What is Natural Fiber Nonwovens?
Nonwoven technologies are useful for the development of novel materials and products in shorter and comparatively faster rate than those attainable in conventional weaving and knitting. Furthermore, nonwoven techniques engineer the final product with superior specific properties. Owing to their specific properties, lower costs of manufacture, nonwovens open up new markets in numerous household, industrial and technical end use applications. Durable applications business is the biggest application region for nonwoven materials and items followed by expendable applications market. Durable applications incorporate home furniture, divider blankets, covering substrates, clothing interlinings, material items and geo-materials. Dispensable applications incorporate grown-up incontinence items, child diapers, expendable wipes, feminine hygiene products, cloths, restorative or surgical items, channels, filters, disposable garments and fabric softener substrates. Additionally, durable applications business sector is the quickest developing business for nonwoven materials and items. Automotive sector is another growing potential for nonwovens.
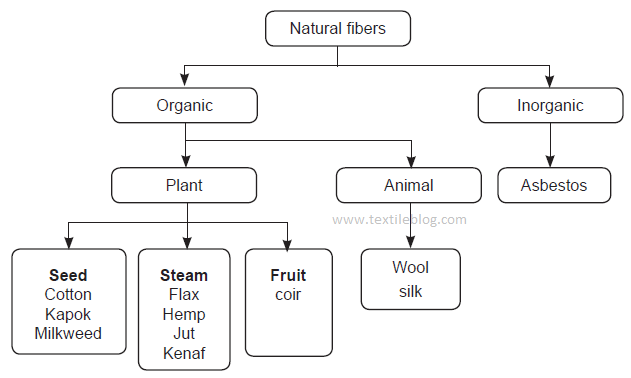
Natural fibers such as cotton, wool, jute, flax, hemp etc. become the fiber of choice for manufacturing various nonwoven fabrics. (Figure-1 represents the classifications of natural fibers from different origins) Their biodegradation properties make them more and more appealing in the context of new regulations for environment protection. The natural fiber nonwovens are becoming the fastest growing sectors occupying technical textile market around all over the world. Some chemical modification are required to natural bast fiber such as jute, flax etc. to make them to feel softer in nonwoven form which is a demand in many applications. Cotton fiber nonwovens are occupying the market of hygiene and healthcare sector more prominently while jute nonwovens are found more suitable positions in the field of applications of filtration, geotextiles, automobile interiors, household products, composite reinforcements and other appliances. Flax and hemp nonwovens are used suitably for reinforcing application in composites, geotextiles, mats, panels etc. All these nonwovens have tremendous potential for various other functional application such as for insulation from heat and sound, sea water oil sorption, metal ion removal from wastewater and many more.
Application of Natural Fiber Nonwovens
1. Application of natural fiber nonwovens in filtration:
The nonwovens have been used as filter media since the birth of nonwoven technology. The performance of nonwoven fabrics in dry and wet filtration is mainly determined by its pore size and its distribution. The selection of the fibers for preparation of filter media is important. The appropriate pore size is a design consideration for filter fabrics for a particular application corresponding to particle size. The micro-pores should be smaller than the minimum particle size to ensure the desired filtration efficiency. This should be achieved with the minimum pressure drop across the filter media and without causing any disturbance to the pore geometry. It is desirable that pore size distribution should be as uniform as possible and that the values at extremities should well controlled. Too small and too large pores than the required average value of the particulates are undesirable.
Needle-punched nonwoven fabrics show superior filtration efficiency with good dust particle separation and dust holding ability. A calendaring process has been found to further increase in filtration efficiency of the fabrics by regulating their density and permeability. Calendaring makes the fibers more tightly packed, thus making it more difficult for particles to pass through the filter fabric. With the increase in consolidation, the fabric density increases with the resultant increase in dust arrestance and holding capacity without increase in pressure drop. Jute needle punched nonwovens are suitable for coarse and medium filtration application and suitable for textile, tobacco dust, wood flour, paper shreds etc. Nonwoven mats made of biodegradable, natural fibers of flax and cotton are used for remediation of a ubiquitous pollutant of water and wastewater, namely, copper ion. The nonwoven mats were treated with citric acid in order to enhance the amount of negative charge on the mats and improve their ability to sequester copper ion. Treated flax fiber mats and flax or cotton fiber mats represent a potentially fast and convenient method for removal of metal ions from water and wastewater streams. Different hemp-based mono-layer and composite nonwovens are prepared to study the oil filtration properties. The Reynolds number of hemp/cotton spunlace nonwoven at different fluxes is small (Re < 1), which decreases as the increasing of filtration area while increases as the increasing of flux at the state of laminar flow.
Hemp or cotton spunlace nonwoven, hemp or viscose spunlace nonwoven, hemp or viscose spunlaced nonwoven etc. are impregnated with polyacrylic adhesive to prepare composites. Those composites are explored for filtration application in practical application.
