One of the most important areas for automation is the dyeing and printing process, as it involves many complex parameters that are very important. If even a small amount of milligram is wrong in the dyeing recipe, the shade of the fabric will change. Different parameters like temperature, pressure, mixing time etc. are very important for dyeing. Dyeing parameters can be controlled very finely using automation. Also, automation has been used in textile finishing for a long time, but over time it is becoming more modern. Automation is notable in machine control systems, robotized systems, color analysis, etc.
Automation in Dyeing
The technology of dyeing process control has evolved relatively rapidly from simple manual operations to stylish computer controlled machines within the past several decades. Dyeing is one of the most complicated process in any textile processing and combines the sciences of fluid mechanics, thermodynamics, chemistry, physical chemistry & others. The earliest systems utilized in the control of batch dyeing machines had electronic devices that were controlled by punched cards. One of the earliest systems was developed by Kilsunds AB in Sweden in 1950s, this used a single time temperature profile for the dyeing of different types of fibers. Bunting in 1968 pointed out that the automation in the dye house was essential.
The Four Main Sections of Dye House Automation System:
- Powder die storage and weighing system [Capacity 25-60 dye box (TBT and Patternostar)]
- Powder Dye Melting and Distribution System [Capacity 50 Cycles/Dye (TBC)]
- Liquid Chemical Distribution System [Capacity 1500 Cycles/Dye (RD96)]
- Powder Chemical Dissolution and Distribution Ion System [Capacity 350 L/min (SLD)]
Computer Control of Dyeing Machinery
The application of computer control within the dyeing industry has grown rapidly during recent decades. Dyeing automation began with the introduction of simple systems that controlled temperature by switching heaters on or off. Subsequently, these were replaced by systems that controlled the dyeing cycle consistent with a time/temperature sequence. The processes of dye and auxiliary addition as well as loading and unloading of the textile materials can also be automated dyehouse management.
Dyeing Machine Automation
The Programmer for Dyeing Machine Automatic Operation is widely accustomed control the speed of rise and fall during the method of thermoregulation. These programmers possess with high accuracy level and are admired for their durable standards and rough or uneven construction. In order to supply a user-friendly programmer, it’s incorporated with various easy to know and operate mechanisms. Being semi-automatic, these programmers also eliminate errors related to manual operations. By installing these programmers one can avoid any kind of uneven dyeing or allied problems.
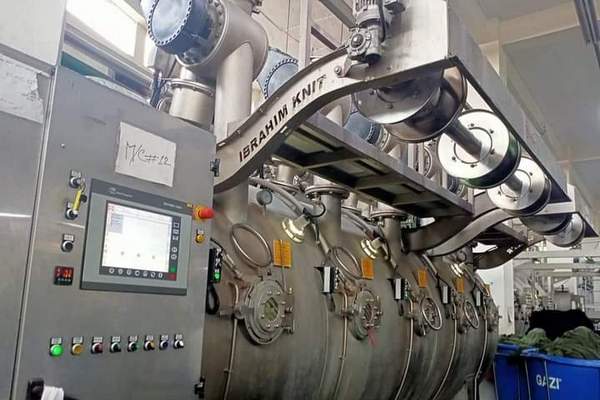
Exclusive Features:
- Time temperature profile for controlling the rate of rise & fall during thermoregulation also hold time.
- Automatic operation of heating, cooling and also increasing or decreasing of pressure.
- Feather touch keypad for simple operation and versatile programming
- 25 recipes with 16 step each are often permanently stored.
- Automation turns on & off the heaters of the dyeing house and controls the temperature of the dyeing bath.
- Automation was adopted as the loading and unloading processes of textile materials were handled automatically.
- Displays the process schedule of a machine through computerized monitoring and allows the operator to sort/indicate the next lot.
- Jiggers are fully computerized with process control. The most outstanding aspects of a pad-batch dyeing system are the amount of dye, dye solution formulation, dye/color monitoring, and dye pickup control.
- It is also possible to finely control each parameter in less time by making quantitative mixing of dyes and other chemicals, temperature of dyeing bath, pressure and time of completion of dyeing etc.
Fully Automatic Laboratory Dyeing Machine
Lodo HT is one of the universal fully automatic Lab Dyeing m/c and it is ideal for tiny samples of yarn cones, bulk fibers, fabric beams etc. Lodo HT is made in Italy with highest quality standards, safety features and low environment impacts. Its main characteristics are its modular design, different configurations of automation levels to extend its automation level and dyeing repeatability to the highest level, so as to achieve the highest possible Right First Time (RFT). For this scope, some unique technological solutions are developed, all available on demand as optional accessories.
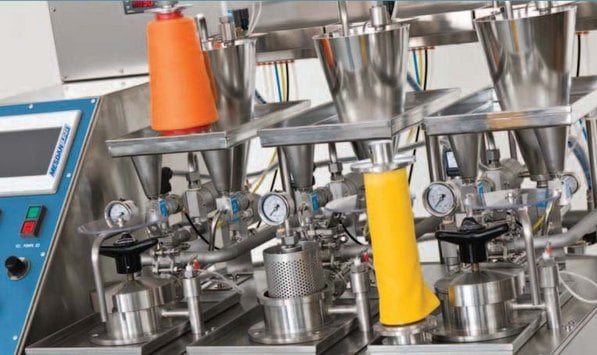
The dyeing units of Lodo HT can be equipped with an automatic dosing system consisting of one main tank (dye bath) and also three additional smaller tanks for the auxiliary products.
