Conversion of Chittaranjan Hand Loom into Power Loom
Authors:
Md. Rakibul Islam1, Mohammmad Shohan
Abdul Kayum Azad, Md. Al-Mamun &
Mahabub Sarker Zakir
Dept. of Textile Engineering,
City University, Dhaka, Bangladesh
Email: irakibul352@gmail.com1
Abstract:
- Purpose: The purpose of this experiment is to reduce production time/cost and also raise production.
- Methodology: Chittaranjan Hand Loom and modern motor were used in this experiment for conversion. An automatic motor was set up upper side of the machine to generate a power loom.
- Findings: Production rate was enhanced, production cost was reduced due to this experiment.
- Practical Implication: This is a practiced based experiment and the outcomes are beneficial to the personnel involved in textile industries who are responsible for woven fabric production.
- Limitations: Due to the poor instrumental facilities only few parts with electric motor was used in this experiment.
- Future Prospects: This experiment opened possible ways for the industrialist/technologist to further study in this field with the facilities of modern technology
1. Introduction:
1.1 Aim:
Our first priority was to create a loom machine by modifying an old machine which was running manually. So we got an idea of improving chittaranjan hand loom by our practical experience. We talked to people about the basic procedure of chittaranjan hand loom weaving machine and we followed up the primary & secondary motion & planned to remove those manual motions by using motor mechanism.
1.2 Objective of the Research:
From this research we wanted to construct a new machine that machine will work the same functions as chittaranjan hand loom & only the basic difference in this new machine it works automatically with the help of motor mechanism & electricity. Using this modified loom machine it will increase production capacity & minimize the time duration & labor cost also. It also focuses on the source of income for the poor people & unemployed peoples due to low cost of modifying of the machine.
2. Literature Review:
2.1 Background of the study:
As we went for a visit to one of our friend’s house he took us for visiting the loom area. While visiting we found some people were making sarees from Chittaranjan hand loom. We felt interesting and we went to them and discussed about the saree making procedures by Chittaranjan hand loom and took all basic information about it. Then an idea came out of preparing a power loom from Chittaranjan loom machine. We tried to make the power loom by using a motor instead of manual functioning. It may reduce the labor capacity, costing & reduce time also.
2.2 Loom:
Machinery for making fabric by weaving yarn or thread. A loom is a device used to weave cloth. The basic purpose of any loom is to hold the warp threads under tension to their way for the interweaving of the weft threads. [1]
2.3 Hand Loom:
A ‘handloom’ is a loom that is used to weave cloth without the use of any electricity. Hand weaving is done on pit looms or frame looms generally located in weavers’ homes. Weaving is primarily the interlacing of two sets of yarn – the warp (length) and the weft (width). The equipment used for this interlacing is the loom. [2]
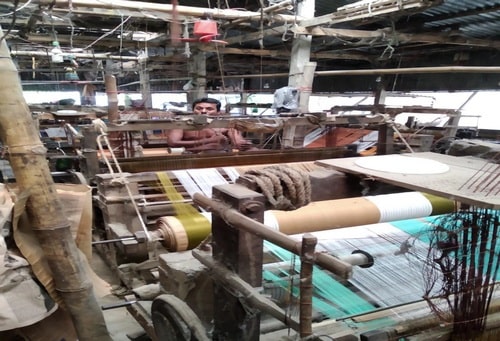
2.4 Types of Hand Loom:
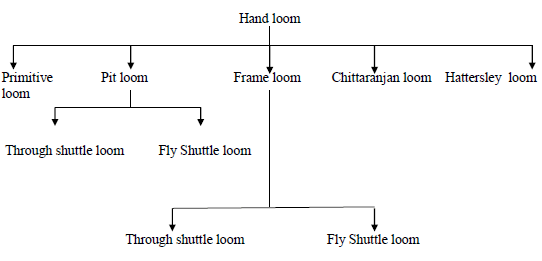
2.5 Chittaranjan Hand Loom:
Chittaranjan loom is one of the types of semi-automatic loom which is made of iron and wood. The terms which is commonly used in Bengali language is chittaranjan loom. Chittaranjan loom also known as Japanese loom. [3]
2.6 Features of Chittaranjan loom:
The common features of chittaranjan loom are in the below:
- Picking and shedding motion is used here as fly shuttle loom.
- The main characteristics of chittaranjan loom lie in its beating up, take up and let-off motion.
- A five wheel take up motion has been adopted to regulate picks per inch.
- For beat up two wheels upon the top shaft connect the slay at the two ends with two livers.
- Higher production rate is here.[4]
3. Theoretical Background:
3.1 Advantages of Chittaranjan Loom:
Chittaranjan loom contain some key advantages which are in the following:
- Chittaranjan looms more perfect for weaving coarse and medium fabric then finer yarns.
- This types of loom has 80% efficiency.
- Chittaranjan loom ensure uniformity in the insertion of picks per inch by the use of five wheel positive take up motion.
- An average can conveniently run this loom.
- This loom runs 120-140 picks per minute.
- These types of loom also ensure uniform beat up. [5]
3.2 Disadvantages of Chittaranjan Loom:
Different demerits of chittaranjan loom are
- Production rate is less over than modern loom.
- 5 wheel positive take up motion is used here which gives jerky motion.
- Chittaranjan loom is not an automatic loom.