2. Applications in medical textiles:
Spunlace cotton nonwovens are extensively used in various medical and healthcare application. Tencel or Cotton Nonwoven Fabric Coated with Chitosan was explored for Wound Dressing. The flax fiber cloth used in medical purpose like cancer and wound healing etc. Air-laid and we-laid nonwoven structure made of flax fibers and its blends could be used as disposables in medical use. As An antimicrobial material flax fibers coated with silver nanoparticles could be of interest not only in fabrication of sanitary and medical articles, but also industrial materials. Manufacturing of medicinal products, health care apparels, and cosmetology aids is becoming one of the most developing segments in the global market of nonwovens production in near future.
You may also like: Importance of Medical Textiles in Infection Prevention and Control
3. Applications in automotive textiles:
Jute and flax nonwovens are recently used extensively in automotive industries. The reasons influencing the steady growth of use of these nonwovens in this sector are many. Comparative weight reduction of 10–30% in automobile parts can be achieved in addition of good mechanical properties. Composite structure can be formed in a single machine passage with relatively good impact performance, with high stability and minimal splintering. The nonwoven end products are having no health hazard during handling or use, no emissions of toxic fumes when subject to heat. The sustainable and renewable raw material resource and superior environmental balance during material and energetic use, recycling possibilities and relative cost advantages make them attractive alternative to synthetic fiber nonwovens.
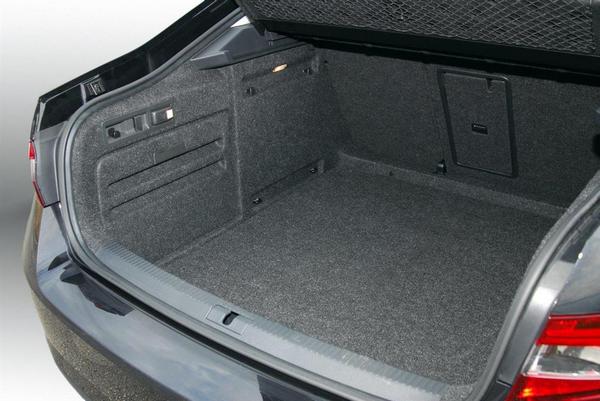
Researchers found that the flax/polypropylene nonwoven prepared by spunlacing are suitable auto interiors with particular technical merits of enhancing tensile and flexural strengths, reducing thickness with controlled ultimate weight, increasing noise absorption coefficient and transmission loss and improving nonwoven moldability and fogging performance. Compared with glass fiber, flax has significantly lower density, thereby enabling a lighter-weight composite that offers comparable performance. This is key for the automotive industry, where it is used for sound absorption, strengthening and structural reinforcement. Door panels of Opel Vectra are now made of flax-based nonwovens. All BMW and Mercedes models now use natural fiber nonwoven composites for door liners, boot liners and parcel shelves. There are now making more sophisticated modifications like blending of flax with extra strong sisal fibers for strengthening or and lightweight headliner and rest of the automobile body. Present market is remarkably open to approach from new nonwoven suppliers, and equally open–minded in respect of which fiber they may consider using flax, hemp or jute.
4. Applications for thermal insulation:
Jute and flax needlepunched nonwoven can be used for effective thermal insulation. Thick and porous needlepunched structure contains evenly dispersed void or air pockets which provide thermal insulation. Also, inherent thermal conductivity of jute and flax is very poor. Woollenization of jute fiber improves the bulk of the nonwoven structure which improves thermal insulation further. In addition to industrial uses these nonwoven fabrics can be used as filler of warm garment like jackets. The thermal conductivity (λ) of air-laid flax nonwoven of 10 mm thickness is evaluated using one sample panel apparatus for evaluation of materials for building industry.
5. Applications for acoustic insulation:
Nonwoven fabrics of ideal materials are used as acoustical insulation products because they have high total surface area. The nonwoven composites consists of cotton fibre with three surface layers (glass fiber, cotton and activated carbon fiber) are explored for their acoustic properties. The nonwoven composites with cotton as a surface layer has significantly higher sound absorption coefficients than the glass fiber layered composites. It is also found that carbonization and activation of the cotton nonwoven further improves sound absorption ability. The effect of blend proportion of cotton, kapok and milkweed fibers with cotton, fabric GSM, bulk density and distance of fabric from sound source on sound reduction of needlepunched nonwoven fabrics is investigated. A nonwoven fabric of cotton/milkweed 40/60 shows the highest sound reduction potential. For acoustic absorption in car interiors floor coverings are made of nonwovens fabrics using natural fiber (kenaf, jute, waste cotton, and flax) and their blends with polypropylene and polyester fibers.