Its main features are- three versions available (manual, standard automation, full automation), from 1 to 6 independent units with 1000 or 2000 cc capacity. Atmospheric and extreme temperature dyeing (maximum temperature: +1350C), programmable and user-friendly PLC micro-processor with touch screen display and up to 50 programs memory capacity.
Every dyeing unit is supplied with automatic continuous washing system and drain of the dyeing bath, reversible circulation pump, automatic indirect water-cooling system by means of an electro valve.
Package Dyeing Automation
GALVANIN can supply robotic and automation system for brand new or dye house including the loading of raw bobbin into dyeing carrier, the unloading of yarn after dyeing process, the loading and unloading process of hydro-extractor, the loading of trolley into hot air dryer and therefore the final unloading after drying. The automation can even include automatic shuttle for the transportation of horizontal dyeing carrier or automatic bridge crane for the transportation of vertical dyeing carrier.
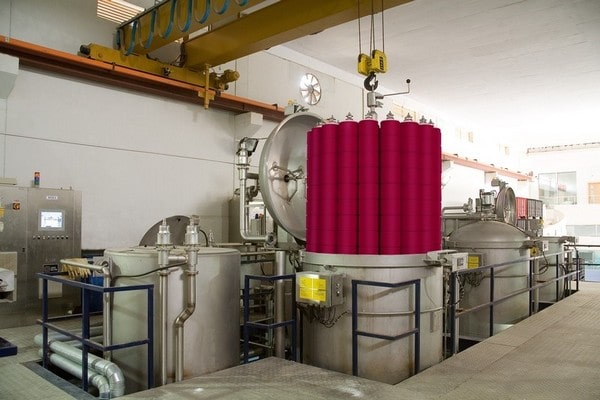
Auto Jigger Controller System
Jigger is a one kind of fabric dyeing machine. The auto jigger controller is a modified version with user-friendly features to convert any types of ordinary jiggers to automatic jiggers. It is a perfect substitute to the old mechanical counter type auto jiggers. Here operational controls are extremely user friendly. This is a microprocessor-based system with digital indication of fabric on both sides and number of cycles completed. It has auto and manual modes. If there are problems in the system, it can be switched to manual mode.
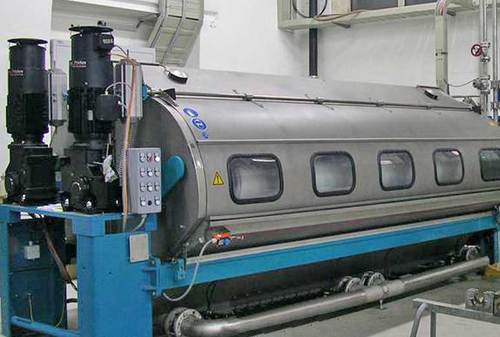
Automatic Dosing & Dispensing System for Dye House
Auto dosing system is an integrated system controlled by computer which involves all the recipe calculations needed for dyeing. All types of chemicals & auxiliaries, which are required for dyeing, are mixed in the dye bath automatically. The automatic dosing &dispensing system for dissolving huge amounts of powder chemicals and dyes from Color Services has several advantages. The system is devised for weighing dissolving and dispensing huge amount of powder dyestuffs, chemicals, safety and environmental requirements. The powder dyestuff or chemicals are often weighted (5 to 100 kg) automatically into the dissolving station. This is often followed by the controlled and auto-addition of water, up to 70 liters/minute. The mixed solution is automatically dispersed to the bathtub or the channel of dyeing machine. A totally automatic dispensing system for the package dyeing is another development toward dye-house automation. In 1986, Technorama introduced an automatic machine called Dosorama WSD for dispensing solid and liquid products. The first installation of auto-dispensing system is made at Park Valley dyers, Huddersfield, UK.
The benefits of automatic dispensing system are accuracy & precision, system integration, reproducibility, smart order processing, safe handling & mixing of materials etc.
Conclusion
The use of automated system & equipment in the dyeing industry has witnessed a sharp increase in recent years primarily due to world market demands for Right-First-Time (RFT) production of high quality products and lower production costs. These demands are achieved by consuming less water, dyes, chemicals & auxiliaries, less time and less energy, while maintaining the levelness of dyeing and also by reducing the environment pollution. At present, buyers are attracted to product, modern technology, automation quality as well as Eco-friendly industries, and are giving priority to factories that have Effluent Treatment Plant for orders. As a result, recently ETP is being set up in many industries.
References
- https://textilelearner.net
- Researhgate.net
- Academia.edu
- Technofashionworld.com
- Indiantextilejournal.com
- Fiber2fashion.com
Author of this Article:
Md. Imran Hossain
B.Sc. in Textile Engineering
Shahid Abdur Rab Serniabat Textile Engineering College, Barisal.
Email: mdimranhossain.te@gmail.com
Articles published by same author:
- Automation in Textile Industry: Impacts, Advantages and Disadvantages
- Applications and Impacts of Automation in Fiber and Yarn Manufacturing
- Application of Automation in Weaving Industry