- Precise control of fraction of picks is not suitable here. [6]
3.3 Power loom:
A power loom is a type of loom that is powered mechanically instead of using human power to weave patterns or thread into cloth. The power loom is an invention that combined threads to make cloth. Power looms were assembled in the weaving shed of a mill and driven by a steam engine by belts from overhead shafting.[7]
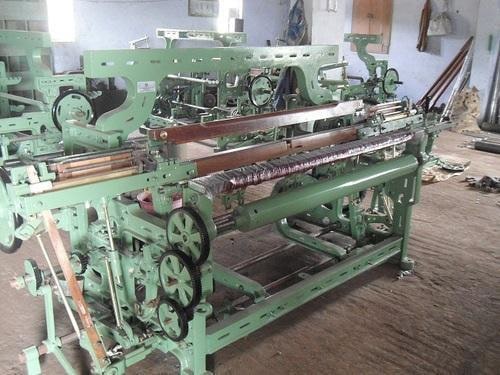
3.4 Types of Power Loom:
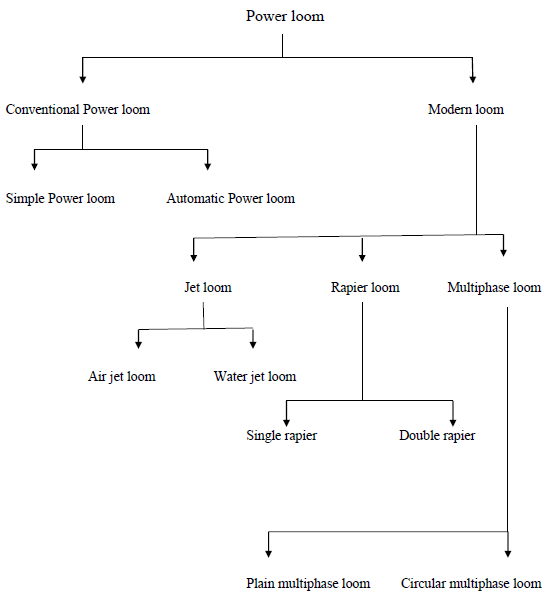
3.5 Features of Power Loom:
The main characteristics of power loom has mentioned in the following:
- It can be produced more complex design than hand loom.
- Power loom has higher production capacity than hand loom.
- This type of loom has needed more initial cost than hand loom.
- It has the risk of fire hazard.
- In case of power loom, shuttle is used for picking purpose.
- Hand loom is driven by electric power or steam.
- In power loom, jacquard, dobby and tappet shedding can be used here.
- Higher quality woven fabric can be produced here. [8]
3.6 Advantage of power loom:
- It works faster than hand loom
- Its production rate is higher than hand loom
- Its labor efficiency is lower than hand loom.
- Its production cost is low.
3.7 Disadvantages of power loom:
- Use of high electricity.
- Production will stop running in case of electric supply off.
3.8 Primary Motion:
- Shedding: The shedding is the temporary separation between upper and lower warp yarns through which the weft is woven. The shed is created to make it easy to interlace the weft into the warp and thus create woven fabric.
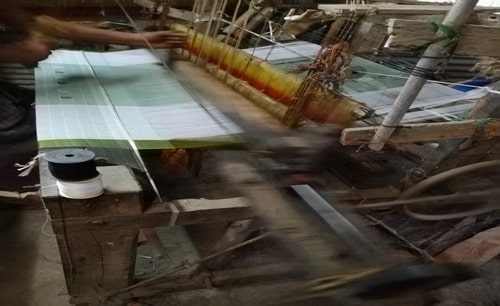
- Picking: Picking means inserting a weft thread across the warp through during weaving. Picking is the second primary motion in weaving. [9]
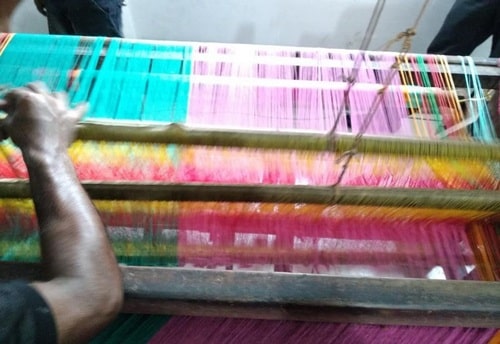
- Beating up: Beating up is the third and final primary motion in weaving; it performs driving the last pick of weft to the fell of the cloth. [10]
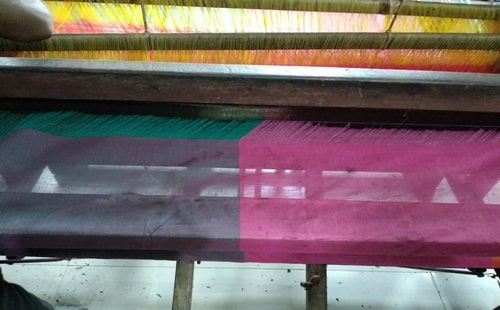
3.9 Secondary Motion:
- Let off: The motion which delivers the warp from the warp beam at the required rate that a suitable constant tension by unwinding it from a flanged bobbin called let off motion. [11]
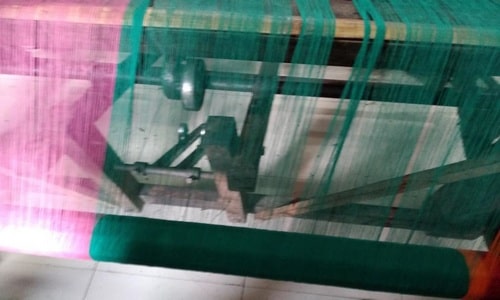
- Take up: The take-up motion withdraws the cloth from the weaving area at a constant rate so as to give the required pick-spacing (in picks/inch or picks/cm) and then winds it on to a cloth roller. [12]
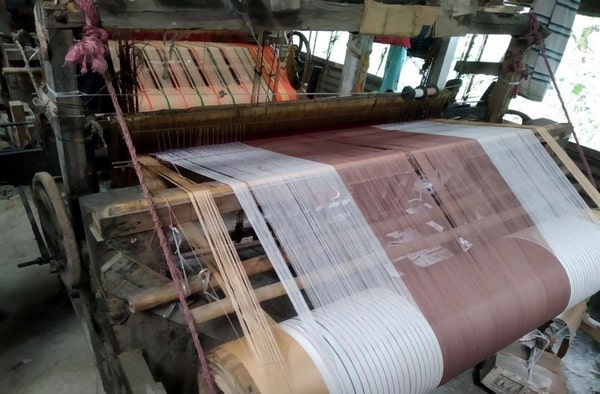
3.10 Difference between handloom and power loom:
Hand loom | Power loom |
1. It is driven by manually. | 1. It is driven by steam or electric power. |
2. Simple design can be produced. | 2. Complex design can be produced. |
3. Higher warp shed needed. | 3. Lower warp shed needed. |
4. Lower production capacity. | 4. Higher production capacity than hand loom capacity. |
5. Slow running speed. | 5. High running speed. |
6. Initial investment is low. | 6. Initial investment is high. |
7. Less number of design verities can be produced. | 7. More number of design verities can be produced. |
8. Shedding is done by pedal and picking and beating done by manual. | 8. Shedding picking and beating is done automatically. |
9. Less production. | 9. High production. |
10. Check and stripe fabrics are produced. | 10. Normally one color fabric is produced. |
11. Shuttle moves manually. | 11. Shuttle moves automatically. |
4.0 Materials & Method:
4.1 Different parts of hand loom:
- Heddles
- Head roller
- Warp
- Weft
- Front rest
- Backrest
- Heald shaft
- Shuttle
- Heald wire
- Cloth roller
- Cross beam
- Treadles
- Warp roller
- Take up motion handle
- Ratchet wheel
- Crosspiece
- Beater
4.2 Different parts use for Hand Loom & Power Loom:
- Heddles: It helps to hold two body stands.
