into these designs as warp. Electromagnetic shielding effectiveness of the fabric decreased with the increase in fabric openness.
3. E-textiles:
Electrically conductive fibres and yarns have attracted great interest because of their distinguished features including reasonable electrical conductivity, flexibility, electrostatic discharge, and EM interference protection. Conductive textile fibres are the primary component for wearable smart textiles introduced particularly for different applications such as sensors, electromagnetic interference shielding, electrostatic discharge, and data transfer in clothing. Therefore, the demand for electrically conductive fibres and yarns is ever-growing. The development of novel conductive fibres becomes crucial with technological improvement in wearable electronics such as wearable displays, solar cells, actuators, data managing devices, and biomedical sensors. E-textiles play a critical role in selecting the conductivity of smart textile electronics. Textile applications such as lighting, considerable current is necessary and low ohmic fibres are preferred. On another hand, for certain sensing or heating applications lower conductivity would work better. So, it requires fibres exhibiting lower electrical conductivity. E-textiles need flexible and mechanically stable conducting materials to ensure electronic capabilities in apparel.
4. Functional coatings:
For many applications, functional coating is the material interfaces and surfaces that provide beneficial functionality over their intrinsic bulk characteristics. Hence, coatings provide a versatile method of modifying textiles with conductive properties. Subsequently, the textile fabric acts as a supporting structure or carrier material for the conductive finish. Conventional methods such as dip coating or roll coating are typically used to apply bulk coatings in the form of a saturation or lamination that covers the entire “surface” of the textile. However, as will be presented herein, the advent of nano-technology in textile research, the development of novel process techniques, and the advancement of inks and coating formulations affords the opportunity to apply coatings to increasingly finer structures.
Properties of Conductive Textiles:
Physical properties:
- Low weight,
- High strength,
- Flexibility,
- Durability,
- Elasticity,
- Heat insulation,
- Water absorbency,
- Dyeability,
- Drape,
- Soft handling,
- Wash ability, etc
Electrical properties:
Electrical properties | Variants of yarns | ||||
CY1 | CY2 | CY3 | CY4 | CY5 | |
Electrical resistance,[kΩ] | 36.384 | 563.4 | 75.5 | 0.2682 | 0.1422 |
Diameter of yarn, [mm] | 0.8352 | 0.2645 | 0.3897 | 0.5845 | 0.4256 |
Electric resistivity, [Ω∙m] | 0.1992 | 0.3094 | 0.0900 | 0.2365 | 0.2559 |
Note: In the case of yarns from staple fibres, respectively CY1, CY2 and CY4 and yarns from continuous fibres respectively CY3 and CY5.
Tensile properties:
Tensile properties | Variants of yarns | |||||||||
Y1 | CY1 | Y2 | CY2 | Y3 | CY3 | Y4 | CY4 | Y5 | CY5 | |
Breaking strength, [cN] | 856 | 1002 | 318.8 | 389.8 | 1006 | 929 | 382.9 | 458.5 | 1507 | 1224 |
Coefficient of variation of strength, [%] | 7.04 | 8.79 | 8.34 | 9.87 | 2.24 | 4.51 | 7.72 | 9.82 | 2.01 | 3.98 |
Breaking elongation, [%] | 22.72 | 28.96 | 13 | 10.15 | 35.64 | 35.5 | 11.01 | 7.02 | 29.25 | 55.8 |
Breaking tenacity, [cN/tex] | 11.57 | 2.17 | 12.31 | 4.41 | 28.77 | 7.05 | 9.70 | 2.71 | 46.19 | 7.96 |
Coefficient of variation of tenacity, [%] | 5.07 | 11.50 | 3.55 | 12.94
| 1.86 | 14.17 | 8.70 | 26.76
| 2.66 | 24.30
|
Application of Conductive Textiles:
Growing awareness about the superior functionality and typical application of conductive textiles include anti-static textiles, electromagnetic shielding (EMs), and e-textiles for flexible electronics has led to the rising adoption of the smart textiles and related products across varied end-use industries.
The increasing awareness about the functionalities and benefits regarding of the application of conductive textiles in smart textiles globally has boosted the demand.
Major application areas of conductive textiles:
- Military & defence
- Healthcare
- Consumer electronics
- Sports & fitness
- Smart clothing
- Transport of electrical signals
- Heating
- Protection from electromagnetic interference and electrostatic discharge
- Others
Some applications are described below.
1. Military & Defence:
Textiles for in military uniforms required to provide extra durability, safety, and protection in hostile environments, damage resistance, and also comfort. Conductive textiles are lightweight, flexible, and provide high strength and superior conductivity. It provides a soldier requires protection against extreme weather conditions (like: heat, cold, wind, and rain), sweat management, integration of high-tech materials ballistic impact, nuclear, biological or chemical threats, etc. That’s why it’s rapidly adopted across the defence segment. The defence segment is the largest user of conductive textiles all over the world. Additionally, these conductive textiles also find applications in military parachutes, safety harnesses, ropes and tenting gears.