6. Application in nonwoven composites:
Recently, vegetable fibers such as jute, flax, pineapple fiber, hemp etc. have been increasingly used as reinforcement in polymer composites. Due to the low cost and good mechanical properties these natural fibers aided with good, renewable and biodegradable resources they are successful alternative to the most common synthetic reinforcement, i.e., glass or carbon fibers. Cotton, jute, flax, hemp, sisal, and broom are the fibers most commonly used fibers and suitable matrix polymers are polyolefins, polystyrene, epoxy resins and unsatured polyesters. In present days, the application areas of these composites are in the automotive sector and include composite parts produced by means of thermo-forming or thermocompression moulding techniques. Needlepunched nonwoven may be a successful reinforcing agent for composites.
Chair, table, wash basin, serving tray, tool box, rain pipe, signal casing, corrugated sheet, speaker box, fan blade, country boat etc. have been successfully prepared from jute needlepunched nonwoven based composite. Jute needlepunched fabrics can be used for decoration, bags, home furnishing, soft luggage, hat, apron, gloves, handicraft items, file cover, sports equipment etc. As a reinforcement layer in tennis racquets spunlaced flax is lightweight and absorbs vibrations. The UV resistance quality and natural wood-like appearance of flax nonwovens make them attractive as construction material for boats and canoes. Other applications include reinforcement in foot bridges, and in wind turbine blades, which provide high strength to weight ratio. Flax nonwoven composites can be used as roofing membranes with hard-wearing, high breathability and long lasting. In this way, it is established as a valuable alternative to synthetically manufactured membranes in the roofing sector.
7. Application in geotextiles:
Now-a-days, properly designed needlepunched nonwovens made of bast fibres are used in erosion control in highway embankment and cut slops, river bank protection, ground separation functions, filtration in road, reinforcement applications in temporary unpaved roads etc. The main advantages of these fibers are their ecofriendliness and renewability. As ecofriendly fibers, jute, flax, hemp etc. have a great compatibility with soil and degrades after few months helping in soil stabilization, cake formation, and vegetation to grow. Though these nonwovens have low strength and biodegradable, they improves the performance of the unpaved road as the soft subgrade attains strength over the time. Presently, application of natural fiber-synthetic blended fabrics may produce a long-term effect in geotextiles. A comparison has been made between the properties of the needlepunched nonwoven geotextiles prepared from polyester fiber and that of flax fibers.
The properties of geotextiles studied are density, pore size and air permeability. Variation in length and diameter of the flax fiber is hound to be the cause of loss of tensile strength of materials. Nevertheless, flax fiber-based geotextiles have a great potential in various civil engineering applications as they are isotropic, compact and permeable to air. Flax nonwoven reinforced cement composites are prepared as sustainable materials for building envelopes. Nonwovens are even explored for water proofing and geotechnical applications. It is found that jute, jute caddies (unspinable jute fibre) in 1:1 proportion suitable for water proofing treatments.
8. Application as floor covering:
Natural fiber nonwovens are successfully explored for reducing automotive interior noise and floor covering. Jute and jute blended needlepunched nonwoven fabric are successfully used as floor covering and carpets. Jute blended needlepunched nonwovens prepared by sandwich blending technique provides both the aesthetic and functional properties for specific applications and are substantially cheaper than commercially available woolen materials. In some cases, woven sacking or hessian fabric is used at the backside for reinforcement of jute based nonwoven fabrics to enhance the mechanical performance and coarse denier polypropylene or acrylic fiber is used on top to bring aesthetic appeal and smooth appearance. Kenaf nonwovens are used as substrates for laminations and explored universally in the manufacture of furniture, kitchen cabinets, fixtures, wall-coverings, displays, and various other products. Nonwoven mats are manufactured from kenaf fibers. Now jute-nonwovens and its composites are used in making of door liners, boot liners parcel shelves etc.
9. Natural fiber nonwovens oil sorbents:
Needlepunched nonwoven fabrics are prepared from cotton, milkweed, kapok fiber, wool, and kenaf fibers and explored for sea water oil sorbents. Except kenaf, oil sorption capacity of these natural sorbents are found much higher than that of polypropylene in a simulated seawater bath. The hydrophobic and scaly surface of wool provides large and readily accessible surface pores for oil adsorption. When wool fiber is present in nonwoven structure the structure itself contributes to easier formation of capillary bridges of oil in fibers interstices. Hence, natural fibre nonwoven structure is one of the best choice where accessible fiber surface area is nearer to loose fibres due to structural openness and the nonwovens can be easily collected after usage.
References:
- Nonwoven Fabric: Manufacturing and Applications by Rembrandt Elise
- Nonwovens: Process, Structure, Properties and Applications by T. Karthik, R. Rathinamoorthy and C. Praba Karan
- Nonwoven Fabrics: Raw Materials, Manufacture, Applications, Characteristics, Testing Processes Edited by Wilhelm Albrecht, Hilmar Fuchs, Walter Kittelmann