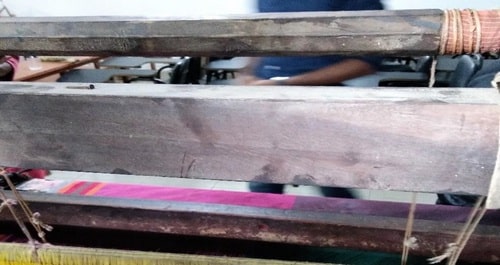
- Treadles: It helps to move heald shaft.
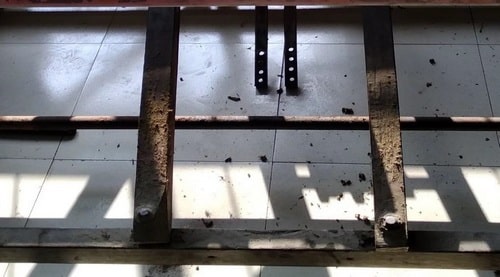
- Cross piece: It helps to hold treadles.
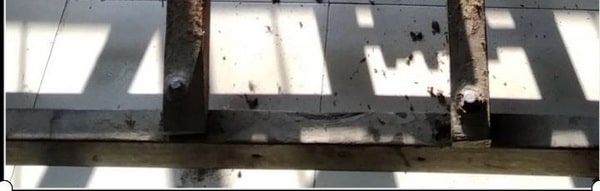
- Beater: It is used to separate and space the warp threads, to guide the shuttle’s motion across the loom, and to push the weft threads into place.
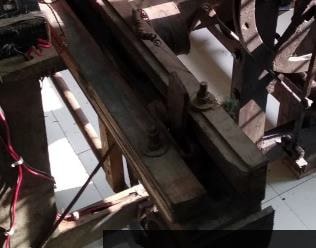
- Backrest: It helps to the warp yarn to pass through the heald shaft.
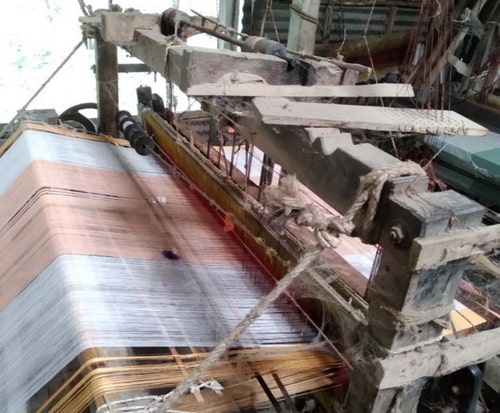
- Cloth Roller: It rolls the finished fabric. It creates tension in front side by this roller.
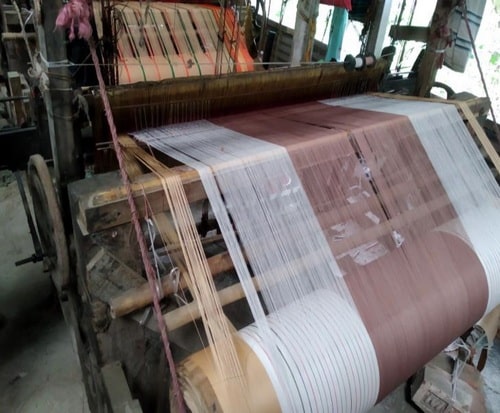
- Creel: It is use as stands of warp bobbin.
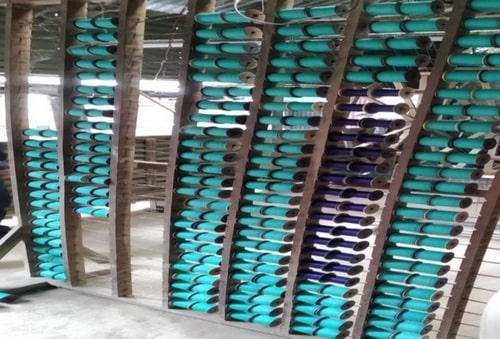
- Extra warp beam: It is use on caution of warp yarn breakage.