You may also like: Defense Textile: A New Export Opportunity for Bangladesh
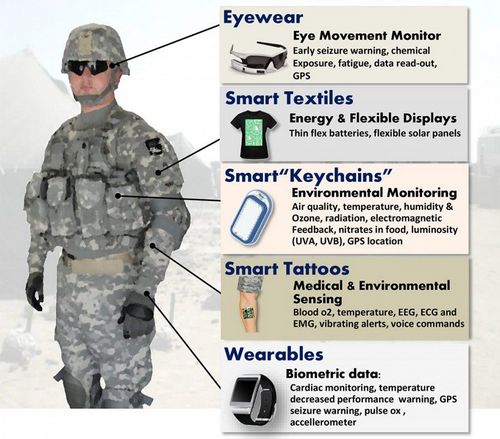
2. Healthcare:
In medical sector, conductive textiles are used for both clinical and non-clinical applications. It’s designed to provide comfort and functionality at the same time. The conductive textiles product helps doctor or medical staff to monitor and communicate conditions of a patients, as it can detect, acquire, and transmit physiological signals.
You may also like: Application of Smart Textiles in Medical and Healthcare
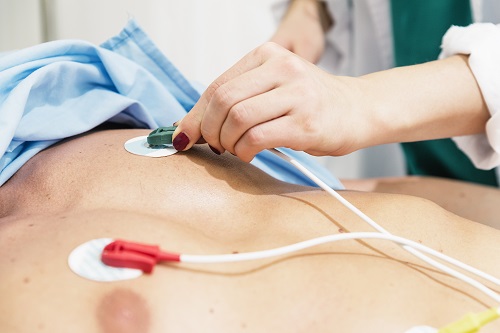
3. Consumer Electronics:
Conductive textiles are used in products such as smart watches, augmented reality headsets, multimedia players with computing facilities, and smart goggles. It helps small, thin, light, and reliable product developments.
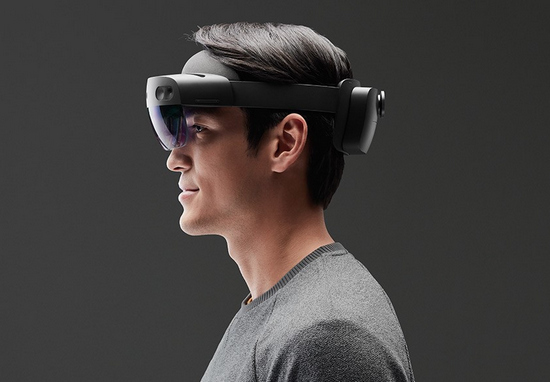
4. Sports & Fitness:
Conductive textiles are used in the sports and fitness sector to monitor sleep, calories consumed, heart rate, blood pressure, etc. Increasing the health awareness among younger’s, led to a high demand for conductive textile. In many smart fitness products, heart rate can be monitored by measuring the electric impulses that the brain uses to control the heart muscle. That can be achieved using an electro conductive fabric that is placed close to the heart.
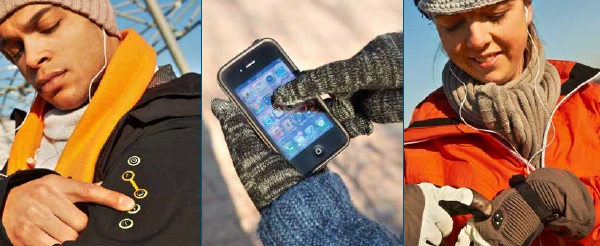
Conclusion:
Conductive textiles are widely used in smart textile applications such as sensors, communication, heating textiles, electrostatic discharge clothing and so on. It became popular during the last decade. Conductive textile has played a vital role in this fast-growing smart textile market since 2015. So, we should have to more and more research on conductive textiles and also smart textile product development.
References:
- Engineering of High-Performance Textiles Edited by Menghe Miao and John H. Xin
- Conductive textiles by K. (Kelvin) Fu, R. Padbury, O. Toprakci, M. Dirican, X. Zhang North Carolina State University, Raleigh, NC, United States
- Industria Textila˘2019, vol. 70, nr. 2
- Analysis of tensile properties for conductive textile yarns by Liliana Buhu, Emil Constantin, Loghin, Daniela Negru, Adrian Buhu
- https://www.technicaltextile.net/articles/printarticle/3739
- https://en.wikipedia.org/wiki/Conductive_textile
Author of this Article:
Md. Mahedi Hasan
B.Sc. in Textile Engineering
Textile Engineering College, Noakhali.
Email: mh18.bd@gmail.com