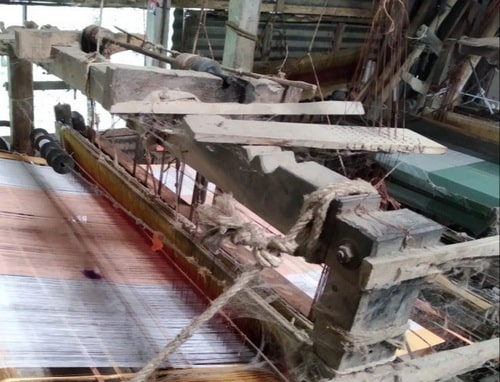
- Shuttle: A shuttleis a tool designed to neatly and compactly store a holder that carries the thread of the weft yarn while weaving with a loom. Shuttles are thrown or passed back and forth through the shed, between the yarn threads of the warp in order to weave in the weft. [13]
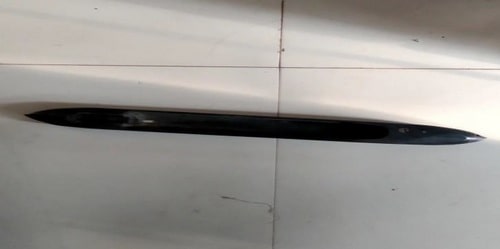
- Heald Shaft: This part is related to the shedding mechanism. The heald shaft is made of wood or metal such as aluminum. It carries a number of heald wires through which the ends of the warp sheet pass. The heald shafts are also known as ‘heald frames’ or ‘heald staves’. The number of heald shafts depends on the warp repeat of the weave. It is decided by the drafting plan of a weave. [14]
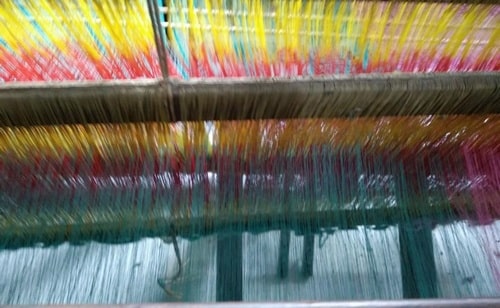
- Wood Temple Roller: The wood temple rollers is used in power loom to give up the grip to yarn used for manufacturing the cloth. Wood temple roller is used at the right end & left end of the power loom in temple box. [15]
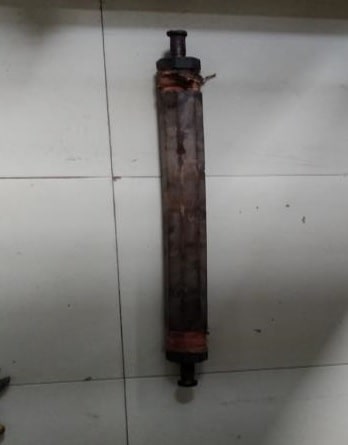
- Cotton Beam: It is used for raping weft fabric and also for creating some tension.
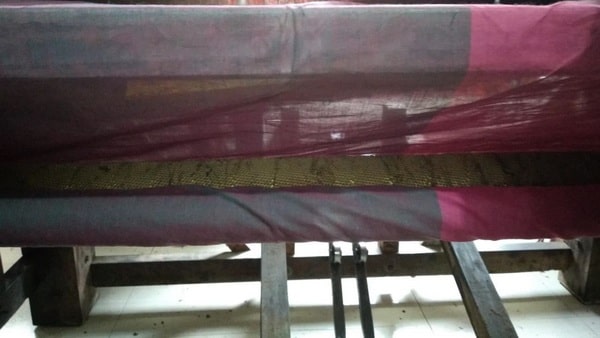
- Heald Wire: Heald wire is situated between heald shafts. It is used for pass the warp yarn from backrest to front rest.
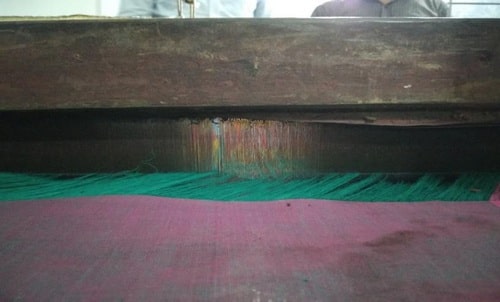
- Pirn: Weft yarn wound in pirn and pirn is used inside shuttle box.
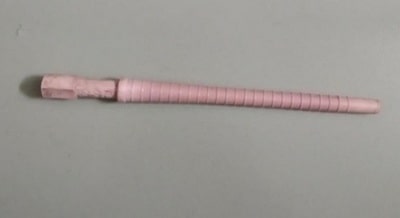
- Wood Stands: All body parts are attached in this portion. It is a heavy wood construction. It is one of the frame parts of power loom machine.
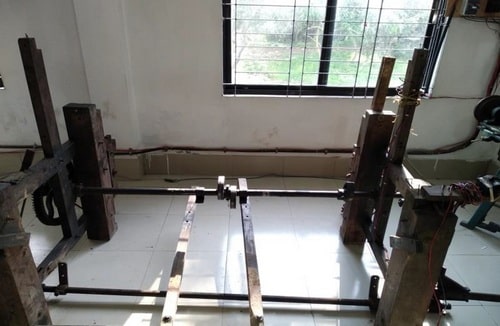
4.3 Equipment:
4.4 Different equipment used for power loom:
- Wire stripper: A wire stripper is a small hand tool device which is used for cut electric wire.
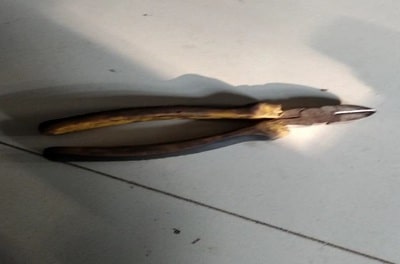
- Screwdriver: A screwdriver is used for installing or removing screws.
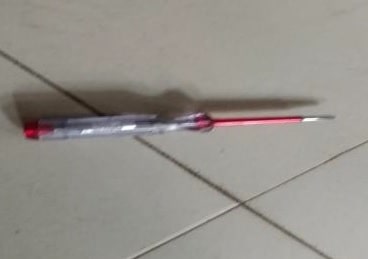
- Hammer: It is used for drive nail into wood and used for break material or shaping any material.
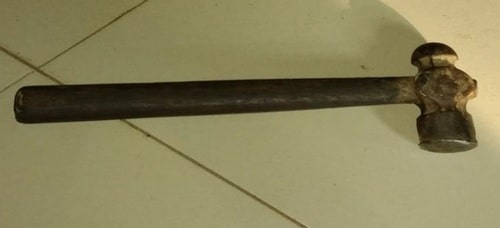
- Wrench: Wrench is used for tight nuts and bolts or keeps them from turning.
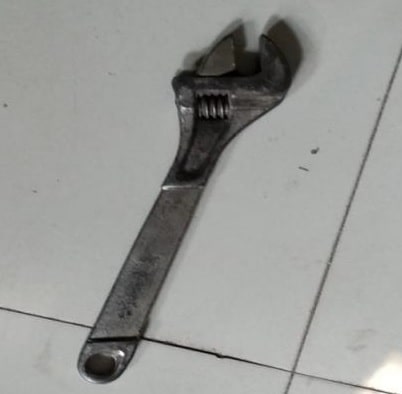
- Spanner: It is used for provide grips and tight nuts and bolts.
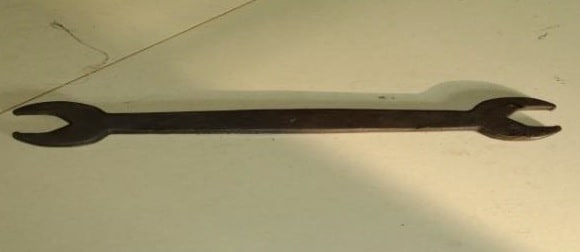
4.5 Method & Methodology:
4.5.1 Method of Chittaranjan Hand Loom:
Chaatittaranj an hand loom is one of the types of semi-automatic loom which is made of iron and wood. The terms which is commonly used in Bengali language is chittaranjan hand loom. Chittaranjan hand loom also known as Japanese loom.
A precise hand weaving technique, involving vertical or horizontal loom, which done by highly skilled labor. The basic concept of hand weaving to divide the warp threads and weft threads. The yarn is stretched and tied to the loom to create a taut warp. Labor start working from bottom to top, the labor weaves the weft and creating different pattern and texture. To create the bale, the fiber is wrapped around an iron rod during the weaving process and then cut to ensure equal height.
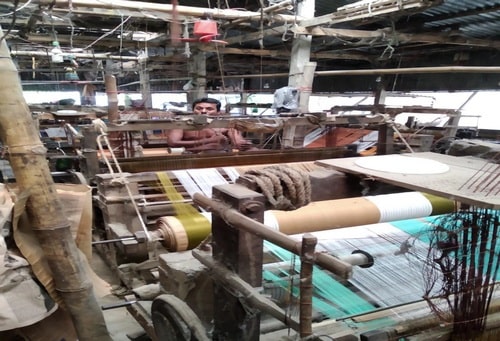
4.5.2 Method of Power Loom:
At first a wooden stand was set up. Then tablet is set up on the stand. After that a roller is set up where automatic gears are available. Front rest & back rest are placed on the top of the stand. A roller is attached on the wood frame stand where a wood temple roller is also situated. There is a frame where heald shaft is tied up with the help of rope. The heald shaft is attached with the foot tablet. There are two beaters in two side of the wheel. A 0.5 Hp motor in set on the left side frame. The wheel is adjusted with the motor pulley by belt with the beater. The motor is electrically connected with switch box. The switch box is set on the right side of the front rest with safety guard. The switch is connected with the main line. The warp yarn passes through back rest to front rest between heald eyes and wrapped into cotton beam. The warp yarn gets tension from the back rest with heavy material. The cloth beam also plays the role of tensioner for warp yarn. The weft yarn are wounded into pirn and placed into shuttle box. The shuttle box is placed to beater on the right side. When the motor is started the beater beats the shuttle in parallel direction in a specific space. By this process the weft yarn is placed between the warp yarns to prepare fabric.
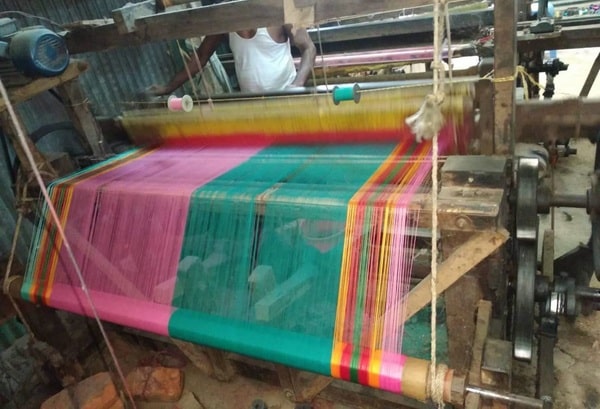
4.5.3 Modification parts of power loom:
- Motor: Here we used motor to remove hand motion.
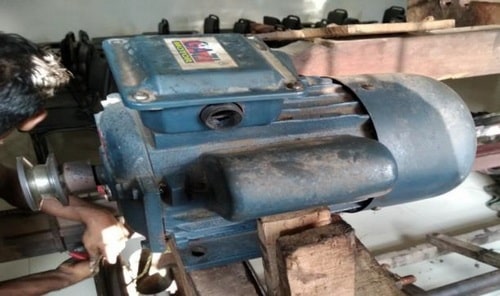
Brand Name: Gazi Motor
Power: 0.5 HP
- Wheel: Wheel is used for rotate the roller. It is also used for rotate the gear.
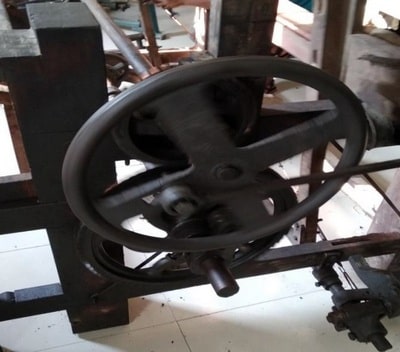
- Treadle: It is used for moving heald shaft upper and lower direction.
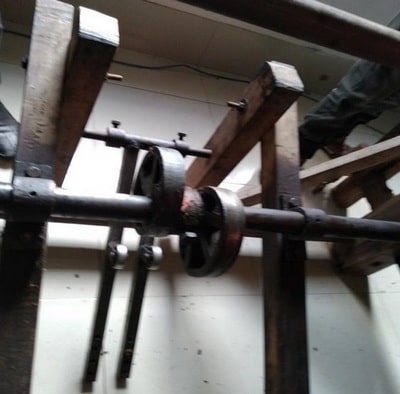
- Gear: It is used for move the roller and also used for move the shuttle right side to left side
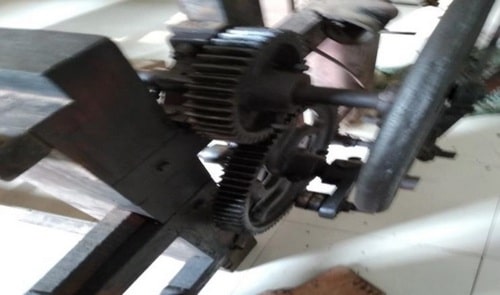
4.5.4 Primary motion
- Shedding: Here gear is used to remove the foot movements of treadle.
- Picking: Gear & wheel are used as modifying parts of picking by removing manual motions.
- Beating: Motor & wheel is used as the replacement of hand motion where hand was used to move the heddle.
4.5.5 Secondary motion
- Let off: Motor & gear is used to deliver the warp yarn from warp beam and it removed manual tensioning.
- Take up: The withdraw of cloth from weaving area is done only by motor which removed manual movements.
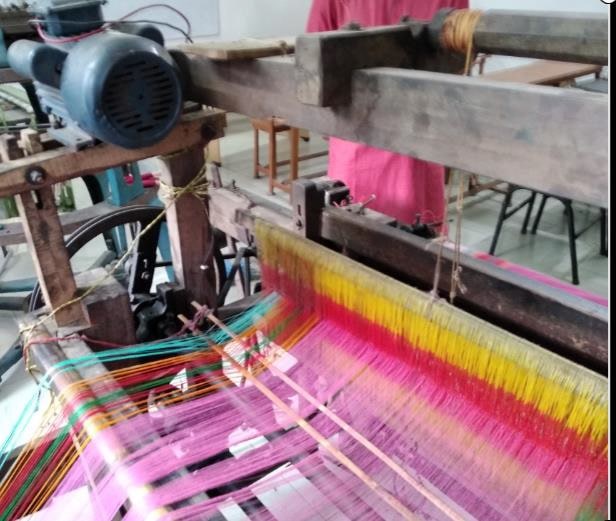
4.5.6 Method of power loom:
The first step in the process of construction is to build the loom frame of straight – grained dressed wooden beams, preferably 2″ by 4″ pine. First we erect two side stands, and connect these with other beams to form a box frame (thus the term “box loom” originated). The height of the side stands should be about 30″, the width 45″ and the cross pieces 34″ long— convenient dimensions for home use. The simplest method of joining these pieces is to connect them with metal plates and carriage bolts. Next we must fasten the bearings for the main shaft to the side frame; then line up the main shaft (1)—which should be of 1″ cold rolled steel— so that it will rotate easily.
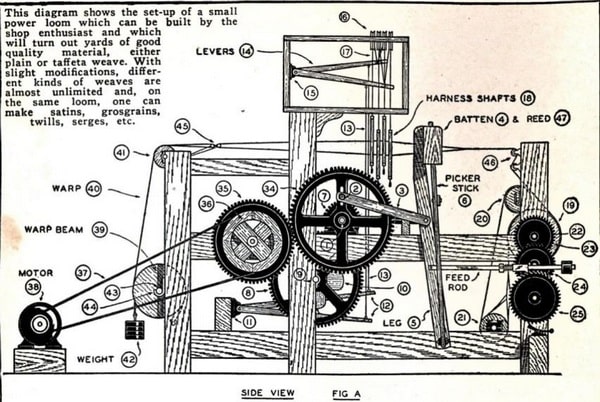
On one end of the shaft (1—Fig. B) we fasten a gear (34) about 14″ in diameter, with a threaded stud in a slot in a spoke located about 3″ from center (2 in Fig. A), which is called batten swing. The slot is for adjustment, so that the swing of the batten arm can be timed accurately. The wooden batten arm (3) is 1″ x 3″ x 14″, connecting to batten (4).
The batten (4) is a beam 68″ long on which a reed about 26″ in length is attached and centered (Figs. B and K). The batten rests on the batten leg (5), swinging on a pivot (a convenient stud on the bottom beam of the frame). On the same stud the picker stick, which swings back and forth with the batten, is fastened (Fig. B).
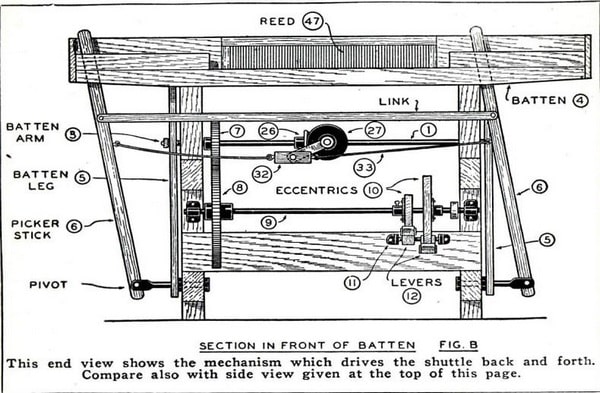
The gear (7) is put on the shaft first, of course, inside the loom frame; this connects with and drives gear (8), in turn clamped to shaft (9). The speed transmission of these gears is 1 to 4, which means that for four revolutions of shaft (1) there will be one revolution of shaft (9). This allows us to make any weave where the repeat is not over four picks.
Wooden or iron eccentrics (10), shaped as indicated in Figs. A, B and E, are joined to shaft (9). At every revolution one or the other eccentric presses down the desired lever (12). These levers are constructed of wood and go on a pivot placed in bracket (11), which should be attached to the cross piece of the frame in back of the shaft. Each lever has a roller located directly beneath shaft (9) – the rollers may be omitted if desired and the levers may be faced with metal.
A wire (13) is hooked to the end of the levers (12), which in turn connect to the wooden levers (14) situated at the top of the machine. Levers (14) are attached to the harness shafts (18) by cords (17) winding over rollers (16), by the method illustrated in Fig. J. By each revolution of the machine, the eccentrics (10) press or release levers (12), which lifts or drops the shafts (18).
The take-off beam (19), Figs. B and D, is about 6″ in diameter and should be covered with sandpaper. A shaft (22) for the entire beam, or a correctly centered stud on each side of it, is affixed through the frame extending far enough to give room for gear (23) to be fastened to the outside. The press roller (20) should be about 3″ in diameter, covered with felt. It should be hung in U-shaped iron guides on each side of the frame so that it can press the material down upon the beam.
Roller (21) should also be a beam of about 3″ in diameter, which is to take up the finished product. The simplest way possible of arranging the take-up is to connect (21) with (19) by a cross belt. A duplex transmission gear (24) is then used to connect gear (23) with the pick wheel (25).
The feed rod, connected to the batten supporting arms, has a dog which fits into the teeth of wheel (25); this operates the take-up beams, which move the finished woven material forward the desired distance, depending on the pick calculated to be put in the finished material.
Figs. B and D indicate the shuttle-drive arrangement. On shaft 1, somewhere near the center, a small bevel gear (26) is set to drive another bevel gear (27), which should be twice the size of (26). An iron or steel shaft (28) is then placed in bearings (29), situated at right angles to shaft (1), and a crank (30) is attached. About 4″ away from the center of (30) is placed a stud (31), which has a turnbuckle (32) pivoted in the center. In each end of this turnbuckle is fastened a screw-eye, to which is attached a strap, tied at the other end to the picker stick (6). These straps can be made of very heavy leather, cord or belting; the length can be determined when the crank is brought to a position where the stud (31) is vertically below the shaft (28). In this position, both straps should be stretched.
Drive gear (35), Fig. A, is fixed to pulley (36); the belt (37) is hooked up with a 1/3-H.P. motor (38).
The threads running the length of the material the warp are made up of a thickness to be decided upon. If we are going to weave a coarse or heavy material, we will use thick or heavy thread and a fewer number of threads per inch; but for a fine cloth, we require yarn or thread that is very thin. The threads are wound around a beam (39), Fig. A, about 5″ in diameter and a little less in length than the length of the loom.
A shaft (43) runs through the center of beam (39) and extends at each end so that it can be slipped into bracket (44) behind the loom frame.
Weights (42) are suspended from a rope, nearly encircling the beam and causing tension on the warp when the loom is in operation. The free end of the rope is fastened to a hook, attached to the frame.
After the warp is hung in the loom, it is passed over cylinder (41) and then each thread is alternately passed over and under two warp sticks (45), tied at the ends by cords in turn fastened to hooks in the frame. This prevents the sticks from moving too far forward when the threads of the warp move as the goods are woven. From these sticks, each thread of the warp is entered into the harness.
The purpose of the warp sticks is to have the warp divided alternately, one thread up and one thread down; so that, when a thread breaks and the repair is made by tying on an additional piece of similar thread, it can be passed under or over the picker stick. In this manner, what is termed “a straight warp” is always maintained.
The harness (18) comprises a steel frame, which supports the leases—each of wire, flat steel, or heavy cable-woven thread, in the center of which is a metal eye or heddle, similar to but larger than the eye of a needle. Through this eye a thread of the warp is passed; we need as many leases as there are threads in the warp, each thread of the warp passing through its individual heddle controlling the raising or lowering of the warp threads in process of weaving.
The leases are hung or mounted on the harness frames, and the number of frames is determined by the type of weave. The one described is composed of four harness frames.
From the harness, the warp threads are passed through the reed (47), Figs. B and C; this is a comb-like arrangement of flat steel. The spaces between the flat pieces of steel wire in the reed are called dents. Through this space are passed a given number of threads, usually two, three or four, depending upon the coarseness or fineness of the yarn in the warp, and also on the quality of the material to be woven.
After the warp threads are passed through the reed, they are then laid over the bar (46) on the back of the breast beam and fastened around the take-up roller.
We are now ready to consider the shuttle: this is the housing for the supply of yarn that will compose the woof threads that run across the material to interlock and hold in place the warp threads. This makes up about fifty per cent of the material.
This shuttle is thrown along the batten by the picker sticks (6). The mechanism of the loom is so set and timed that the shuttle travels when the threads of the warp form a shed or opening for the shuttle to pass through, and when it does so, the filling thread is put in position, and then packed into place by the reed (47), which pushes the filling forward.
This entire operation, which is one revolution of the loom, is designated as a “pick.” The next pick, or the return of the shuttle to the other side, carrying the thread across, is when the loom again revolves one turn. Thus, the shuttle alternates from one side to the other.
The supply of yarn or filling placed in the shuttle is wound on a tube or quill, and its tension regulated by a series of fine strings in the shuttle. As the material is woven, the take-up roller is operated by the gears (21 to 25) designated as the take-up motion, and moves the finished woven material forward.
Such parts as shuttles, quills, harness, heddles, etc., should be purchased at any loom supply house.
Aside from the parts specifically detailed, considerable latitude in dimensions and materials is permitted; hence no specific dimensions for the parts are given in this article.
The editors would like to hear from those readers who build and operate this loom.
We set up our Project (Chittaranjan Hand loom to Power loom) by attaching nuts, bolts, metal frame, wood frame, wheel, shuttle and motor(0.5 Hp) at Power loom. We made a plan to build a power loom in purpose to remove manual functioning & increase production & decrease cost of labor.
The original power loom however met its end at Nab Wood near Shipley. We brought a revolutionary hand loom. Weavers were fearful for their future livelihood. We manufactured a loom successfully& delivered the power loom. We went into full time production by using our power loom.
5.0 Result & Discussion:
5.1 Result:
This is the finished production of our modified power loom machine.
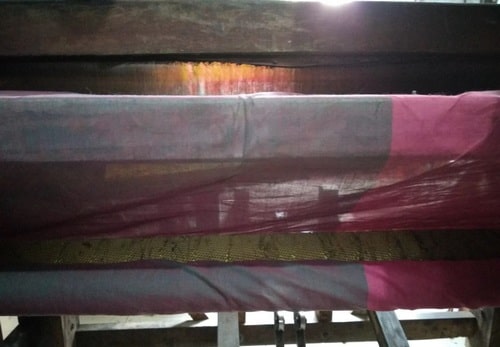
After the production from our modified power loom we can easily compare between Chittranjan Hand loom with our modified power loom from Chittranjan Hand loom.
Chittranjan Hand loom | Results |
Efficiency | Low |
Production Quantity | Lower Average |
Production Cost | More |
Time Cost | High |
Labor cost | High |
Speed | Low |
Maintenance cost | Medium |
Remarks/Feedback | Below Average |
Modified Power Loom | Results |
Efficiency | High |
Production Quantity | Medium |
Production Cost | Average |
Time Cost | Low |
Labor cost | Low |
Speed | High |
Maintenance cost | Medium |
Remarks/Feedback | Good |
5.2 Discussion:
Our modified Power loom works very similarly to the original chittraranjan handloom. Our modified Power loom operated by electric power.
A power loom is a type of loom that is powered mechanically instead of using human power to weave patterns or thread into cloth. The power loom is an invention that combined threads to make cloth. Power looms were assembled in the weaving shed of a mill and driven by a steam engine by belts from overhead shafting. Power looms were a major advance over the hand looms used before.
A powerloom is mechanized loom which runs by steam or electric power. The looms are driven by a steam engine by belts which lead to more effective and efficient output, plus higher quality of fabric produced compared to handlooms. The handlooms, on the other hand, are used to weave fabric using hand and loom made from wood and the resultant yarn varies according to the materials used and the skill of the weaver, which may result in a less effective fabric. The handloom is the oldest type of loom used for weaving, thus cannot produce complex designs like powerlooms.
So, there are many basic differences between handloom & power loom.
Though out the research of both loom we can find out power loom is more useful than hand loom because of its production capacity efficiency & minimization of time & labor cost.
6. Conclusion:
Conversion of chittaranjan hand loom to power loom is an experiment to reduce time & labor cost with the increase of production. It was created on a slight change of some parts. It was different and gave a good result in production in less time than hand loom. It can be used in small Industry for woven fabric productions & also will be beneficial. It will also produce saree same as the chittaranjan hand loom. It will create a field for unemployed people with low capital. But there are some limitations due to few parts & equipments with an electrical issue. If the electrical supply is not interrupted then there is no issue of production loss. This experiment will open some possibilities for Industrial & technologists for future study & development in the field of modern technology.
References:
Collection: From Hand Loom Workshop, Location: Kazibari, Kalihati, Tangail.
[1] ‘Parts of Loom?’, Last edited on [2019],[Online]. Available: https://textilelearner.net/different-parts-of-loom-and-their-functions/; [Accessed: June 11,2019;]
[2] ‘What is hand loom?’Last edited on [2019]. [Online]. Available:https://www.dacottonhandlooms.in/know-handloom/[Accessed: June 12, 2019]
[3] ‘What is chittaranjan hand loom?’Last edited on [2019]. [Online]. Available https://textilechapter.blogspot.com/2016/11/chittaranjan-loom-weaving-definition-features-advantage-disadvantage.html[Accessed: June 14, 2019]
[4] ‘Features of Chittaranjan hand loom? ‘Last edited on [ 2019]. [Online]. Available:https://textilechapter.blogspot.com/2016/11/chittaranjan-loom-weaving-definition-features-advantage-disadvantage.html [Accessed: June 14,2019]
[5] ‘What are the advantages of chittaranjan hand loom? ‘Last edited on [2019]. [Online]. Available:https://en.wikipedia.org/wiki/Shed_(weaving)\[Accessed: June 14,2019]
[6] ‘What are the disadvantage of chittaranjan hand loom? ‘Last edited on [2019]. [Online].Available:https://textilechapter.blogspot.com/2016/11/chittaranjan-loom-weaving-definition-features-advantage-disadvantage.html[Accessed: June 15, 2019]
[7] ‘Definition of power loom? ‘Last edited on [2019]. [Online]. Available: https://textilelearner.net/difference-between-handloom-and-power-loom/ [Accessed: June 16, 2019]
[8] ‘What are the features of power loom? ‘Last edited on [2019]. [Online]. Available: https://textilechapter.blogspot.com/2016/11/hand-loom-power-loom-definition-features-characteristics.html[Accessed: June 17, 2019]
[9] ‘Definition of picking? ‘Last edited on [ 2019]. [Online]. Available:http://www.definetextile.com/2014/04/picking.html[Accessed: June 18, 2019]
[10] ‘Definition of Beating up? ‘Last edited on [2019]. [Online]. Available:http://www.definetextile.com/2014/04/beating-up.html[Accessed: June 19, 2019]
[11] ‘What is let off? ‘Last edited on [2019]. [Online]. Available:https://textilelearner.blogspot.com/2011/06/take-up-motion-let-off-motion-secondary_5888.html[Accessed: June 11, 2019]
[12] ‘what is take up motion?’Last edited on [ 2019]. [Online]. Available:http://www.definetextile.com/2014/04/let-off-motion.html[Accessed: June 22, 2019]
[13] ‘Definition of shuttle?Last edited on [2019]. [Online]. Available:https://en.wikipedia.org/wiki/Shuttle_(weaving)[Accessed: June 25, 2019]
[14] ‘Definition of heald Shaft’Last edited on [2019]. [Online]. Available:https://textilelearner.blogspot.com/2011/08/important-parts-of-loom-heald-shaft.html[Accessed: June 28, 2019]
[15]‘what is temple roller?’Last edited on [2019]. [Online]. Available: http://www.viwtexpart.com/temple_roller.html[Accessed: June 29, 2019]